TECHNICAL PAPER #31
UNDERSTANDING BRIQUETTING
By
Mac Cosgrove-Davies
Technical Reviewer
Dr. Ben Bryant
Published By
VITA
1600 Wilson Boulevard, Suite 500
Arlington, Virginia 22209 USA
Tel:
703/276-1800 . Fax: 703/243-1865
Internet: pr-info@vita.org
Understanding Briquetting
ISBN: 0-86619-233-6
[C]1985, Volunteers in Technical Assistance
PREFACE
This paper is one of a series published by Volunteers in
Technical
Assistance to provide an introduction to specific
state-of-the-art
technologies of interest to people in developing countries.
The papers are intended to be used as guidelines to help
people choose technologies that are suitable to their
situations.
They are not intended to provide construction or
implementation
details. People are
urged to contact VITA or a similar organization
for further information and technical assistance if they
find that a particular technology seems to meet their needs.
The papers in the series were written, reviewed, and
illustrated
almost entirely by VITA Volunteer technical experts on a
purely
voluntary basis.
Some 500 volunteers were involved in the production
of the first 100 titles issued, contributing approximately
5,000 hours of their time.
VITA staff included Maria Gianuzzi as
editor, Suzanne Brooks handling typesetting and layout, and
Margaret Crouch as project manager.
The author of this paper, VITA Volunteer Mac
Cosgrove-Davies, is
a mechanical engineer currently working for the Carl T.
Jones
Corporation in Springfield, Virginia.
He has traveled in Central
and South America and has a keen interest in appropriate
energy
technology. The
reviewer is also a VITA Volunteer. Dr.
Ben Bryant
is the professor of wood and fiber utilization technology at
the
College of Forest Resources, University of Washington,
Seattle,
and president of AFPITA, a non-profit technology transfer
company.
In addition to teaching and research in the forest products
field, he has invented structural building panels made of
wood and fiber, consulted extensively in the forest products
industries, and performed studies in 22 developing countries
in
the area of approporiate technology transfer.
His group developed
the compound lever briquetting press.
VITA is a private, nonprofit organization that supports
people
working on technical problems in developing countries.
VITA
offers information and assistance aimed at helping individuals
and groups to select and implement technologies appropriate
to
their situations.
VITA maintains an international Inquiry Service,
a specialized documentation center, and a computerized
roster of volunteer technical consultants; manages long-term
field projects; and publishes a variety of technical manuals
and
papers.
UNDERSTANDING BRIQUETTING
By
VITA Volunteer Mac Cosgrove-Davies
I. INTRODUCTION
In many parts of the world, the primary source of energy for
such
vital activities as cooking and space heating is burning
wood and
other agricultural products.
An increasing population using a
dwindling resource of combustible biomass materials will
eventually
result in a shortage of those materials unless steps are
taken to reverse the trend.
One means of making more efficient use of existing resources
is
through the use of briquetting.
Briquetting involves collecting
combustible materials that are not usable due to a lack of
density,
and compressing them into a solid fuel of a convenient
shape that can be burned like wood or charcoal.
Materials such as
sawdust, wood bark, rice husks, and straw have been
successfully
briquetted.
During the first and second World Wars, households in
several
European countries employed a simple lever-operated
briquetting
press that used soaked waste paper and other combustible
domestic
waste as a feed stock.
Today's industrial briquetting machines,
although much larger and more complex, operate on the same
general
principles.
Although briquetting has been widely used in the
metallurgical
industry to recover metal filings, shavings, and scraps that
would otherwise be of little value, this paper is concerned
solely with the briquetting of combustible materials for
fuel.
The focus is on simple technologies that can be employed on
a
small to intermediate scale.
II. OPERATING
PRINCIPLES
Briquetting is one of several compaction technologies in the
general category of densification.
In densification, a material
is compressed to form a product of higher bulk density,
lower
moisture content, and uniform size, shape, and material
properties.
There are two ways that compaction can be accomplished:
with and without a binder.
One must have something to make the material stick together
during compression.
Otherwise, when the briquette is removed from
the mold, it will crumble to pieces.
This fastening agent is
known as a binder.
In some cases, most commonly under high temperature
and/or pressure, a material can act as its own binder.
Wood, for example, becomes plastic and can be briquetted
without
a binder under such conditions.
Many of the processes considered
here, however, will require the addition of a binder.
In most cases, the process of briquetting will consist of a
series of steps:
1.
Collecting material to be densified
2.
Preparing material
3.
Compacting
4.
Removing, drying or cooling, and storing
COLLECTION OF MATERIALS TO BE DENSIFIED
As mentioned above, there is a wide variety of materials
that can
be densified. Some
can be bundled, <see figure 3> or tied together, rather than
briquetted. A
partial list is included below.
o
jute
o rice
husks o
coffee husks
o
coal dust
o alfalfa
o
some nut shells
o
sisal
o bagasse
o
dung
o
wood wastes
o straw
o
vines
-
shavings o
paper waste
o municipal waste
-
sawdust o
peat
o sunflower
husks
- bark
o
olive residue
o
fish waste
- twigs
o
hemp o
coconut dust
o
coconut fiber
o peat
o
cotton sowing
(coir)
o
food processing
o
leather waste
waste o
charcoal fines
It should be noted that the use of industrial or automotive
waste
oils should be avoided since in many cases such oils contain
additives that can give off toxic fumes when burned.
If such oil
waste is to be used, it should be thoroughly checked by a
competent
laboratory first.
In general, any material that will burn but is not in a
convenient
size, shape, or form to be readily usable as fuel is a good
candidate for briquetting.
It may be necessary or desirable to
make briquettes of more than one material.
PREPARATION OF THE RAW MATERIAL
Once the raw material is collected, it must be assembled in
a
central location for processing.
The method of preparation depends
somewhat on the particular material being briquetted, but
the procedure generally includes some or all of the
following
steps.
SIZE REDUCTION
The raw material is first reduced in size by chopping,
crushing,
breaking, rolling, hammering, milling, grinding, cutting,
etc.,
until it can pass through a screen or reaches a suitably
small
and uniform size.
Since this process consumes a good deal of
energy, this size reduction step should be as short as
possible.
Indeed, with some materials this step may not even be necessary.
DRYING
Although the feed stock fed to the briquetting press is
often
wet, it may still be necessary to dry the stock before
mixing it
with the binder.
Drying can be done in the sun, with a heater, or
by using heated air and a rotating drum.
You can dry the material
before or after size reduction.
PREPARATION OF FEED STOCK
The method of mixing the raw material with the binder to
produce
a feed stock can vary widely.
Anything from a simple trough and
hoe to a modified commercial cement mixer can be used.
A ribbon
mixer for small-scale production is shown in Figure 1.
You must determine the correct propportion of raw material
to
binder before starting full-scale production.
This is best accomplished
by a trial and error method of making several briquettes
with different mixtures of binder material, then testing
each for mechanical strength and burning properties.
The cost of the binding material can be critical to the
economic
success of the project, so the smallest amount of binder
necessary
for an acceptable briquette should be used.
Although a
combustible binder is desirable, it is possible to use a
noncombustible
binder with good results.
Alternative uses of the
binder must be weighed against the value of the final
product as
an energy source.
The following is a partial list of binding
materials:
Combustible
Binders Non-combustible
binders
o
natural or synthetic
o slime
resins
o clay
o
tar
o mud
o
animal manure o
cement
o
sewage mud
o
fish waste
o
algae
o
starch
CARBONIZATION
In carbonization, a biomass material (usually wood) is
heated to
very high temperatures but is not given enough oxygen for
the
material to burn.
This processs produces charcoal.
The briquetting process can be used with carbonization to
produce
briquettes made wholly or partially of charcoal.
The briquettes
can be made using charcoal fines or ash as part of the feed
stock, or the briquettes can be compacted with any of the
raw
materials listed above and then carbonized.
The first method wil
probably produce a more consistent product.
The second method
may result in briquettes that are too fragile to handle
without
creating excessive dust.
COMPACTION
The next step, compaction, can be done in many ways.
The following
section on design variations will describe several
possibilities.
A basic overview is given below.
In general, a supply of prepared feed stock is loaded into a
chamber, the chamber is covered with a close-fitting top,
and
pressure is applied to compress the feed stock.
The pressure
applied can be anywhere from 0.5 to 1,200 kilograms per
square
centimeter (kg/sq cm) depending on the process
employed. In some
cases, the feed stock is heated to aid in the binding.
Another method of compaction, employed by some of the more
sophisticated
briquetting machines, is to heat the feed stock and
then extrude it.
Extrusion is a process whereby the feed stock is
forced through a small opening at high pressure.
The result is a
continuous log that can be cut to any length.
The advantage of
extrusion is that it is a continuous process that can
produce
briquettes in many shapes and sizes.
Disadvantages include the
need for high pressure, temperature, and energy consumption,
as
well as the relatively complex machinery involved (see
Figure 2).
A handful of soaked paper or other feed stock is taken from
the
mixing vat and hand-molded into spherical briquettes.
In some
areas, dung is shaped by hand for use as fuel.
Formed briquettes
are sun dried before use.
These briquettes will burn longer if
wood ash containing some charcoal is added to the feed
stock.
WROUGHT IRON BRIQUETTING PRESS I
This is the first of the briquetting presses.
It utilizes a
mechanical lever to apply greater pressure than is possible
with
hand molding. This
press also utilizes waste paper. Soaked
paper,
preferably with wood ash added, is put in the mold and
pressed.
Briquettes are then removed and sun dried.
Finished briquettes
are spherical, about 5 cm in diameter and weigh about 30
grams.
WROUGHT IRON BRIQUETTING PRESS II
This press provides greater compaction than the Wrought Iron
Press I because the compression face is pressed deeper into
the
mold form. The basic
press is again easy to make, taking approximately
four to five hours and five to eight kg of iron.
The
length of the lever arm will determine the briquetting
pressure.
The mold should be sturdy enough to handle the pressure created
by the lever. Any of
the briquetting materials given above can be
used in this press.
Modifications can also be made to yield
different shapes depending on the skill of the manufacturer.
Briquetting feed stock is poured into the mold and the lever
is
pushed down, compressing the briquette.
The lever is then lifted,
the base plate removed, and the finished briquette is pushed
through and then placed in the sun to dry.
TUBE-PRESSES
Metal or plastic pipe provides a good briquetting mold since
it
produces cylindrical briquettes.
The tube presses illustrated
(see Figure 4) consist of a tube mounted vertically on a
platform
ubr4x7.gif (600x600)
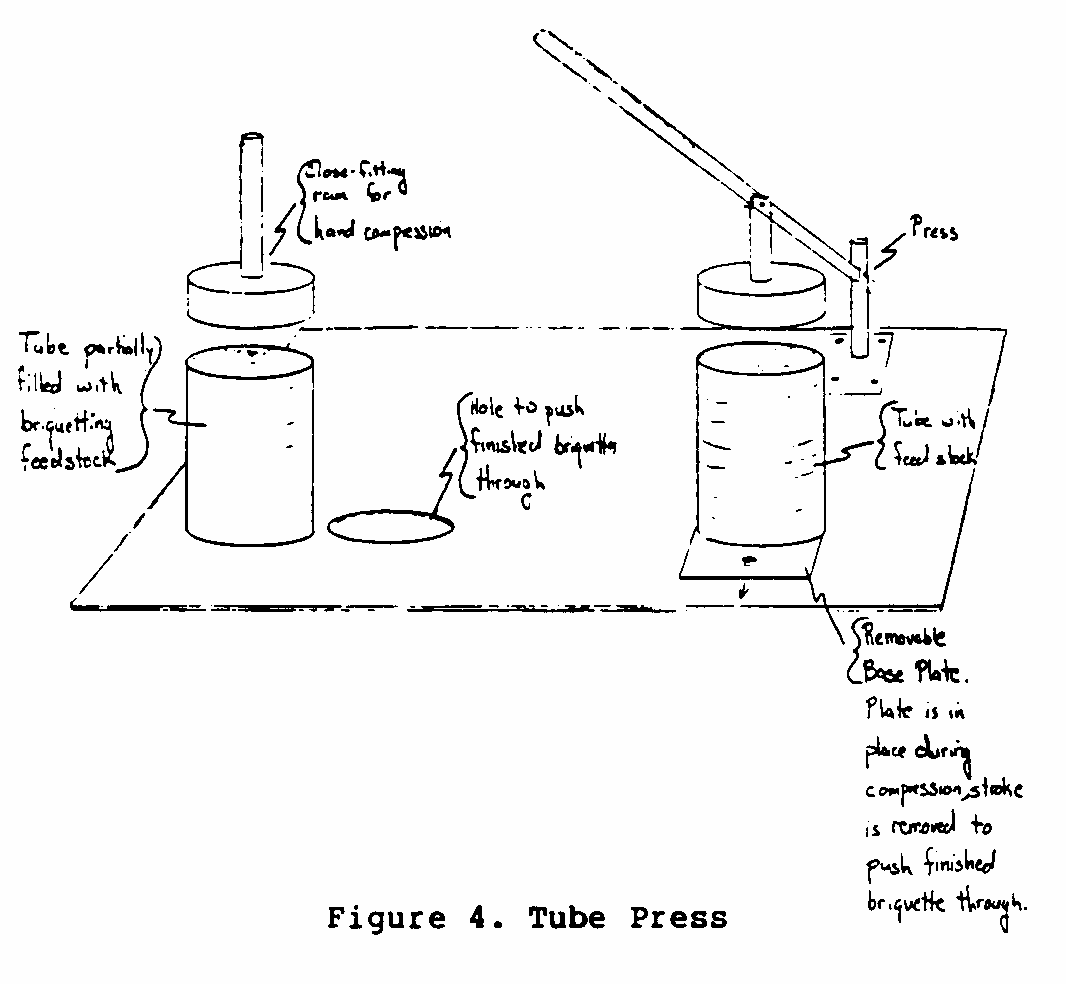
and a close fitting ram used for compaction.
The basic design can
be varied considerably, as the figure indicates.
Feed stock is poured into the tube and compressed with the
ram.
The tube is then positioned over a hole (or a slide is
removed)
below the tube exposing a hole) and the briquette is pushed
through. Briquettes
are then dried in the sun before storage and
use.
EARTH RAMS
Presses currently in use for making stabilized earth blocks
might
be modified to make briquettes from a mixture of a clay
binder
and charcoal dust or coal dust.
The Combustaram, similar to the
CINVA-Ram and Tersaram, is commercially available or can be
manufactured locally (see Figure 5).
ubr5x8.gif (600x600)
The lever arm is put in the open position, feed stock is
poured
into the molds and the lever is then quickly pushed up, over
the
top of the press, and down.
This movement positions the top of
the press and compresses the briquettes on the downward
stroke.
The lever is then moved back to the original position and
again
pushed down, thus forcing the briquettes out of the
molds. Finished
briquettes are set in the sun to dry.
The process requires
at least two workers.
COMPOUND LEVER PRESS
This press incorporates the principles of both the wrought
iron
briquetting press and the tube press.
Made of wood, the compound
lever multiplies the effectiveness of a simple lever.
Enough
pressure is generated when chopped, biodegraded, or finely
divided fibrous material is used in the damp or wet state to
eliminate the need for a binder.
The filled mold with the plunger inserted is initially
placed
toward the rear of the main lever to take advantage of the
maximum
stroke. After
initial compaction, the mold is moved to the
forward position for final pressure application.
The mold is
perforated to allow for escape of excess fluids, and a dowel
in
the face of the mold assembly places a center hole, improves
combustion of the briquette.
RICE HUSK EXTRUDER
This device is designed specifically to make fuel logs from
rice
husks. The extruder,
powered by a 20 HP electric motor, works
best with husks that have been ground and/or dried to reduce
moisture content.
The device measures 1.5 x 2.75 x 1.1 meters,
requires one or two workers, and produces 150 kgs of fuel
logs
per hour. The rice
husk fuel log extruder is relatively new and
has not yet been manufactured outside of Thailand.
Once the device is warmed up, the operator must keep the
machine
continuously supplied with prepared husks.
The operator must also
stack the finished logs and monitor the temperature of the
device's
heating unit. The
machine is designed to operate 24 hours
a day. Because of
the large volume of rice husks required to
keep the machine in continuous operation, this device may be
best-suited to large rice processing centers.
INDUSTRIAL BRIQUETTING MACHINES
Industrial briquetting machines densify waste produced in an
industrial setting.
These machines produce a wide variety of
products--briquettes, pellets, cubes, logs.
Quite often, machines
used for producing animal feed pellets can be modified for
fuel
pellets. Many do not
require binding materials. In addition,
several manufacturers offer a consulting service to
determine
which of their models is most appropriate for a particular
application.
Manufacturers should be contacted for more information on
their products.
V. COMPARING THE
ALTERNATIVES
Briquetting or densification is only one of several
technologies
that should be considered for the use of agricultural and
biomass
waste. Alternatives
include:
1. Fertilizer or
Soil Conditioner: The use of biomass waste for
energy production can deprive the soil of important
conditioning
agents, and the long-term impact of this deprivation must be
carefully studied.
2. Livestock Feed:
In some cases, the potential briquetting
material could be used as food for local livestock that
could be
used as a source of food or as work animals.
3. Bacterial
Fermentation for Alcohol Production: In
aerobic
fermentation, bacteria act to break down organic materials
in the
presence of oxygen.
This process can produce alcohol, which is an
attractive fuel because of its high energy content.
It is also a
liquid and therefore relatively easy to handle.
Research into
fermentation has progressed rapidly in the past several
years.
The economics of alcohol production favor large-scale
facilities
and this technology is not recommended on the village scale.
4. Anaerobic
Digestion for Methane Production: Anaerobic digestion
differs from aerobic digestion in that in anaerobic
digestion
the bacteria acts in the absence of oxygen.
The product of
anaerobic digestion is methane, a high-heat, clean-burning
flammable
gas similar to natural gas.
However, it requires a relatively
large initial investment in equipment and special storage
and handling, as well as a gas-burning stove.
Several countries,
notably China and India, have developed simple small-scale
digesters.
5. Gasification:
When a combustible material is raised to a very
high temperature without sufficient oxygen for combustion to
take
place, reactions occur that produce a combustible gas,
liquid
products, and charcoal or ash.
These processes of thermal decomposition
are known as gasification, pyrolysis, and carbonization
respectively.
Gasification can be performed on biomass
waste, but in general it requires a large-scale operation to
be
economically feasible.
6. Pyrolysis:
As mentioned above, pyrolysis is the process
of
producing a liquid when a combustible solid is heated
without
enough oxygen for complete combustion.
Large-scale plants exist,
and pyrolysis can also be performed on a small scale in
conjunction
with a retort for making charcoal.
The products of
pyrolysis, such as oils, tars, and resins, are useful in
various
industrial, commercial, and household applications.
7. Suspension
Burners: These are burners in which ground combustible
materials are mixed with air blowing up from the bottom of
a combustion chamber and burned in suspension.
They effectively
supply a relatively clean, hot gas than can be used in dry
kilns,
power boilers, veneer dryers, and other processes.
They are not
recommended for household use, but may be appropriate in a
light
industrial setting.
8. Fluidized Bed
Combustors: In a fluidized bed
combustor, air
is blown up from the bottom of the combustion chamber, but
in
this case the combustion chamber is partially filled with a
granular material such as sand.
The air being forced up through
the sand circulates the sand as it if were
"boiling." When
combustion takes place in this system, the sand acts as a
bed on
and in which the combustible material burns.
This system is more
flexible than the suspension burner because the feed stock
need
not be finely ground or even of a consistent size.
Fluidized bed
combustors also represent a proven technology and are
appropriate
in light industrial settings.
V. CHOOSING THE
TECHNOLOGY RIGHT FOR YOU
Before embarking on a briquetting program, investigate the
potential
market to determine the viability of the project.
Social,
environmental, political, and economic factors should be
researched
along with technical matters.
Many projects have failed
because the non-technical factors in their involved were
neglected.
For example, although in some cases the raw materials
required
for briquetting will be very low in cost, the market for
briquettes
itself will increase the value of the raw materials.
This could have negative effects on the distribution of
income.
In addition, some briquetting materials have competing uses.
Dung, for example, is also used as a fertilizer.
Thus the value
of the fuel for its various uses must be weighed before any
decision is made.
Further, there are usually several ways of
producing energy from the raw material.
A special note with respect to the stove that will be used:
In
general, the final briquetted product has a heating value
comparable
to wood. It may,
however, burn in a different manner than
traditional fuels and thus the stove (or the briquette) may
have
to be modified to be compatible.
This issue should be taken
quite seriously by the briquette manufacturer who plans to
sell
the product on the open market.
When analyzing the feasibility of a briquetting project and
the
market appeal of the product, some preliminary research is
essential before proceeding with technical design.
The most
effective way of achieving success is to assess the
situation
from several viewpoints--forestry administration, farmers'
cooperatives,
women's associations, contractors, technicians, etc.
These groups are a good source of information about the
availability
of combustible waste of all kinds, the social climate,
the attitudes of local people to innovations, and economic
and
other relevant factors.
Environmental questions should also be taken into
consideration,
because using biomass waste as fuel eliminates an important
element in the ecological chain.
Normally, biomass waste is
returned to the soil.
If this balance is broken, the consequences
may decrease productivity of the soil and, in extreme
conditions, even lead to desertification.
The analysis should include information on:
1.
Cultural habits pertinent to food
preparation and
cooking styles
2.
Size of the market: number of people and
amount of fuel
used
3.
Relevant social factors
4.
The history of previous innovations in local
society
5.
The willingness and ability of people to pay
for the
new fuel
product
6.
Types and requirements of stoves in use in
the market
area
7.
Availability and characteristics of biomass
waste in
the region
8.
Environmental considerations
9.
Transportation problems
10.
Availability of credit or subsidy to get the
enterprise
started.
The briquetting of
biomass waste that would otherwise be unavailable
as fuel can be an effective, low-cost method of increasing
the fuel supply. In
addition, by providing an alternative to
wood burning, briquetting can help slow the process of
deforestation.
A wide range of technologies makes briquetting accessible
to nearly everyone.
Finally, briquetting holds a unique place
among the various alternative uses of biomass with its
easily
understandable technology and its simplicity of operation.
SUPPLIERS AND MANUFACTURERS
UNITED STATES
Agnew Environmental Products
Box 1168
Grants Pass, Oregon 97526
Telephone: 503/479-3396
Bio-Solar Corp.
P.O. Box 762
Eugene, Oregon 97401
503/686-0765
Bonnot
800 Lake St.
Kent, Ohio 44240
216/676-5829
California Pellet Mill Co.
1800 Folsom St.
San Francisco, California 94103
415/431-3800
Deere & Co. (formerly John Deere)
John Deere Rd.
Moline, Illinois 61265
309/752-8000
Ferro-Tech
467 Eureka Rd.
Wyandotte, Michigan 48192
Fourply Inc.
P.O. Box 890
Grants Pass, Oregon 97526
503/479-3301
Guaranty Performance Co. Inc.
P.O. Box 748
Independence, Kansas 67301
316/331-0027
Hobbs (C.B.) Co.
Elk Grove, California 95624
916/685-3925
Papakube Corp.
7185 Navajo Rd.
Suite 1
San Diego, California 92119
Sprout Waldron
802 Logan St.
Muncy, Pennsylvania 17756
717/546-8211
FOREIGN
Ferdinand Platbrood
12 Category des Rossignols
6070 Chatlet
Belgium
Fred Hausmann Ltd.
4005 Basel
Switzerland
Hawker Siddeley Canada Inc. (formerly Ltd.)
7 King St., East
Toronto, Canada M5C1A3
416/362-2941
Mr. Sayan Panpinig
53 MOO. 6 A. Ladkrabang
Bangkok, Thailand
========================================
========================================