LOW COST DEVELOPMENT OF
WATER POWER SITES
BY
HANS W. HAMM
VITA
1600 Wilson Boulevard, Suite 500
Arlington, Virginia 22209 USA
Tel: 703/276-1800 . Fax 703/243-1865
Internet: pr-info@vita.org
LOW COST DEVELOPMENT OF
SMALL WATER POWER SITES
HANS W. HAMM
a VITA publication
OTHER MANUALS OF INTEREST FROM VITA
Overshot
Water-Wheel: Design and Construction Manual
Small Michell (Banki) Turbine
Hydraulic Ram
Environmentally Sound Small-Scale Water Projects:
Guidelines for Planning
(CODEL/VITA)
Environmentally Sound Small-Scale Energy Projects:
Guidelines for Planning
(CODEL/VITA)
For free catalogue of these and other VITA publications,
write
to:
VITA Publications Services
Volunteers in Technical Assistance
1600 Wilson Boulevard, Suite 500
Arlington, Virginia
22209 USA
ABOUT VITA
Volunteers in Technical Assistance (VITA) is a
private, nonprofit,international development
organization. It makes available to individuals
and
groups in developing countries a variety of
information and technical resources aimed at
fostering self-sufficiency--needs assessment and
program development support; by-mail and on-site
consulting services; information systems training.
Vita
promotes the use of appropriate small-scale
technologies, especially in the area of
renewable energy. VITA's extensive documentation
center and worlwide roster of volunteer technical
experts enable it to respond to thousands of technical
inquiries each year. It also publishes a
quarterly newsletter and a variety of technical
manuals and bulletins.
VITA
VOLUNTEERS
IN TECHNICAL
ASSISTANCE
ISBN 0-86619-014-7
TABLE OF CONTENTS
Preface
I.
Introduction
II. Basic
Data
III. Power
IV.
Measuring Gross Head
V.
Measuring Flow Rate
VI.
Measuring Head Losses
VII. Small
Dams
VIII. Water
Turbines
IX. Water
Wheels
X. Example
Tables
I Flow
Value
II Maximum
Velocity & Friction Coefficient
Appendixes
1. Availability
of Manufactured Turbines
2.
Conversion Tables
3.
Bibliography
4. The
Author and Reviewers
5. Data
Sheet
6. Decision
Making Work Sheet
7. Record
Keeping Work Sheet
PREFACE
During the last
several years of answering individual requests from
Peace Corps and other community development workers, VITA
has come to
realize the great need for a manual on small hydroelectric
power development.
VITA is an
international association of more than 5,000 scientists,
engineers, businessmen and educators who volunteer their
talent and
spare time to help people in developing areas with their
technical
problems. The
Volunteers are from the United States and 100 other
countries.
The difficulty of
communication has proved extreme in answering requests
concerning the feasibility of a small hydro plant as a
source of
power, as compared with a diesel.
The value of a manual written in simple
terms is readily apparent.
The present
manual has been prepared to fill this need.
It should
enable the reader to assess the possibility and desirability
of installing
a small hydroelectric power plant, select the type of
machinery most
suitable for installation, and order turbine and generating
equipment.
It should also serve as a guide in actual construction and
installation.
When further guidance is needed.
VITA can put the reader in touch with
expert VITA Volunteers.
The manual begins
by describing in simple language the steps necessary
to measure the head (the height of a body of water,
considered as causing
pressure) and flow of the water supply, and gives data for
computing the
amount of power available.
Next it describes the construction of a small
dam and points out safety precautions necessary in designing
and building
such structures.
Following this is a discussion of turbines and water
wheels. Guide lines
are given for making the right choice for a particular
site. In this
connection, ready-made units are available from
such reliable manufacturers as James Leffel & Company in
the United States
and Ossberger-Turbinenfabrik in Germany.
Both companies give excellent
service in advising prospective purchasers.
This section of
the manual also describes in detail how to make a
Michell (or Banki) turbine in a small machine shop with
welding facilities,
from usually available pipe and other stock material.
However,
the hazards accompanying the manufacture of so delicate a
machine by
do-it-yourself methods, and the difficulty of achieving high
efficiency
Should warn the ambitious amateur to consider the obvious
alternative
of securing advice from a reliable manufacturer before
attempting to
build his own. Table
3 gives information on the availability of manufactured
units. Electric
generator equipment is standardized and
readily available.
Appendix 1 gives
detailed information on manufacturers of turbines.
Appendix 2 is a chart for converting English units of
measure to metric
units. English units
are used in the text.
Finally, for
those who are interested in pursuing the subject further
and who have the engineering background to understand
technical treatises,
a bibliography in Appendix 2 describes textbooks and
handbooks available
in English in the United States and England.
Harry Wiersema
I. INTRODUCTION
A. Alternatives
Flowing water
tends to generate automatically a picture of "free"
power in the eyes
of the observer. But there is always a
cost to
producing power
from water sources. The cost of
developing low-output
water power sites
should be checked against available alternatives,
such as:
1. Electric
Utility - wherever transmission lines can furnish unlimited
amounts of
reasonably priced electric current, it is
usually
uneconomical to develop small and medium-sized sites.
2. Generators -
diesel engines and internal-combusion engines may
use a variety of
fuels, for example, oil, gasoline, or wood.
In
general, the
capital expenditure for this type of power plant is
low compared to
a hydro-electric plant. Operating
costs, on the
other hand, are
very low for hydro-electricity and high for
generated
power.
3. Solar Heat -
extensive experimental work has been done on the
utilization of
solar heat. Equipment now available may
be less
costly than
water power development in regions with long hours
of intense
sunshine.
B. Evaluation
For isolated
communities in countries where the cost of coal and oil
is high and access
to transmission lines is limited or non-existent,
development of
even the smallest water power site may be worthwhile.
Particularly favorable
is the situation where the head (the height of
a body of water,
considered as causing pressure) is relatively high,
and for this
reason a fairly inexpensive turbine can be used (note
Figure 1).
Water power is also very economical where a
dam can be
lcd1x2.gif (486x486)
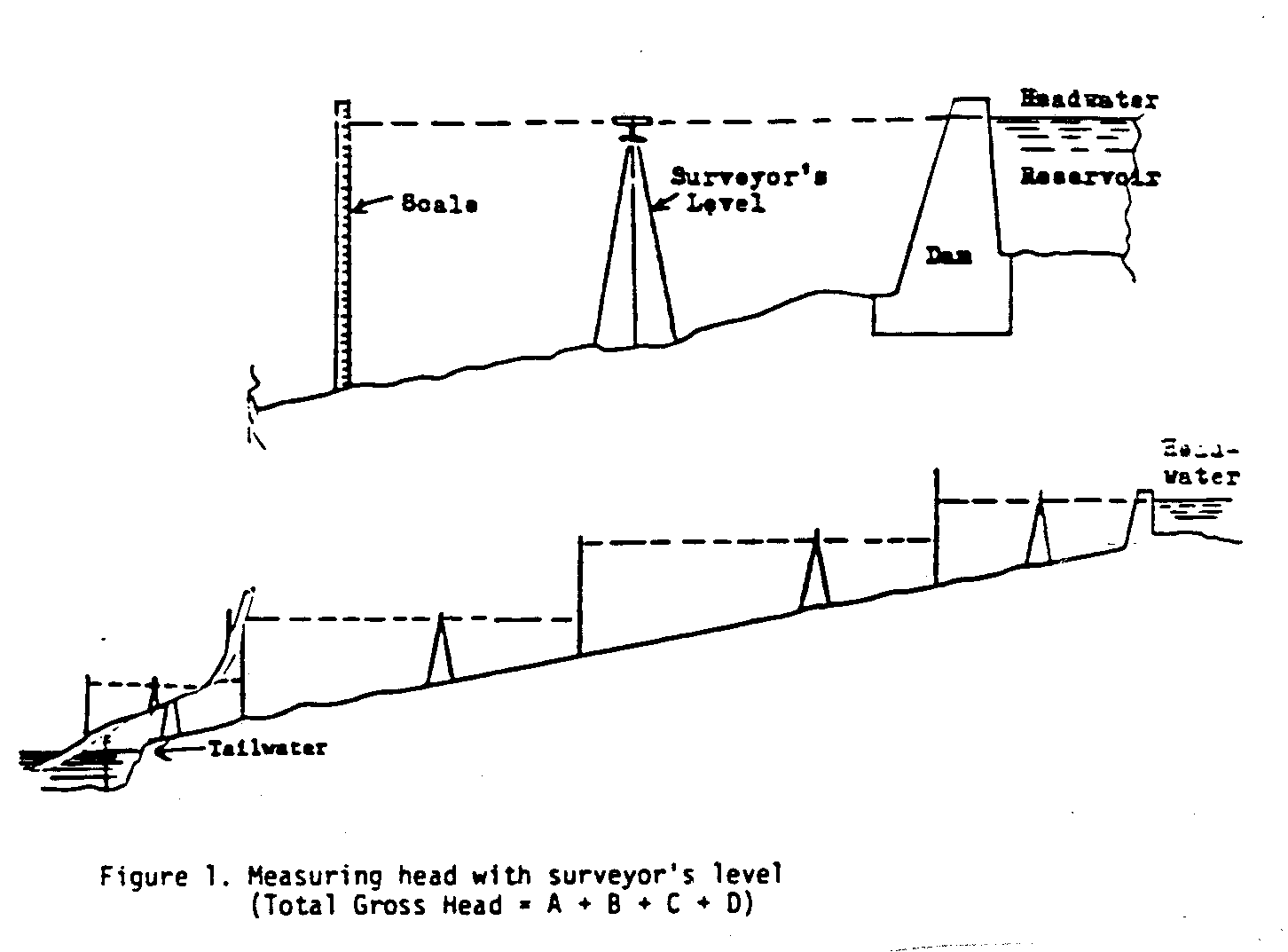
built into a small
river with a relatively short (less than 100 feet)(1)
conduit (penstock)
for conducting water to the water wheel (note
Figure 10).
Development cost can be fairly high when
such a dam and
lcd10x11.gif (600x600)

pipeline can
provide a head of only 20 feet or less.
Cost factors which
must be considered
are:
1. Capital
Expenditures
a. Design cost
- can be relatively high for small plants.
b. Cost of Head
Plants.
High for
low-head plants where a dam and reservoir have to
be created.
Small for
high-head plants with only an intake, a pipeline
and shed for
machinery.
(1) A table for converting English units to metric units is
given in
Appendix 2.
c. Riparian
Rights - the rights of those whose property borders
on a body of
water must be respected.
d. Construction
Cost - including civil works and machinery.
e. Electrical
Equipment - transformers, transmission lines, and
meters.
2. Operating Expenditures
a. Amortization
charges and interest on capital expenditures.
b. Depreciation
- for machinery, about 4% a year.
- for buildings, it can be as low as
1% a year.
c. Labor -
operation and maintenance.
d. Repairs.
e. Taxes,
insurance, and administration.
The safest
method of evaluating and developing a small site is to
be guided by
the following instructions for determining available
head, flow,
and, therefore, power.
A Note of
Caution: flow should be measured at a time when it is at
a minimum,
i.e., during the dry season. Otherwise
the plant will be
oversized.
The data
obtained can be submitted through VITA to several manufacturers
of small turbines for preliminary quotations and
recommendations. Turbine
manufacturers will furnish considerable advice and usually
an outline drawing
of the entire project.
Government publications for designing civil
works such as a dam are available from:
U.S. Government Printing Office
Her Majesty's Stationery
Office
Washington,
D.C. 20402 and
London, England
U.S.A.
These agencies will supply a list of publications on the
subject.
II. BASIC DATA
A. Minimum flow in cubic feet or cubic meters per second.
B. Maximum flow to be utilized.
C. Available head in feet or meters.
D. Pipe line length required for obtaining desired head.
E. Site sketch with elevations, or topographical map with
site sketched in.
F. Water condition, whether clear, muddy, sandy, acid, etc.
F. Soil condition, the velocity of the water and the size of
the ditch or
channel for
carrying it to the works depends on soil condition.
H. Minimum tailwater elevation at the powerhouse site must
be given to
determine the
turbine setting and type.
I. Air temperature, minimum and maximum.
III. POWER
The amount of
power desired (useful power) should be determined in
advance. Power way
be expressed in terms of horsepower or kilowatts.
One
horsepower is equal to 0.7455 kilowatts.
One kilowatt is about one and a
third horsepower.
The required amount of power (gross power) is equal to
the useful power plus the losses inherent in any power
scheme. It is
usually safe to assume that the net or useful power in the
case of small
power installations will only be half of the available gross
power due to
water transmission losses and the turbine and generator
efficiencies. Some
power is lost when it is transmitted from the generator
switchboard to
the place of application.
The GROSS POWER, the power available from the water, is
determined by the
following formula:
In English
Units:
Gross Power
(horsepower)
Minimum
Water Flow (cubic feet/second) X Gross Head(feet)
---------------------------------------------------------
8.8
In Metric Units:
Gross Power
(Metric horsepower) = 1,000 Flow (cubic meters/second)
-----
X Head(meters)
75
The NET POWER available at the turbine shaft is:
In English
Units:
Net Power =
Minimum Water Flow X Net Head X Turbine Efficiency (English)
-----------------------------
8.8
In Metric Units:
Net Power =
Minimum Water Flow X Net Head X Turbine Efficiency (Metric)
-----------------------------
75/1,000
The NET HEAD is
obtained by deducting the energy losses from the gross
head. These losses
are discussed in section VI. A good
assumption for
turbine efficiency, when it is not known, is 80%.
IV. MEASURING GROSS HEAD
(Either Method)
A. Method No. 1
1. Equipment
a. Surveyor's
leveling instrument - consists of a spirit level
fastened
parallel to a telescopic sight (note Figure 2).
lcd2x5.gif (285x285)
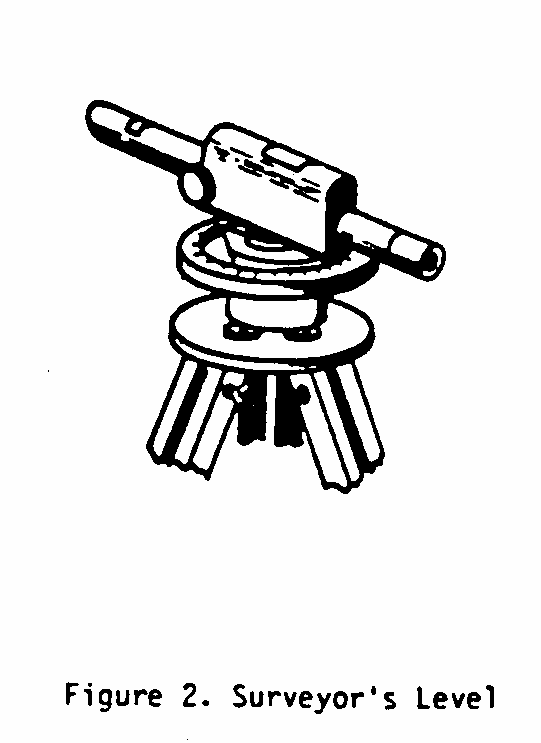
b. Scale - use
wooden board approximately 12 feet in length
(note Figure
3).
lcd3x5.gif (285x285)
2. Procedure (note
Figure 1)
lcd1x2.gif (600x600)
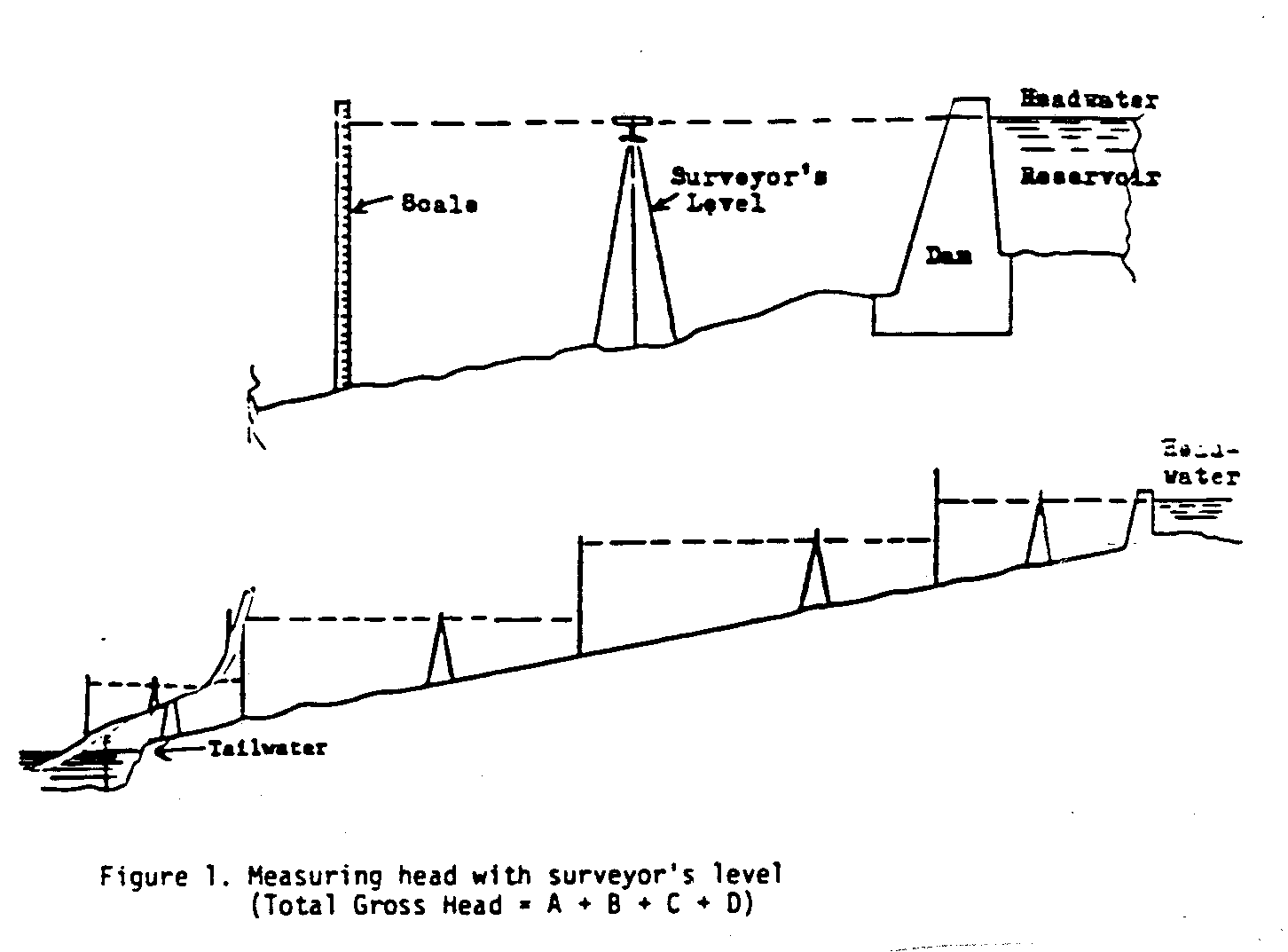
a. Surveyor's
level on a tripod is placed down stream from the
power
reservoir dam on which the headwater level is marked.
b. After taking
a reading, the level is turned 180[degrees] in a
horizontal
circle. The scale is placed downstream
from it
at a
suitable distance and a second reading is taken.
This
process is
repeated until the tailwater level is reached.
B. Method No. 2
This method is
fully reliable, but is more tedious than Method No. 1
and need only be
used when a surveyor's level is not available.
1. Equipment
a. Scale (note
Figure 3).
b. Board and
wooden plug (note Figures 4 and 6).
lcd4x50.gif (285x285)

c. Ordinary
carpenter's level (note Figure 5).
lcd5x6.gif (317x317)
2. Procedure (note
Figure 6)
lcd6x7.gif (600x600)
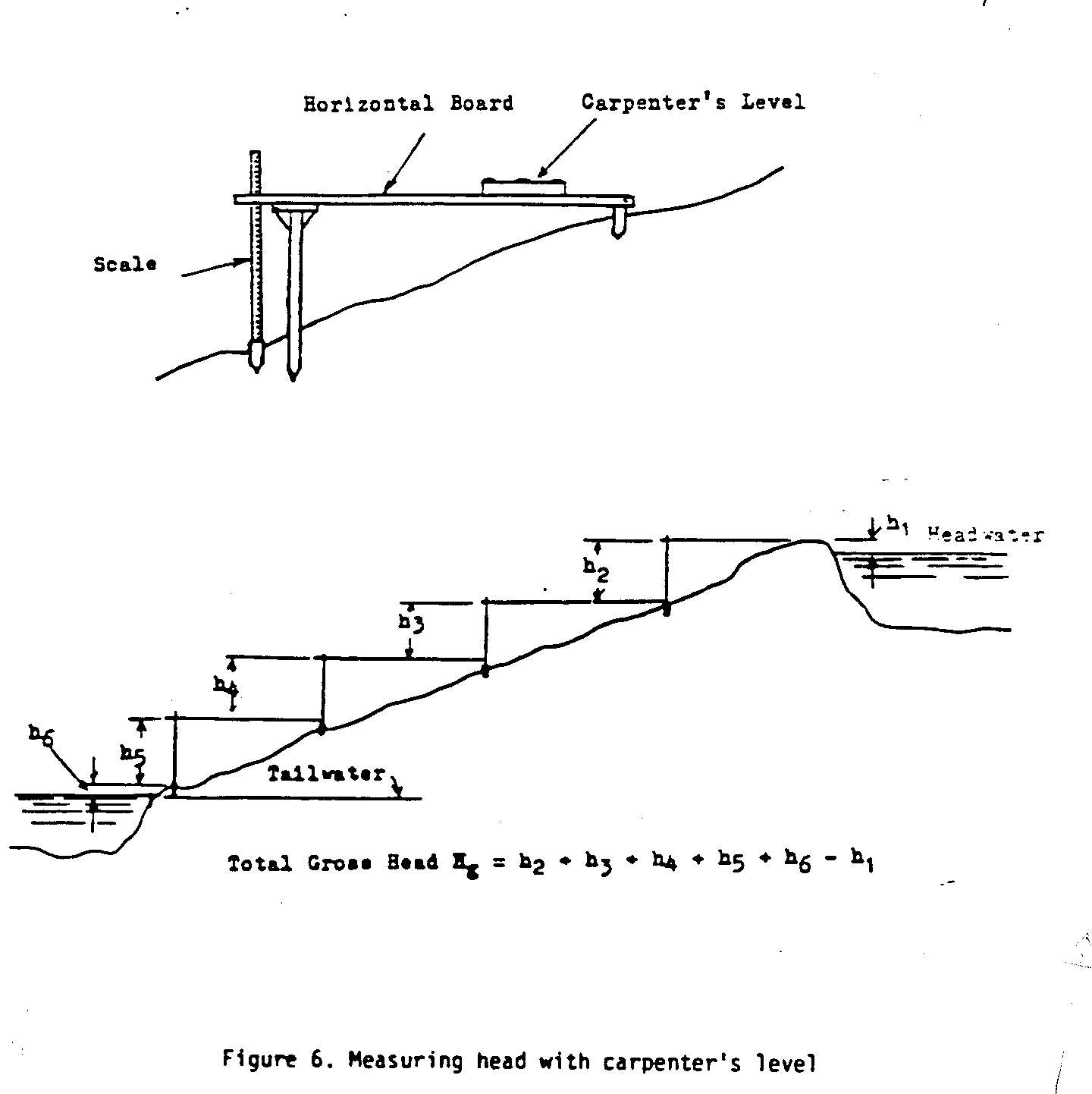
a. Place board
horizontally at headwater level and place level
on top of it
for accurate leveling. At the downstream
end
of the
horizontal board, the distance to a wooden plug set
into the
ground is measured with a scale.
b. The process
is repeated step wise until the tailwater level
is reached.
V. MEASURING FLOW RATE
For power
purposes, measurements should take place at the season of
lowest flow in order to guarantee full power at all
times. Investigate
the stream flow history to ascertain that the minimum
required flow is
that which has occurred for as many years as it is possible
to determine.
An obvious point that has, nevertheless, been overlooked in
the past is
this: if there have been years of drought in which flow rate
was reduced
below the minimum required, other streams or sources of
power may offer a
better solution.
A. Method No. 1
For small
streams with a capacity of less than one cubic foot per
second, build
a temporary dam in the stream, or use a "swimming
hole"
created by a natural dam. Channel the
water into a pipe and
catch it in a
bucket of known capacity. Determine the
stream flow
by measuring
the time it takes to fill the bucket.
Stream Flow
(cubic feet per second) = Volume of Bucket (cubic feet)/Filling Time (seconds)
B. Method No. 2
For medium
streams with a capacity of more than one cubic foot per
second, the
weir method can be used. The weir (see
Figures 7 & 8)
lcd7x8.gif (600x600)
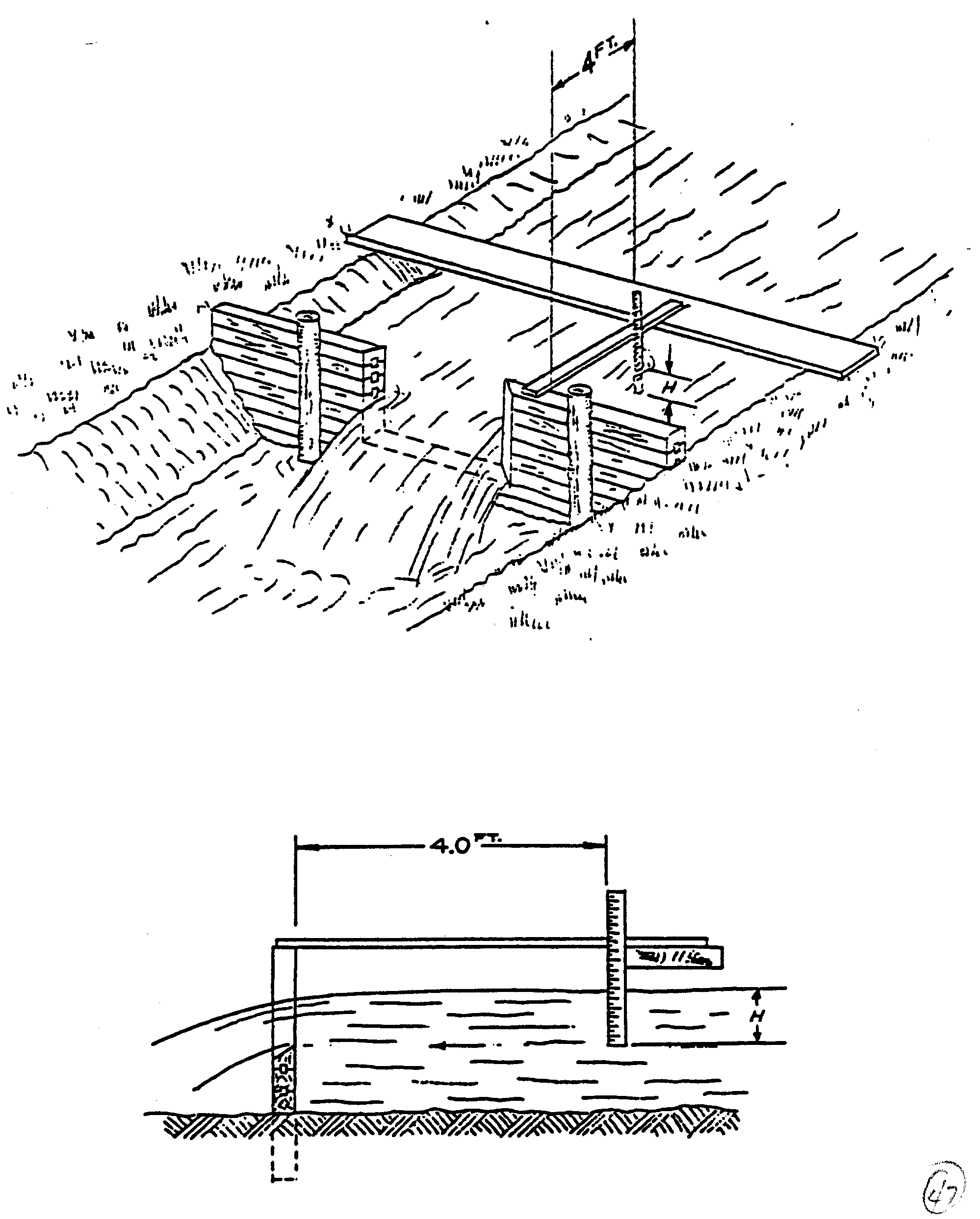
is made from
boards, logs or scrap lumber. Cut a
rectangular
opening in
the center. Seal the seams of the
boards and the sides
built into
the banks with clay or sod to prevent leakage.
Saw the
edges of the
opening on a slant to produce sharp edges on the upstream
side.
A small pond is formed upstream from the
weir. When
there is no
leakage and all water is flowing through the weir opening,
(1) place a
board across the stream and (2) place another narrow board
level (use a
carpenter's level) and perpendicular to the first.
Measure
the depth of
the water above the bottom edge of the weir with the help
of a stick on
which a scale has been marked.
Determine the flow from
Table I.
Table I
FLOW VALUE (Cubic Feet per Second)
Weir Width
------------------------------------------------------------
Overflow Height 3
feet 4 feet
5 feet 6 feet
7 feet
8 feet 9 feet
------------------------------------------------------------
1.0 inch
.24
.32 .40
.48
.56 .64
.72
2
inches
.67 .89
1.06
1.34 1.56
1.8
2.0
4
inches 1.9
2.5
3.2 3.8
4.5
5.0 5.7
6
inches
3.5 4.7
5.9
7.0 8.2
9.4
10.5
8
inches
5.4 7.3
9.0
10.8 12.4
14.6
16.2
10
inches
7.6 10.0
12.7
15.2 17.7
20.0
22.8
12
inches
10.0 13.3
16.7
20.0 23.3
26.6
30.0
C. Method No. 3
The float
method (Figure 9) is used for larger streams.
Although it
lcd9x10.gif (600x600)

is not as
accurate as the previous two methods, it is adequate for
practical
purposes. Choose a point in the stream
where the bed is
smooth and
the cross section is fairly uniform for a length of at
least 30
feet. Measure water velocity by
throwing pieces of wood into
the water and
measuring the time of travel between two fixed points,
30 feet or
more apart. Erect posts on each bank at
these points.
Connect the 2
upstream posts by a level wire rope (use a carpenter's
level).
Follow the same procedure with the down
stream posts. Divide
the stream
into equal sections along the wires and measure the water
depth for
each section. In this way, the
cross-sectional area of
the stream is
determined. Use the following formula
to calculate the
flow:
Stream Flow
(cubic feet per second) = Average Cross-Sectional Flow
Area(square feet) X Velocity (feet per second)
VI. MEASURING HEAD LOSSES
As noted in
Section III, the "Net Power" is a function of the "Net
Head". The
"Net Head" is the "Gross Head" less the "Head
Losses".
Figure 10 shows a typical small water power
installation. The head losses
lcd10x11.gif (600x600)

are the open-channel losses plus the friction loss from flow
through the
penstock.
A. Open Channel
Head Losses
The headrace
and the tailrace in Figure 11 are open channels for
lcd11x12.gif (600x600)
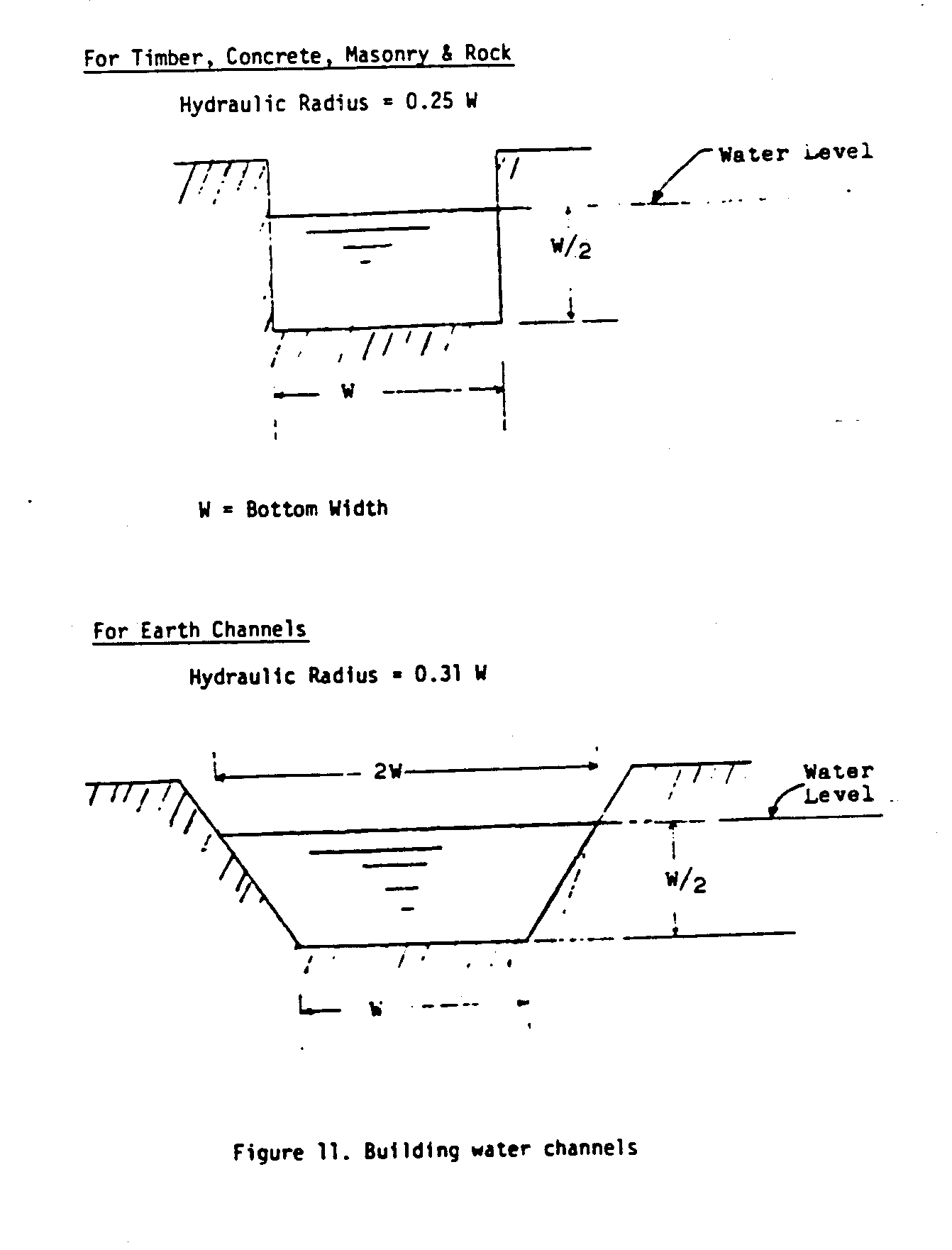
transporting
water at low velocities. The walls of
channels made of
timber,
masonry, concrete, or rock, should be constructed
perpendicularly. Design them so that the water level height is one half
of
the width.
Earth walls should be built at a 45[degrees]
angle. Design them so
that the water
level height is one half of the channel width at the
bottom.
At the water level the width is twice that
of the bottom.
The head loss in
open channels is given in the nomograph in Figure 12.
lcd12x13.gif (600x600)
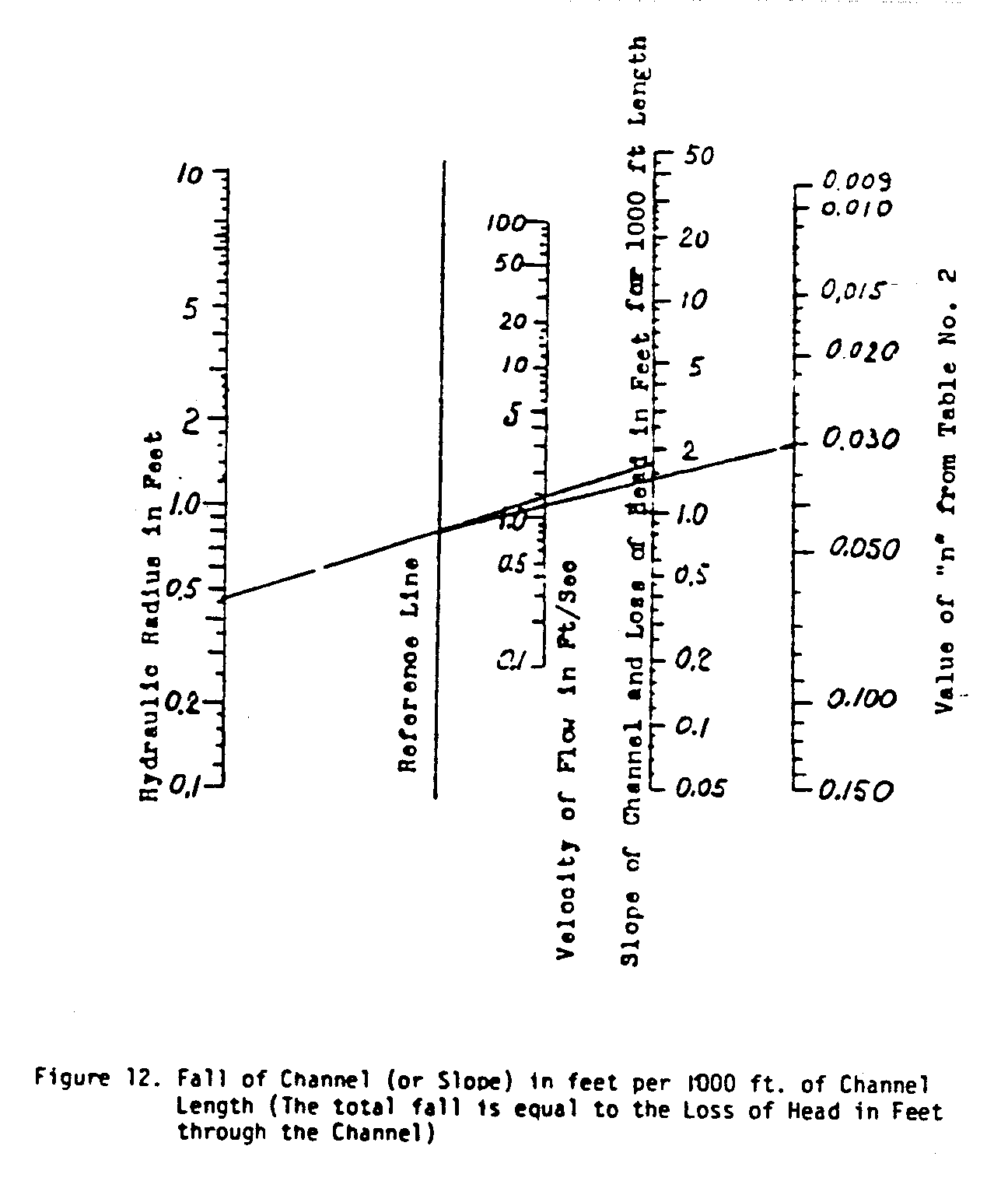
The friction effect of the material of construction is
called "n". Various
values of "n" and the maximum water velocity,
below which the walls of a
channel will not erode are given in Table II.
Table II
Maximum Allowable
Water Velocity
Material of Channel Wall
(feet/second)
Value of "n"
Fine grained sand
0.6
0.030
Coarse sand
1.2
0.030
Small stones
2.4
0.030
Coarse stones
4.0
0.030
Rock
25.0
(Smooth) 0.033
(Jagged) 0.045
Concrete with sandy water
10.0
0.016
Concrete with clean water
20.0
0.016
Sandy loam, 40% clay
1.8
0.030
Loamy soil, 65% clay
3.0
0.030
Clay loam, 85% clay
4.8
0.030
Soil loam, 95% clay
6.2
0.030
100% clay
7.3
0.030
Wood
0.015
Earth bottom with rubble sides
0.033
The hydraulic
radius is equal to a quarter of the channel width, except
for earth-walled channels where it is 0.31 times the width
at the bottom.
To use the
nomograph, a straight line is drawn from the value of "n"
through the flow velocity to the reference line.
The point on the reference
line is connected to the hydraulic radius and this line is
extended
to the head-loss scale which also determines the required
slope of the
channel.
B.
Pipe Head loss and Penstock Intake
The trashrack
in Figure 13 is a weldment consisting of a number of
lcd13x15.gif (600x600)
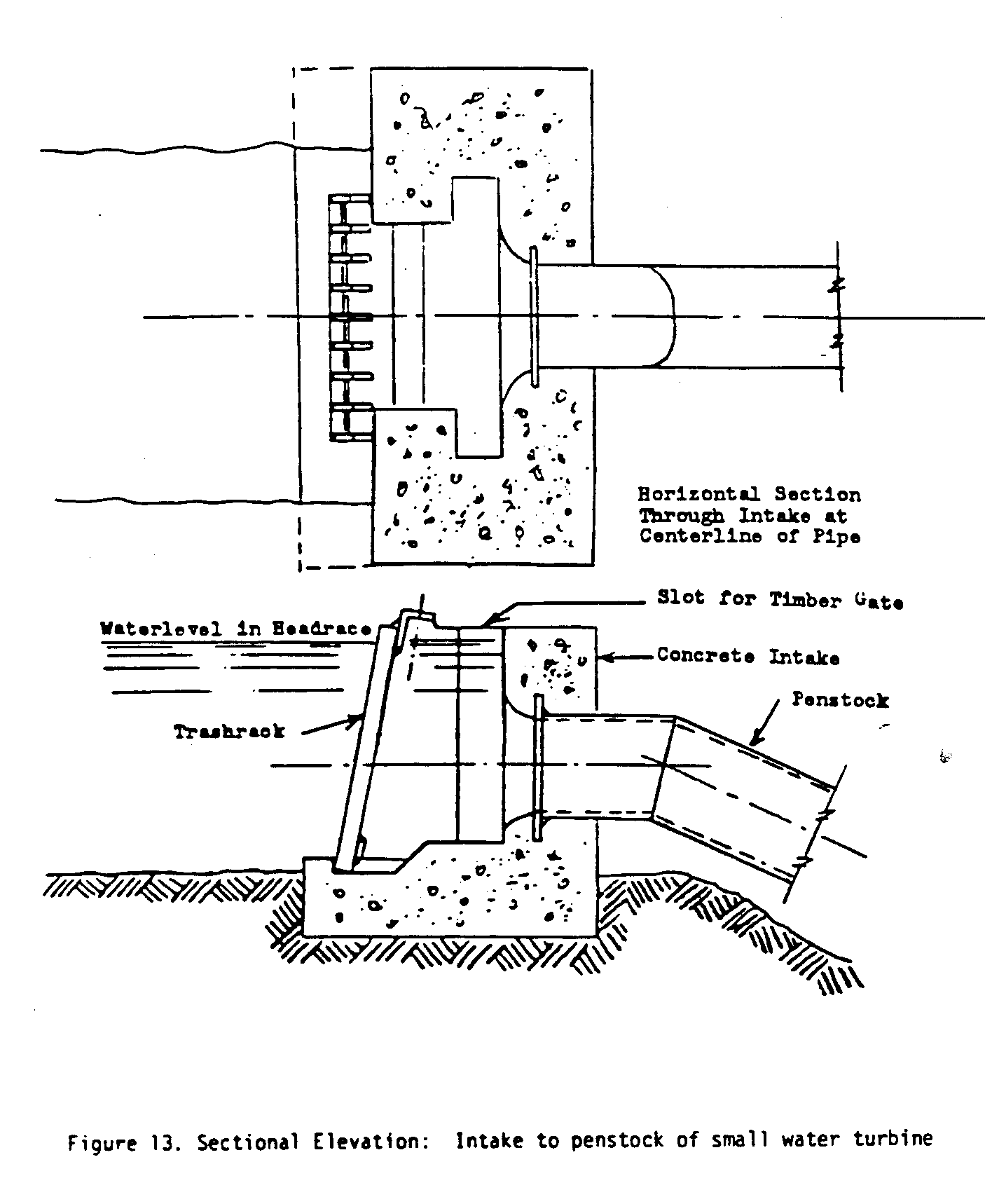
vertical bars
held together by an angle at the top and a bar at the
bottom.
The vertical bars must be spaced in such a
way that the
teeth of a
rake can penetrate the rack for removing leaves, grass
and trash
which might clog up the intake. Such a
trashrack can
easily be
manufactured in the field or in a small welding shop.
Downstream
from the trashrack, a slot is provided in the concrete
into which a timber gate can be inserted for
shutting off the flow
of water to
the turbine.
The penstock
can be constructed from commercial pipe.
The pipe
must be large
enough to keep the head loss small.
From the nomograph
(Figure 14) the required pipe size is
determined. A straight line
lcd14x16.gif (600x600)
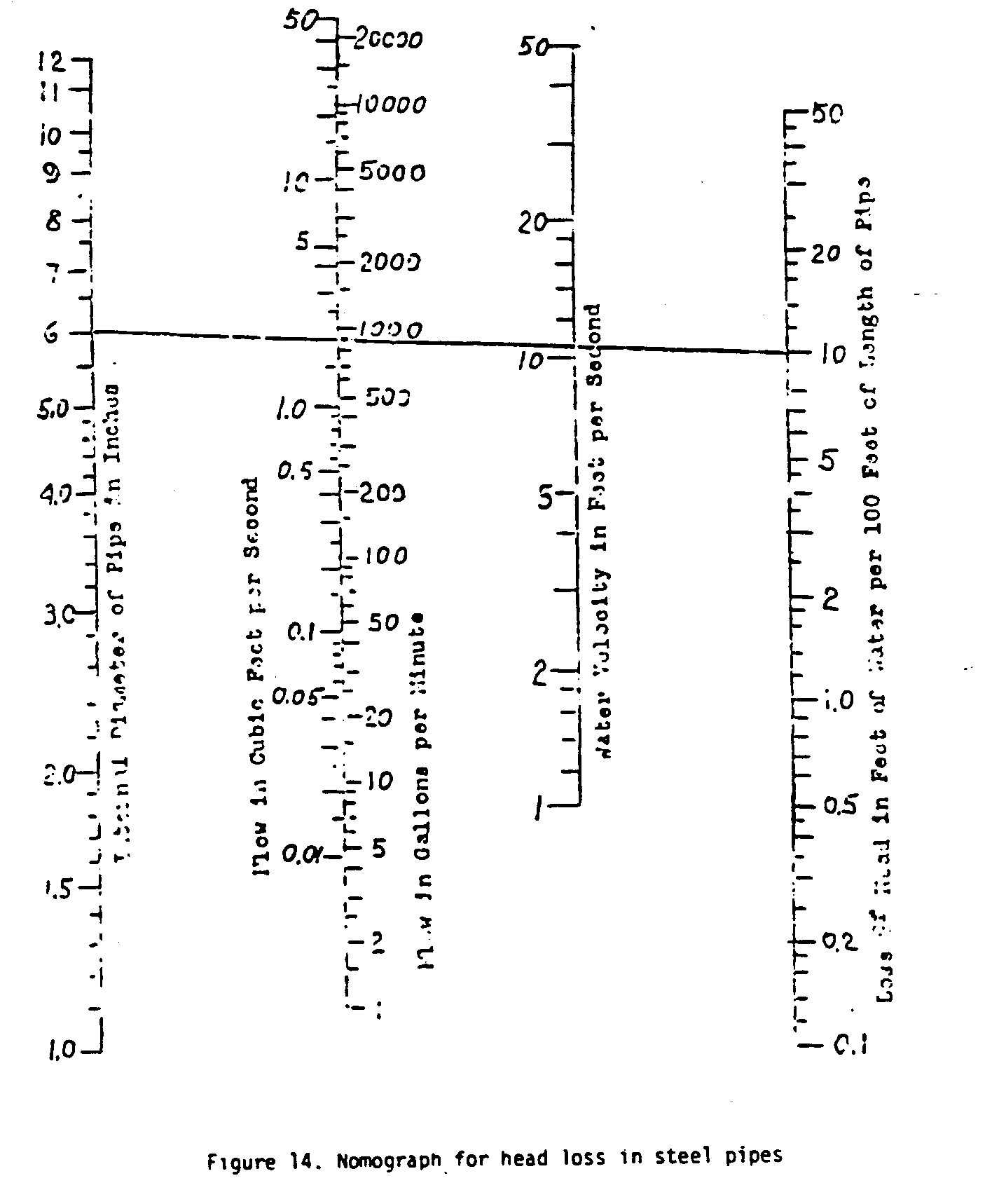
drawn through
the water velocity and flow rate scales gives the
required pipe
size and pipe head-loss. Head loss is
given for a
100-foot pipe
length. For longer or shorter
penstocks, the actual
head loss is
the head loss from the chart multiplied by the actual
length
divided by 100. If commercial pipe is
too expensive, it is
possible to
make pipe from native material; for example, concrete
and ceramic
pipe or hollowed logs. The choice of
pipe material
and the
method of making the pipe depend on the cost and availability
of labor and
the availability of material. VITA can
provide the
needed
technical information.
VII.
SMALL DAMS
A dam is
necessary in most cases to direct the water into the channel
intake or to get a higher head than the stream naturally
affords. A dam
is not required if there is enough water to cover the intake
of a pipe or
channel at the head of the stream where the dam would be
placed.
A dam may be made
of earth, wood, concrete or stone. In
building any
kind of a dam, all mud, vegetable matter and loose material
must be removed
from the bed of the stream where the dam is to be
placed. This usually is
not difficult since most small streams will cut their beds
down close to
bed rock, hard clay or other stable formation.
A. Earth Dams
An earth dam may
be desirable where concrete is expensive and timber
scarce.
It must be provided with a separate spillway
of sufficient
size to carry off
excess water because water can never be allowed to
flow over the
crest of an earth dam. If it does the
dam will-erode and
be destroyed.
A spillway must be lined with boards or with
concrete
to prevent
seepage and erosion. Still water is
held satisfactorily by
earth but moving
water is not. The earth will be worn
away by it.
Figures 15 and 16
show a spillway and an earth dam. The
crest of the
lcd15170.gif (600x600)
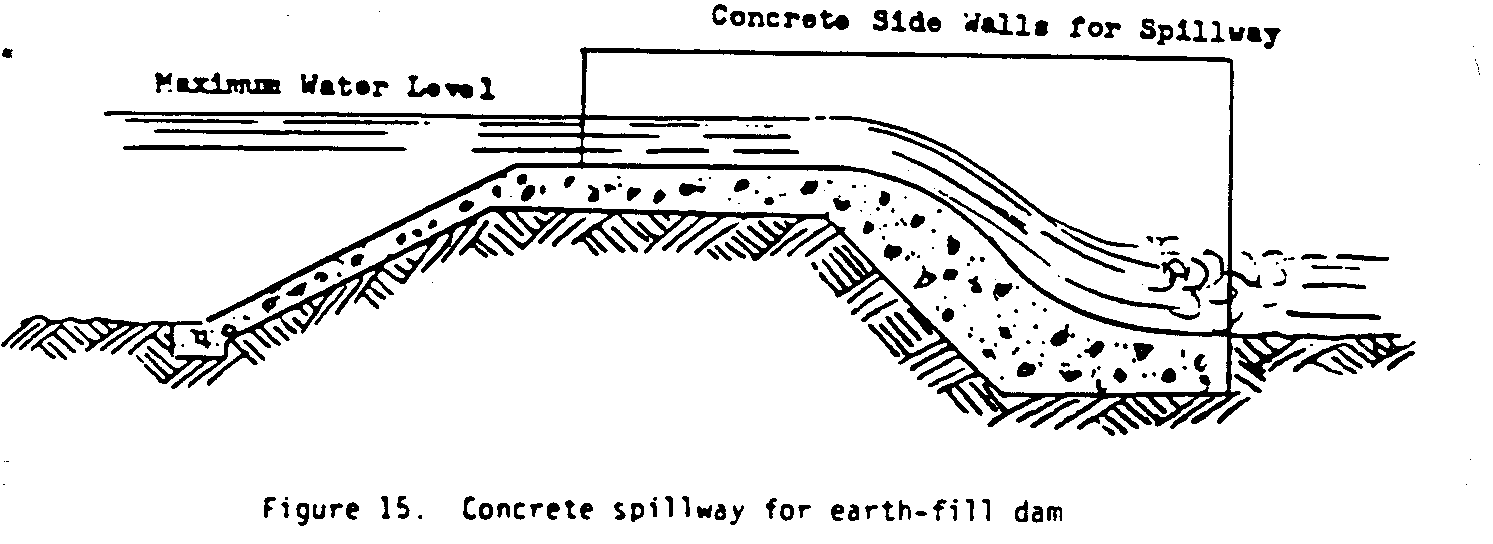
a roadway, with a
bridge placed across the spillway.
NOTE: Building a
dam will cause important environmental changes
both upstream and
downstream. In addition, even a small dam creates
a potential
flooding hazard once it is filled with water. CONSULT
A PROFESSIONAL
CIVIL ENGINEER BEFORE BUILDING A DAM.
The greatest
difficulty in earth-dam construction occurs in places where
the dam rests on
solid rock. It is hard to keep the
water from seeping
between the dam
and the earth and finally undermining the dam.
One way
of preventing
seepage is to blast and clean out a series of ditches in
the rock, with
each ditch about a foot deep and two feet wide extending
under the length
of the dam. Each ditch should be filled
with three
or four inches of
wet clay compacted by stamping it. More
layers of
wet clay can then
be added and the compacting process repeated each
time until the clay is several inches higher
than bedrock. The upstream
half of the dam,
as shown in Figure 16 should be of clay or heavy clay
lcd16x18.gif (600x600)
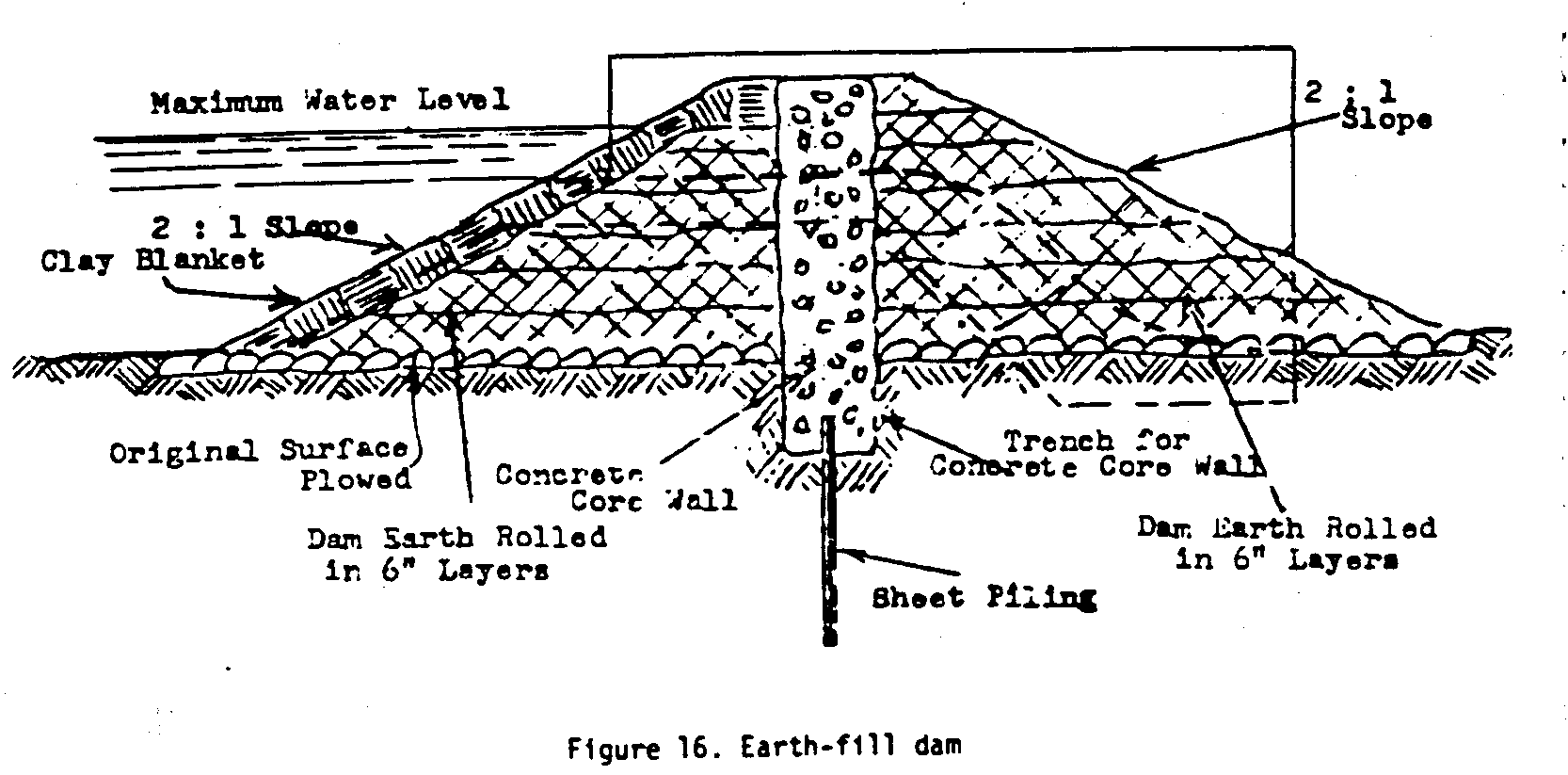
soil, which
compacts well and is impervious to water.
The downstream
side should
consist of lighter and more porous soil, which drains out
quickly and thus
makes the dam more stable than if it were made
entirely of clay.
B. Crib Dams
The crib dam is
very economical in timber country as it requires only
rough tree
trunks, cut planking and stones. Four-
to six-inch tree
trunks are placed
two to three feet apart and spiked to others placed
across them at
right angles. Stones fill the spaces
between timbers.
The upstream side
(face) of the dam, and sometimes the downstream side,
is covered with
planks (see Figure 17). The face is
sealed with clay
lcd17x19.gif (600x600)
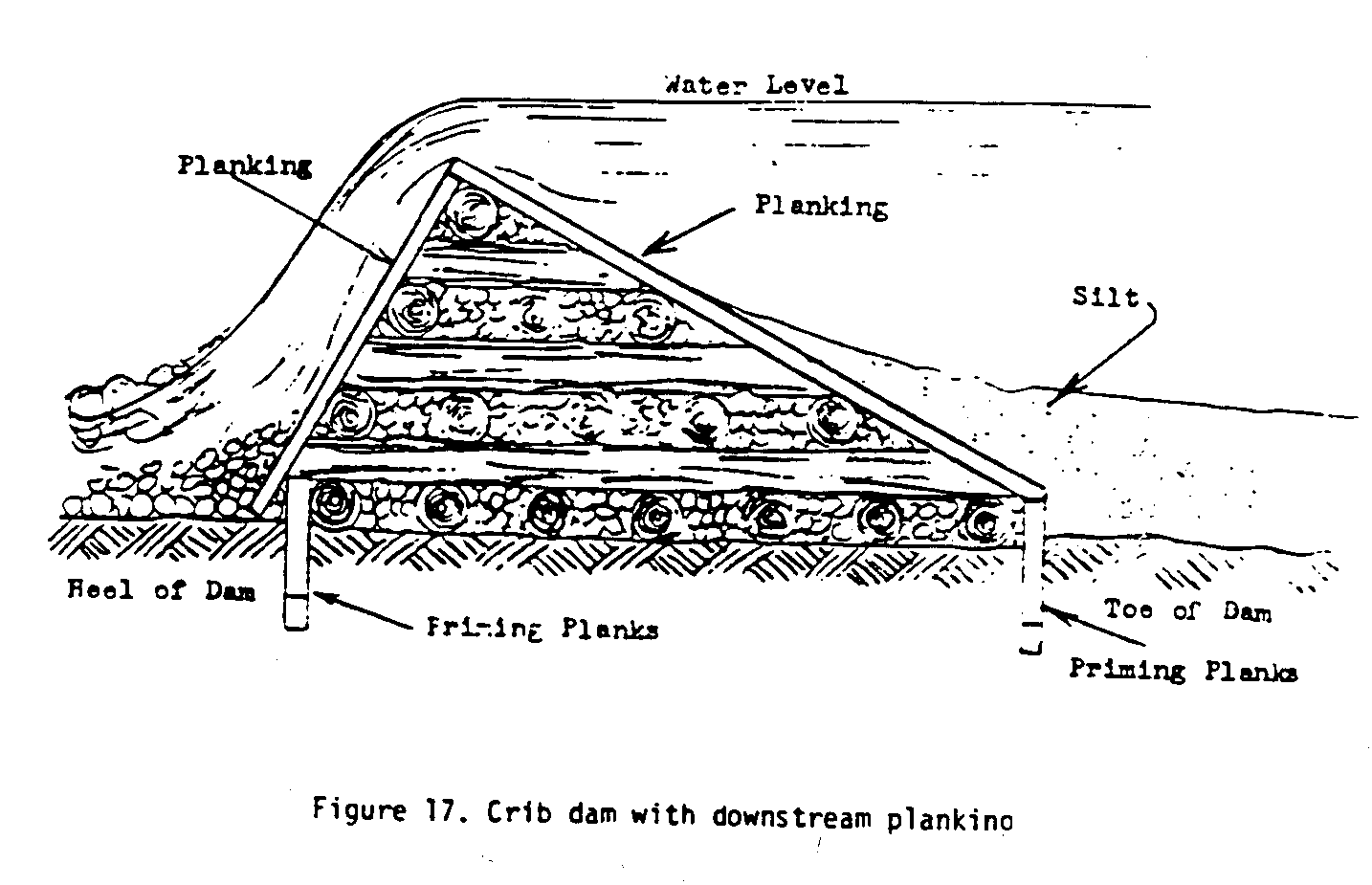
to prevent
leakage. Downstream planks are used as
an apron to guide
the water which
overflows the dam back into the stream bed.
The dam
itself serves as
a spillway in this case. The water
coming over the
apron falls
rapidly and it is necessary to line the bed below with
stones in order
to prevent erosion. A section of a crib
dam without
downstream
planking is illustrated in Figure 18.
The apron consists
lcd18x19.gif (600x600)
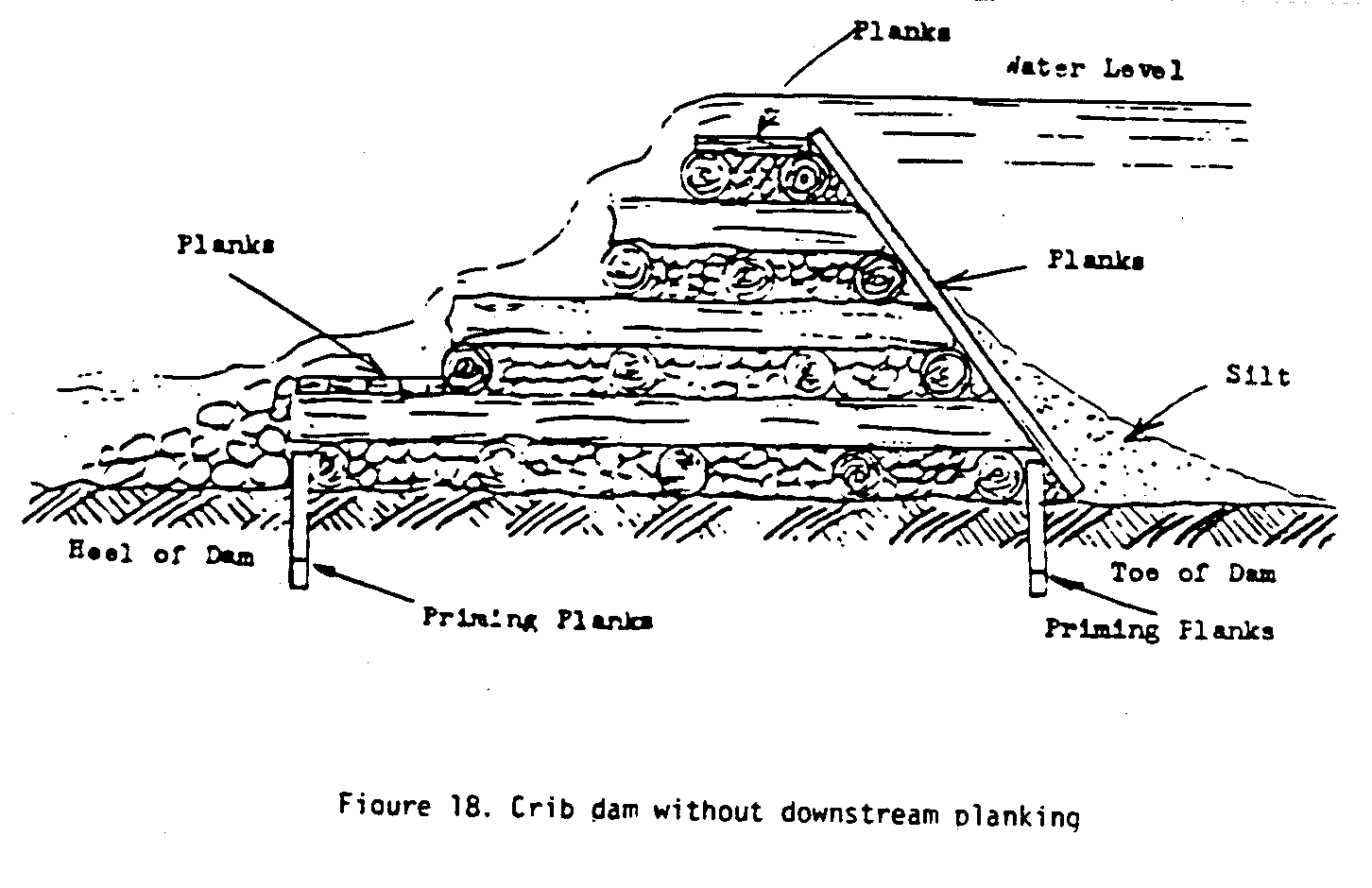
of a series of
steps for slowing the water gradually.
Crib dams, as
well as other types, must be embedded well into the
embankments and
packed with impervious material such as clay or
heavy earth and
stones in order to anchor them and to prevent
leakage.
At the heel as well as at the toe of crib
dams, longitudinal
rows of planks
are driven into the stream bed. These
are priming
planks which
prevent water from seeping under the dam, and the also
anchor it.
If the dam rests on rock, priming planks
cannot and need
not be driven;
but where the dam does not rest on rock they make it
more stable and
watertight. These priming planks should
be driven as
deep as possible
and then spiked to the timber of the crib dam.
The
lower ends of the
priming planks are pointed as shown in Figure 19,
lcd19x20.gif (437x437)
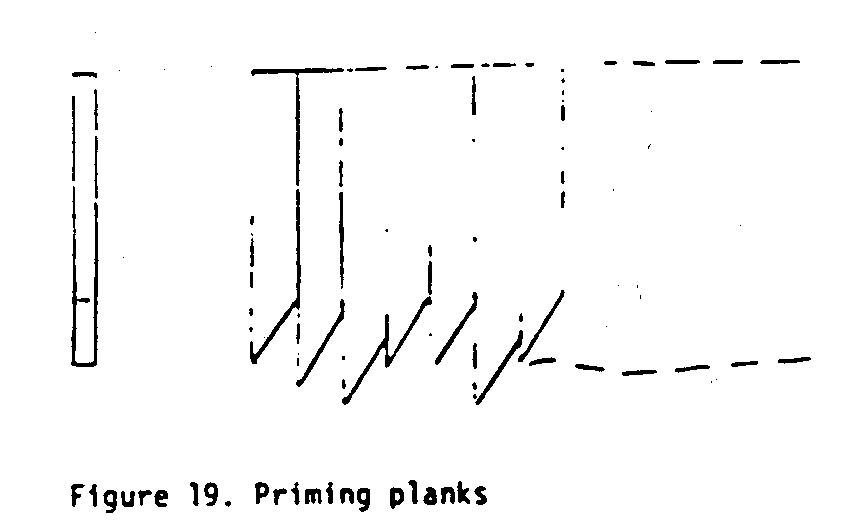
and they must be
placed one after the other as shown.
Thus each
successive plank
is forced, by the act of driving it, closer against
the preceding
plank resulting in a solid wall. Any
rough lumber may
be used. Chestnut
and oak are considered to be the best material. The
lumber must be
free from sap, and its size should be approximately
two inches by six
inches. In order to drive the priming
planks and
also the sheet
piling of Figure 16, considerable force may be required.
lcd16x18.gif (600x600)
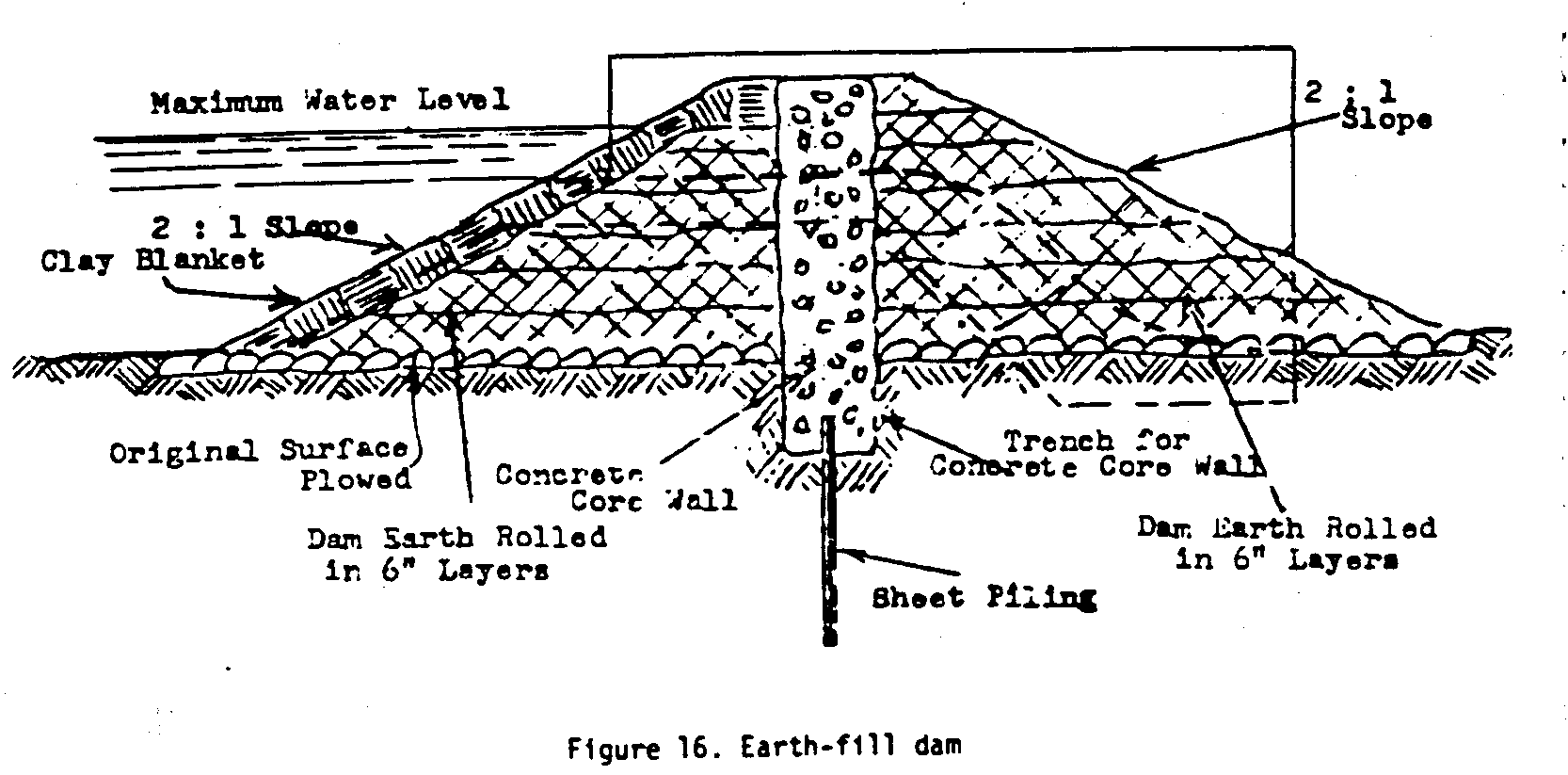
A simple pile
driver as shown in Figure 20 will serve the
lcd20x20.gif (486x486)
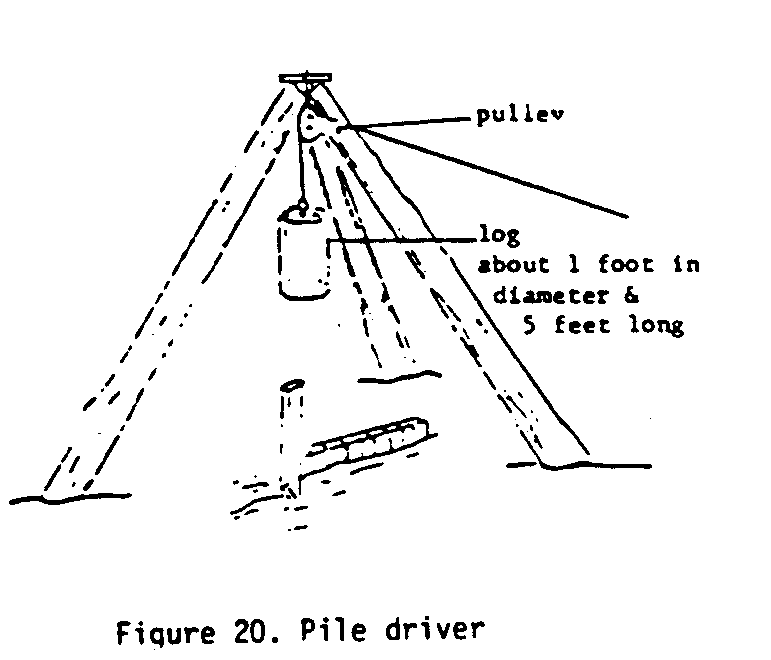
purpose.
C. Concrete and
Masonry Dams
Concrete and
masonry dams more than 12 feet high should not be built
without the
advice of a competent engineer with experience in this
special
field. Dams of less height require
knowledge of the soil
condition and
bearing capacity as well as of the structure itself.
Figure 21 shows a
stone dam which also serves as a spillway.
It can
lcd21x21.gif (600x600)
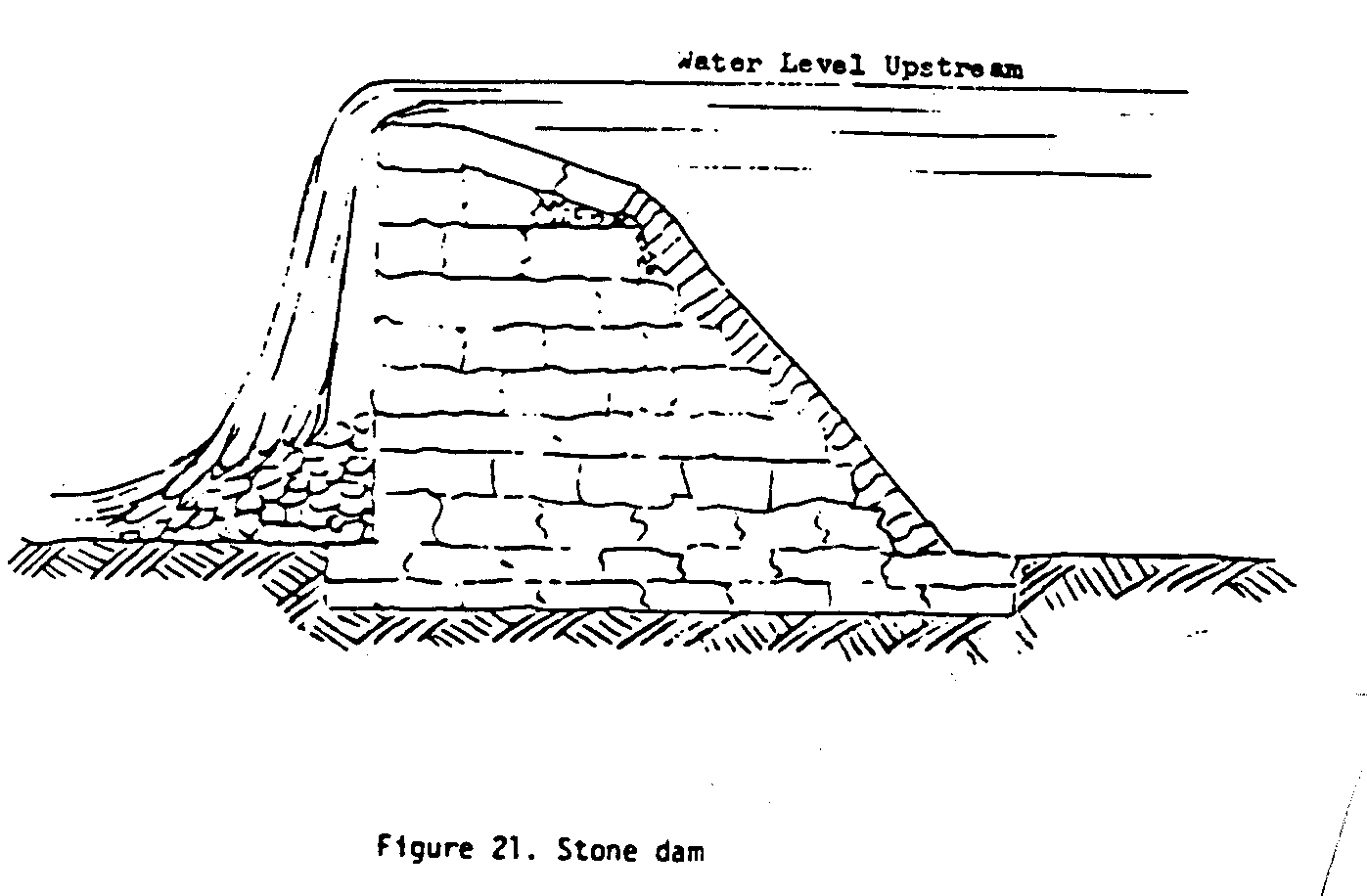
be up to ten feet
in height. It is made of rough
stones. The layers
should be bound
by concrete. The dam must be built down
to a solid
and permanent
footing to prevent leakage and shifting.
The base of
the dam should
have the same dimension as its height to give it
stability.
Small concrete
dams (Figure 22) should have a base with a thickness
lcd22x22.gif (486x486)
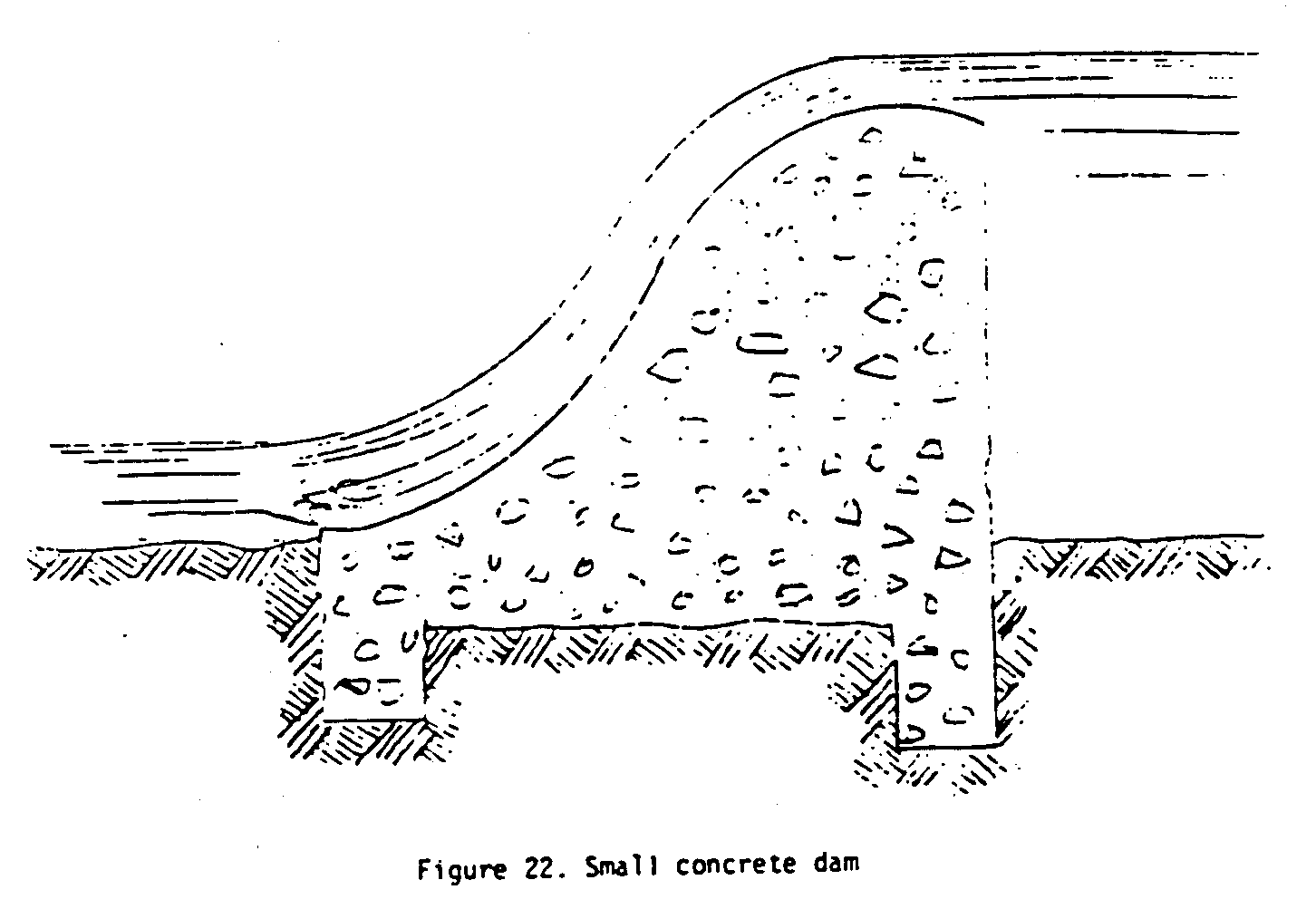
50% greater than
height. The apron is designed to turn
the flow
slightly upwards
to dissipate the energy of the water and protect
the downstream
bed from eroding.
VIII. WATER TURBINES
The manufacturers
of hydraulic turbines for small plants can usually
quote on a complete packaged unit, including the generator,
governor and
switch gear. Water
turbines for small power developments may be purchased
(see Table III) or made in the field, if a small machine and
weld shop is
available.
A centrifugal
pump may be used as a turbine wherever it is technically
possible. Its cost
is about one-third the cost of a hydraulic turbine.
But
it may be poor economics to use a centrifugal pump because
it is less
efficient than a turbine and will have other disadvantages.
A water power
unit can produce either direct current (D.C.) or
alternating current (A.C.) electricity.
Two factors to
consider in deciding whether to install an A.C. or D.C.
power unit are (1) the cost of regulating the flow of water
into the turbine
for A.C. and (2) the cost of converting motors to use D.C.
electricity.
Flow Regulation
The demand for
power will vary from time to time during the day.
With
a constant flow of water into the turbine, the power output
will sometimes
be greater than the demand for power.
Therefore, either excess power must
be stored or the flow of water into the turbine must be
regulated according
to the demand for power.
In producing
A.C., the flow of water must be regulated because A.C.
cannot be stored.
Flow regulation requires governors and complex valve-type
shut-off devices.
This equipment is expensive; in a small water
power site, the regulating equipment would cost more than a
turbine and
generator combined.
Furthermore, the equipment for any turbine used for
A.C. must be built by experienced water-turbine
manufacturers and serviced
by competent consulting engineers.
The flow of water
to a D.C. producing turbine, however, does not
have to be regulated.
Excess power can be stored in a storage battery.
Direct-current generators and storage batteries are low in
cost because
they are mass-produced.
To
summarize: In producing A.C., the flow
of water into the turbine
must be regulated; this requires costly and complex
equipment. In producing
D.C., regulation is not necessary, but storage batteries
must be
used.
Converting Motors for D.C.
D.C. power is
just as good as A.C. for producing electric light and
heat. But for
electrical appliances, from farm machinery to household
appliances, the use of D.C. power can involve some expense.
When such
appliances have A.C. motors, D.C. motors must be
installed. The cost of
doing this must be weighed against the cost of flow
regulation needed for
producing A.C.
Table III
Small Hydraulic Turbines
Types
Impulse
Michell Centrifugal
Pump
or or
Used as
Pelton Banki
Turbine
Head Range
50 to 1000 3 to
650 Available
(feet)
for
Flow Range
0.1 to 10
0.5 to 250
(cubic feet per second)
any
Application
high head medium
head desired
Power
1 to 500
1 to 1000
condition
(horsepower)
Cost per Kilowatt
low low
low
Manufacturers
James Leffel & Co.
Ossberger- Any
reputable
Springfield, Ohio
Turbinenfabrik
dealer or
U.S.A. 45501 8832
Weissenbura manufacturer
Drees & Co. Bayern,
Germany
Werl. Germany Can be
do-it-your-
Officine Buhler self
project if small
Taverne, Switzerland weld and
machine
shops are available
A. Impulse Turbines
Impulse turbines
are used for high heads and low flow rates.
They
are the most
economical turbine because the high head gives them high
speed and their
size and weight per horsepower is small.
Construction
costs of intake
and power house are also small. A very
simplified
version is shown
in Figures 23 and 24.
lcd23240.gif (600x600)
The Michell (or
Banki) turbine is simple in construction and may be
the only type of
water turbine which can be locally built.
Welding
equipment and a small machine Shop like
those often used to repair
farm machinery and
automotive parts are all that is necessary.
The two main parts
of the Michell turbine are the runner and the
nozzle.
Both are welded from plate steel and require
some machining.
Figures 25 and 26 show the arrangement of a turbine of this
type for
lcd25270.gif (600x600)

generator with a belt drive.
Because the construction can be a DO-IT-YOURSELF
project, formulas and design details are given for a runner
of
12" outside diameter.
This size is the smallest which is easy to
fabricate and weld.
It has a wide range of application for all small
power developments with head and flow suitable for the
Michell turbine.
Different heads result in different rotational speeds.
The proper belt-drive
ratio gives the correct generator speed.
Various amounts of water
determine the width of the nozzle ([B.sub.1], Figure 26) and
the width of the
lcd26x28.gif (600x600)
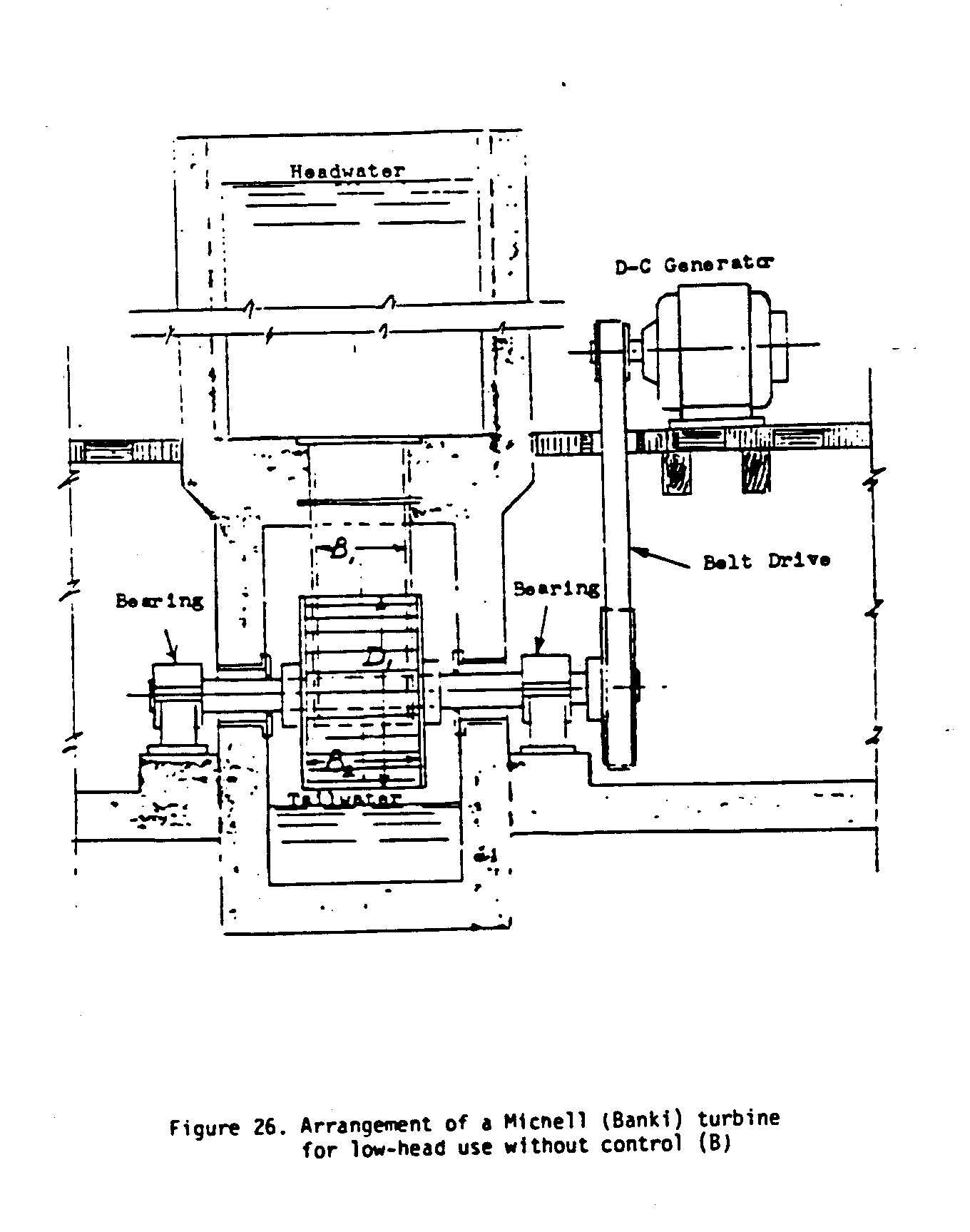
runner ([B.sub.2], Figure 26).
These widths may vary from 2 inches to 14 inches.
No other turbine is adaptable to as large a range of flow.
The water passes through the runner twice in a narrow jet
before discharge
into the tailrace.
The runner consists of two side plates, each 1/4"
thick with hubs for the shaft attached by welding, and from
20 to 24
blades. Each blade
is 0.237" thick and cut from 4" standard pipe.
Steel pipe of this type is available virtually
everywhere. A pipe of
suitable length produces four blades.
Each blade is a circular segment
with a center angle of 72 degrees.
The runner design, with dimensions
for a foot-long runner, is shown in Figure 27; and Figure 28
gives the
lcd27290.gif (600x600)
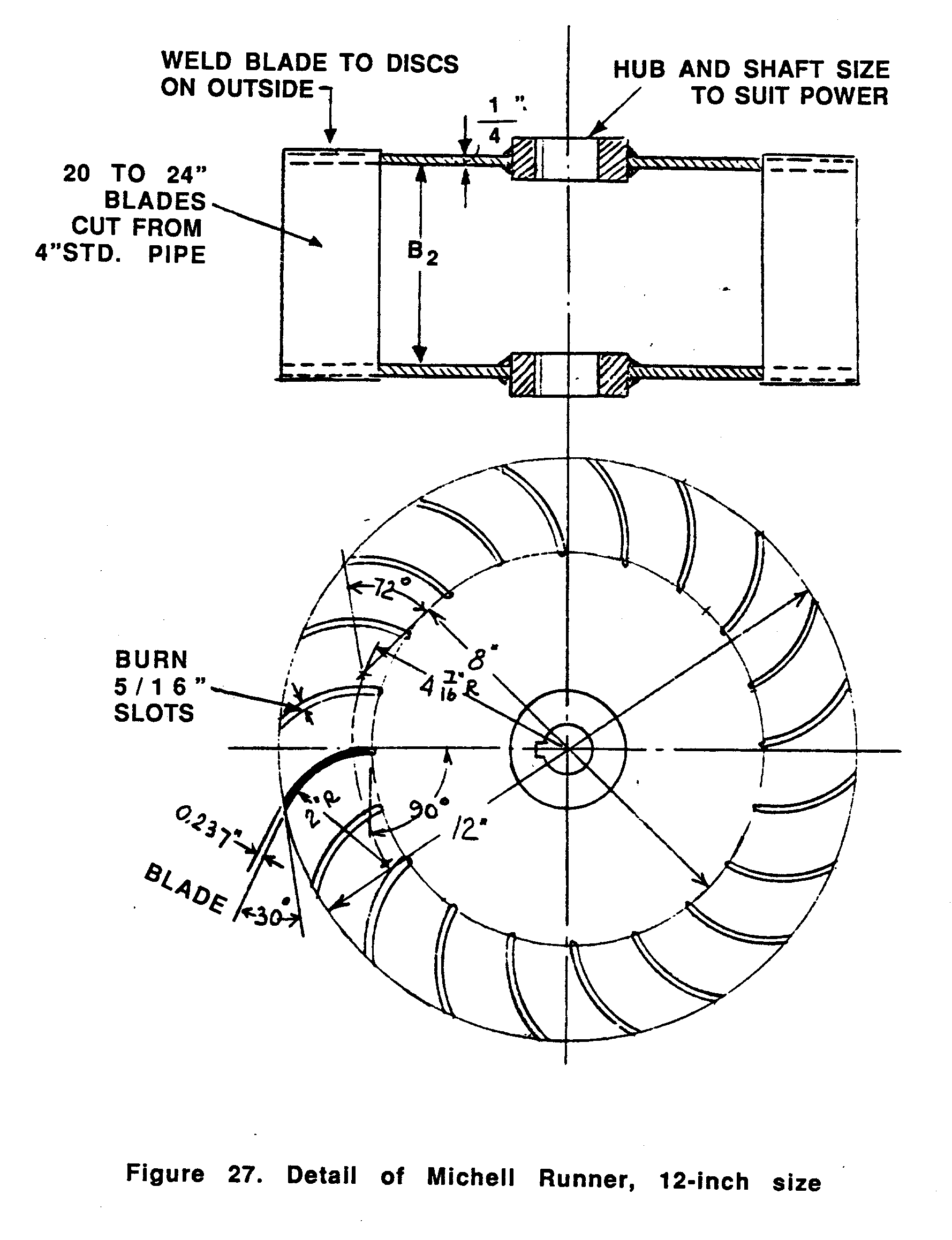
for other size runners.
Upstream from the nozzle discharge
opening of 1 1/4", the shape of the nozzle can be made
to suit penstock
pipe conditions.
To calculate the principal turbine dimension:
[B.sub.1] = Nozzle Width (inches) = 210 X Flow (cubic feet
per second)
-----------------------------------------------------------
Runner Outside Diameter
(inches) X [square root]Head (feet)
[B.sub.2] = Runner Width between Discs = [B.sub.1] + 1/2 to 1"
Rotational Speed (revolutions per minute) = 73.1 X [square
root] Head (feet)
--------------------------------
Runner Outside Diameter
(feet)
The efficiency of the Michell turbine is 80% or greater and
therefore
suitable for small power installations.
Flow regulation and governor,
control of the flow can be effected by using a center-body
nozzle
regulator (a closing mechanism in the shape of a gate in the
nozzle).
This is expensive because of governor costs.
It is, however, needed
for running an alternating-current generator.
The application of Figures 25 and 26 is a typical
example. For high
heads the Michell turbine is connected to a penstock with a
turbine
inlet valve. This
requires a different type of arrangement from the
one shown here. As
mentioned before, the Michell turbine is unique
because its [B.sub.1] and [B.sub.2] widths can be altered to
suit power-site traits
of flow rate and head.
This, besides simplicity and low cost, makes
it the most suitable of all water turbines for small power
developments.
C. Centrifugal Pumps and Propeller-Type Pumps
The use of
centrifugal pumps or propeller-type pumps as turbines
should be explored
before all other alternatives, provided that
direct-current
electricity can be used (See Figures 29 and 30).
lcd29320.gif (600x600)
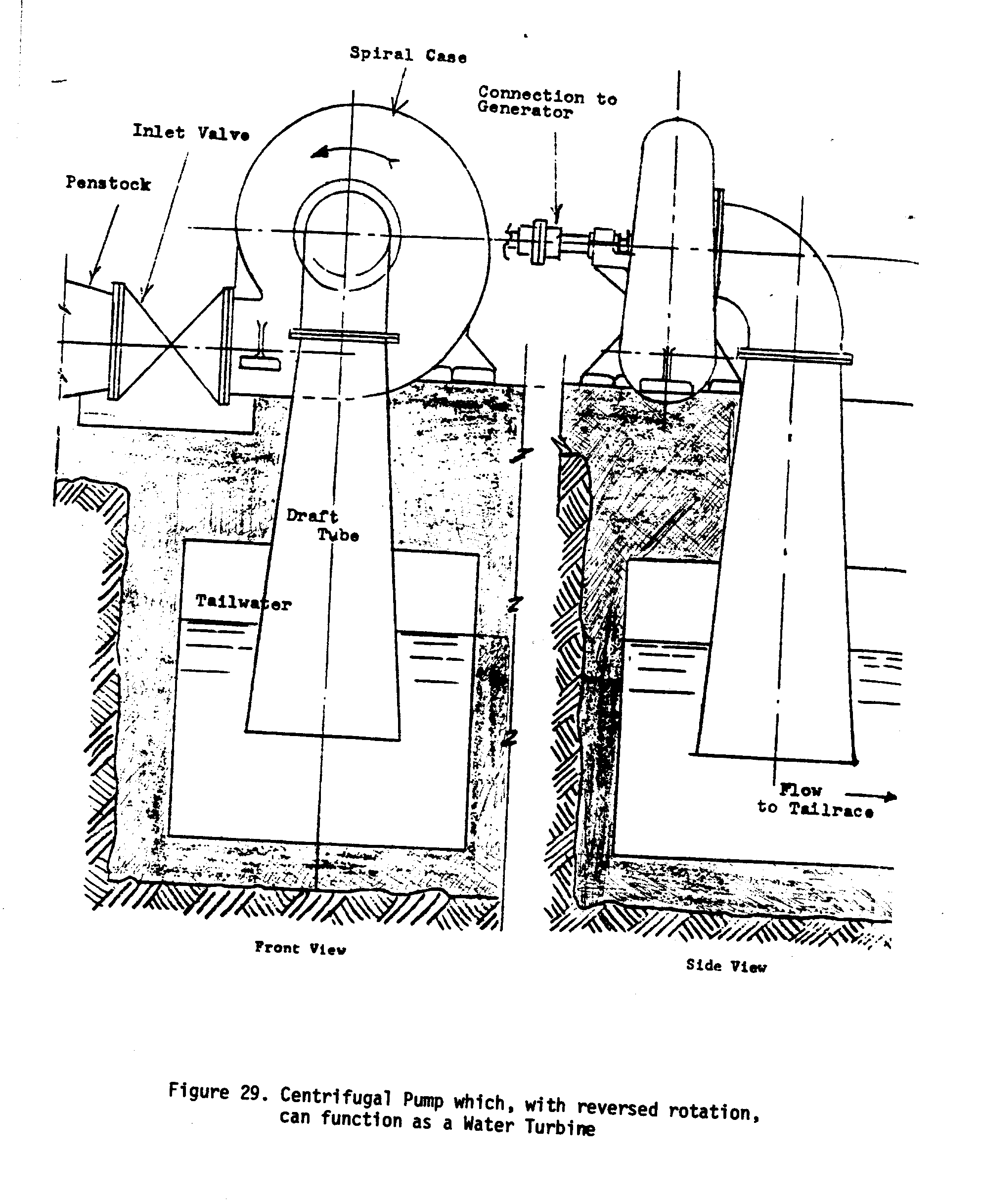
cost and are
available in many sizes. Manufacturers
can quote
the proper unit if
head and flow are given.
They can be used
to produce alternating current also, but with increased
cost.
In this case, a butterfly valve is used as
the turbine-inlet
valve; and the
valve can be regulated by a small water-turbine
governor.
The help of an engineer should be sought in
modifying these pumps for
use as turbines.
IX. WATER WHEELS
Water wheels date
back to biblical times but are far from obsolete.
They have certain advantages which should not be
overlooked. They are
more economical for small power requirements than water
turbines in some
cases. It is
possible to make a water wheel for power requirements up to
10 horsepower in places where there are no elaborate
manufacturing
facilities.
Water wheels are attractive especially
where fluctuations in flow rate
are large. Speed
regulation is not practical -- therefore, water wheels are
used primarily to drive machinery which can take large
fluctuations in
rotational speed.
They operate between 2 and 12 revolutions per minute
and require gearing and belting (with inherent friction
loss) to run most
machines. Thus, they
are most useful for slow-speed applications, e.g.,
flour mills, some agricultural equipment, and some pumping
operations.
A water wheel,
because of its rugged design, requires less care than
a turbine does. It
is self-cleaning, and, therefore, need not be protected
from debris (leaves, grass and stones).
The two main types of
water wheels are the overshot and the undershot.
A. Overshot Water Wheel
The overshot water
wheel way be used with heads of 10 to 30 feet, and
flow rates from
one to 30 cubic feet per second.
The water is
guided to the wheel in a timber or metal flume at a
water velocity of
approximately 3 feet per second. A gate
at the
end of the flume
controls the flow to the wheel and the jet velocity,
which should be
from 6 to 10 feet per second. To obtain
this velocity,
the head
([H.sub.1] in Figure 31) should be one to two feet.
Wheel width
lcd31x34.gif (600x600)

depends on he
amount of water to be used. The
discharge will be one
to two cubic feet
per-second for a flume width of one foot.
Wheel
width must exceed
flume width by about one foot because of jet
expansion.
The efficiency of a well-constructed
overshot water wheel
can be 60% to 80%.
B. Undershot Water Wheel
The undershot
water wheel (Figure 32) should be used with heads of 1.5
lcd32x35.gif (600x600)
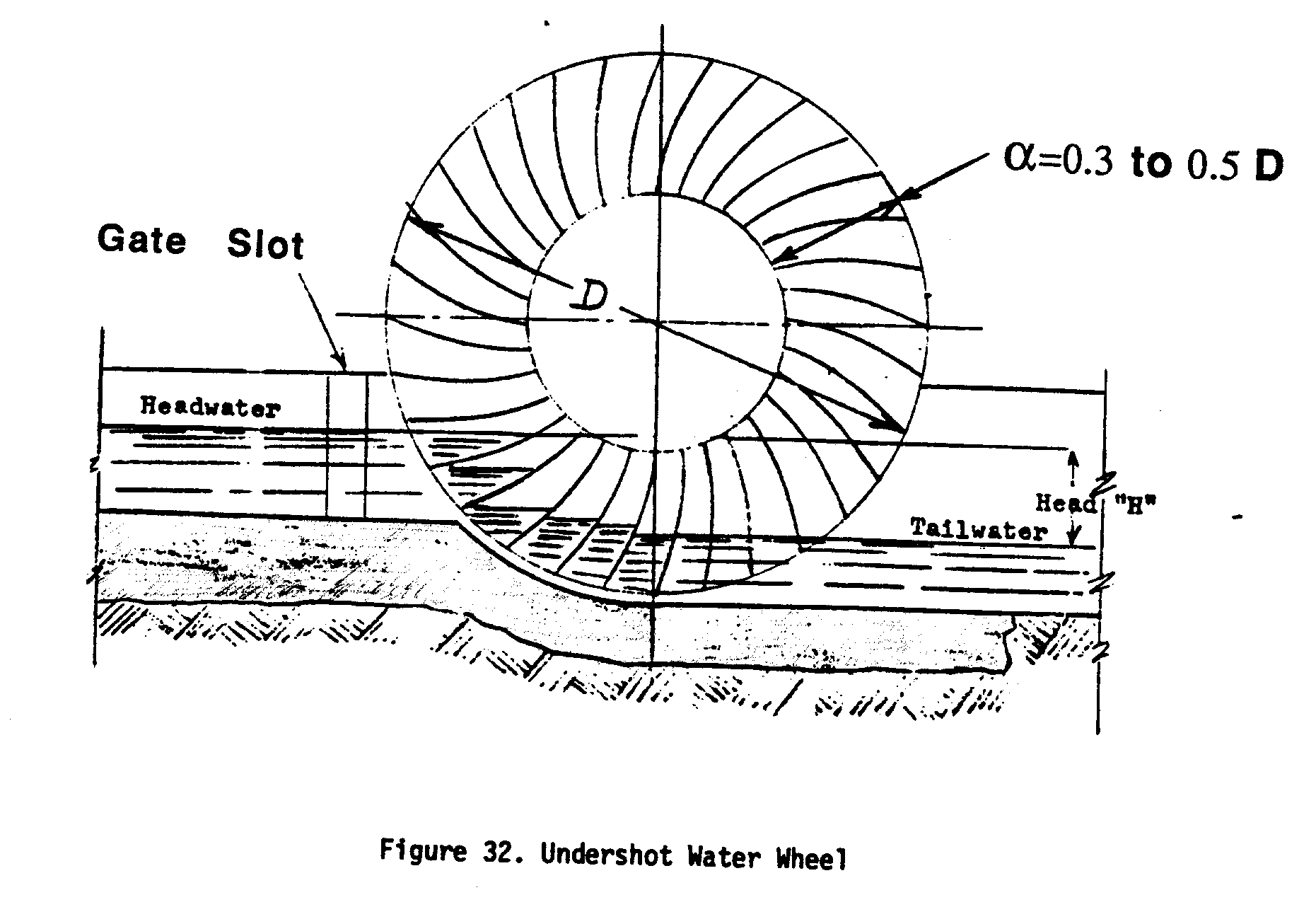
to 10 feet and
flow rates from 10 to 100 cubic feet per second.
Wheel
diameter should be
3 to 4 times the head -- wheel diameters between 6
and 30 feet.
Rotational speed should be 2 to 12
revolutions per minute,
with the higher
speed applying to the smaller wheels.
For each foot
of wheel width,
the flow rate should be between 3 and 10 cubic feet
per second.
The wheel dips from one to three feet into
the water.
Efficiency is in
the range of 60% to 75%.
X. EXAMPLES
Mission Hospital
1. Requirements: 10
kilowatt light and power plant.
2. 10 kilowatts is 13 1/3 horsepower.
3. The gross power required is then about 27 horsepower.
4. A stream in hilly territory can be dammed up and the
water
channeled through
a ditch 112 mile long to the power plant site.
5. A penstock 250 feet long will take the water to the
turbine.
6. The total difference in elevation is 140 feet.
7. Available minimum flow rate: 1.8 cubic feet/second.
8. The soil in which the ditch is to be dug permits a water
velocity
of 1.2 feet per
second.
9. Table II, Section VI gives n= 0.030
10. Area of flow in the ditch = 1.8/1.2 = 1.5 square feet.
11. Bottom width = 1.5 feet.
12. Hydraulic radius = 0.31 X 1.5 = 0.46 feet.
13. Figure 8 shows that this results in a fall and head loss
of 1.7 feet
lcd8x8.gif (486x486)
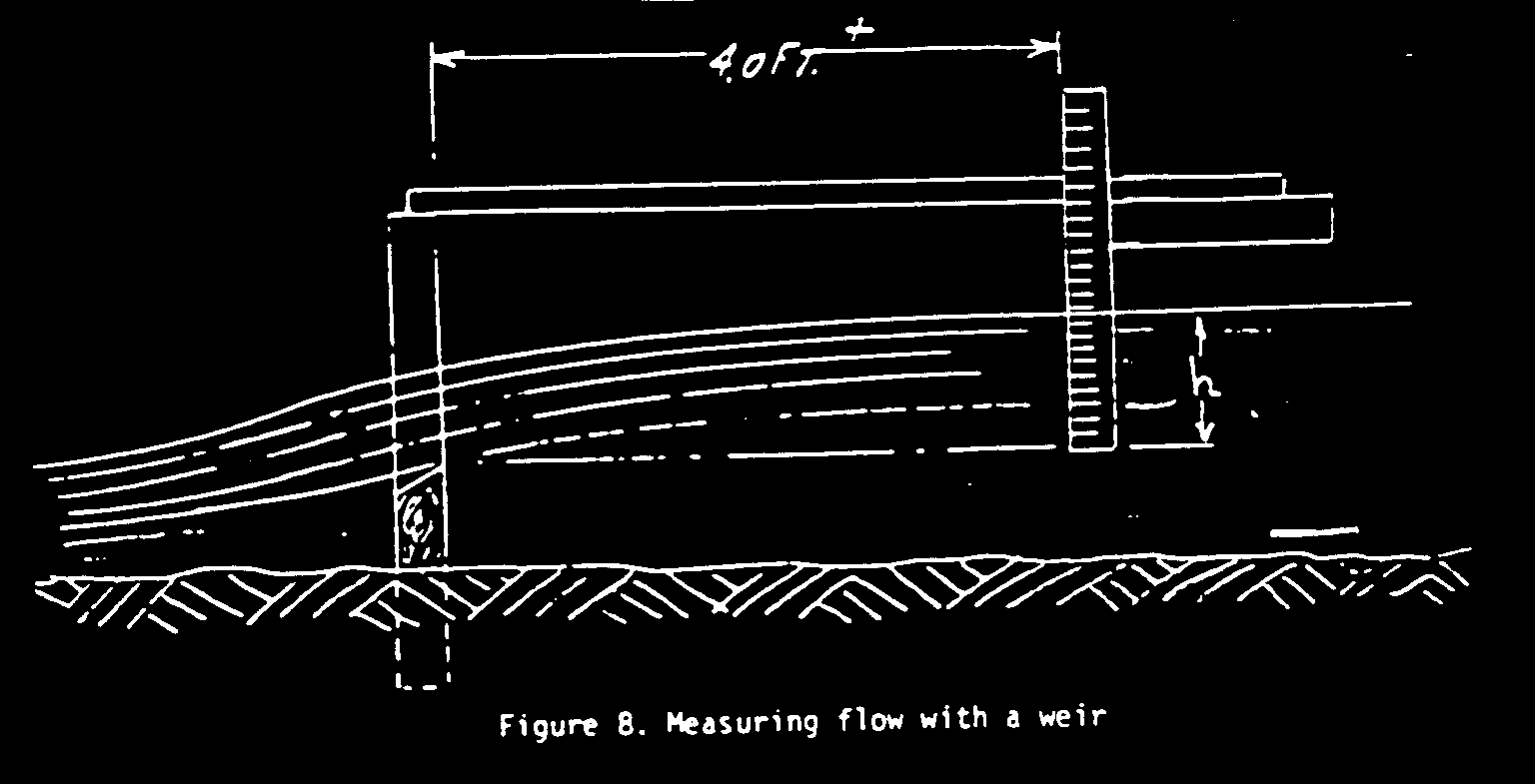
for 1,000 feet.
The total for the half-mile (2,64C feet)
ditch is
4.5 feet.
14. The fall that is left through the penstock is then:
140-4.5 = 135.5
feet.
Figure 10 gives 5.7 inches as the required
penstock diameter
lcd10x11.gif (600x600)

for 1.8 cubic
feet per second flow at 10 feet per second velocity.
15. Head loss in the penstock is 10 feet for 100 feet of
length and
25 feet for the
total length of 250 feet.
16. For the water tubine:
Net Head =
135.5-25 = 110.5 feet
17. Power produced by the turbine at 80% efficiency:
Net Power =
Minimum water flow X net head/8.8 X Turbine Efficiency
=1.8 X
110.5/8.8 X .80 = 18 horsepower
18. Consult Table III.
The cost of a pump or turbine for a particular
situation can
only be learned by writing to the various manufacturers.
VITA engineers
can step in here, lay out the physical
arrangement and
compile a list of necessary mechanical and
electrical
components to the best advantage of the field worker.
Appendix 1
AVAILABILITY OF MANUFACTURED TURBINES
Small hydraulic
turbines and even more the governors for regulating
these turbines are difficult to obtain because the demand
for these products
has diminished to a considerable extent in the last twenty
years. And
manufactured water wheels are completely off the
market. Of the remaining
number of manufacturers of small turbines and governors only
one exists in
the United States, and two are known by the author to exist
in Europe.
The James Leffel
& Company is located in Springfield, Ohio.
Their
booklet, Leffel Pamphlet "A".
Hints on the Development of Small Water
Power, is available on request.
It is a very useful supplement to the
information in this manual.
Its description of Leffel's small vertical
Samson turbine is very complete.
This turbine is available in sizes from
3 to 29 horsepower.
The company maintains an engineering department
which stands ready to assist in planning and design of the
entire installation.
This company also
manufactures a complete unit called Hoppes Hydroelectric
Unit, which is useful in isolated locations where the demand
is
small. It comes in
sizes of I to 10 kilowatts. A Leffel
bulletin
describing this unit gives complete instructions on
submitting the
information necessary for ordering it.
The Michell (or
Banki) turbine is manufactured exclusively by the
Ossberger-Turbinenfabrik of Weissenburg, Bavaria,
Germany. This turbine
is made in sizes ranging from 1 to 1000 horsepower.
The company has an
impressive record of installations, many in less-developed
countries.
Ossberger-Turbinenfabrik is very responsive to requests for
information.
It furnishes without charge a considerable amount of data,
translated
into English. The
simple design of the Michell turbine makes it a
favorite for remote regions and is priced lower than
corresponding
Francis and impulse type turbines.
Its governor, developed by Ossberger,
is also very reasonably priced.
A third company
which manufactures turbines and governors for turbines
but does not sell packaged units, including the electrical
equipment, is
the Officine Buehler, Taverne.
Canton Ticino.
Switzerland. They are in
the small turbine field, and they manufacture all types
except Michell.
Their workmanship is of the highest quality, and their
engineering is
superb. Like the
other companies, they assist prospective customers in
planning their installations.
Appendix 2
CONVERSION TABLES
Units of Length
1 Mile
= 1760 Yards
= 5280 Feet
1 Kilometer
= 1000 Meters
= 0.6214 Mile
1 Mile
= 1.607 Kilometers
1 Foot
= 0.3048 Meter
1 Meter
= 3.2808 Feet
= 39.37 Inches
1 Inch
= 2.54 Centimeters
1
Centimeter = 0.3937 Inch
Units of Area
1 Square
Mile = 640 Acres
= 2.5899 Square Kilometers
1 Square
Kilometer = 1,000.000 Sq.
Meters = 0.3861 Square Mile
1 Acre
= 43.560 Square Feet
1 Square
Foot = 144 Square
Inches = 0.0929 Square Meter
1 Square
Inch = 6.452 Square
Centimeters
1 Square
Meter = 10.764 Square Feet
1 Square
Centimeter = 0.155 Square Inch
Units of Volume
1.0 Cubic
Foot = 1728 Cubic
Inches = 7.48 U.S. Gallons
1.0 British Imperial Gallon = 1.2 U.S.
Gallons
1.0 Cubic
Meter = 35.314 Cubic
Feet = 264.2 U.S. Gallons
1.0 Liter
= 1000 Cubic Centimeters =
0.2642 U.S. Gallons
Units of Weight
1.0 Metric
Ton
= 1000 Kilograms
= 2204.6 Pounds
1.0
Kilogram = 1000 Grams
= 2.2046 Pounds
1.0 Short
Ton = 2000 Pounds
CONVERSION TABLES
Units of Pressure
1.0 Pound per
square inch
= 144 Pound per square foot
1.0 Pound per
square inch = 27.7 Inches of
Water(*)
1.0 Pound per
square inch = 2.31 Feet of
Water(*)
1.0 Pound per
square inch = 2.042 Inches of
Mercury(*)
1.0 Atmosphere
= 14.7 Pounds per
square inch (PSI)
1.0
Atmosphere = 33.95
Feet of Water(*)
1.0 Foot of
Water = 0.433 PSI = 62.355 Pounds
per square foot
1.0 Kilogram per
square centimeter = 14.223 pounds per
square inch
1.0 pound per
square inch = 0.0703 kilogram
per square centimeter
(*) at 62 degrees Fahrenheit (16.6 degrees Celsius)
Units of Power
1.0 Horsepower
(English) = 746 Watt
= 0.746 Kilowatt (KW)
1.0 Horsepower
(English) = 550 foot pounds
per second
1.0 Horsepower
(English) = 33,000 foot
pounds per minute
1.0 Kilowatt
(KW) = 1000 Watt = 1.34
Horsepower (HP) English
1.0 Horsepower
(English)
= 1.0139 Metric Horsepower
(cheval-vapeur)
1.0 Metric
Horsepower = 75 Meter X
Kilogram/Second
1.0 Metric
Horsepower = 0.736
Kilowatt = 736 Watt
Appendix 3
BIBLIOGRAPHY
General Texts and Handbooks
Brown, J. Guthrie ed, Hydro Electric Engineering
Practice. New York:
Gordon &
Breach, 1958; London: Blackie and Sons,
Ltd., 1958. A
very complete
treatise covering the entire field of hydroelectric
engineering.
Three volumes.
v. 1 Civil Engineering $50.00 U.S.
v. 2 Mechanical
and Electrical Engineering $30.00 U.S.
v. 3 Economics,
Operation and Maintenance ($25.00 U.S.)
Creager, W. P. and Justin, J. D.
Hydro Electric Handbook.
2d ed.
New York:
John Wiley and Son, 1950.
A most complete handbook
covering the
entire field. Especially good for
reference.
($18.50 U.S.)
Davis, Calvin V.
Handbook of Applied Hydraulics.
2d ed. New York:
McGraw-Hill,
1952. A comprehensive handbook covering
all phases
of applied
hydraulics. Several chapters are
devoted to hydroelectric
application.
($23.50 U.S.)
Paton, T. A. L.
Power from Water. London:
Leonard Hill, 1961.
A
concise general
survey of hydroelectric practice in abridged form.
($8.50 U.S.)
Zerban, A. H. and Nye, E.P.
Power Plants. 2d ed. Scranton,
Penn.:
International Text
Book Co., 1952. Chapter 12 gives a
concise
presentation of
hydraulic power plants. ($8.00 U.S.)
The Banki Turbine
Haimerl, L. A., "The Cross Flow Turbine," Water
Power (London), January
1960.
Reprints available from Ossberger
Turbinenfabrik, 8832 Weissenburg,
Bayern,
Germany. This article describes a type
of water turbine
which is being
used extensively in small power stations, especially
in Germany.
Mockmore, C. A. and Merryfield, F., The Banki Water
Turbine. Corvallis,
Ore.:
Oregon State College Engineering Experiment
Station Bulletin
No. 25, February
1949. 40c.
A translation of a paper by Donat Banki.
A highly technical
description of this turbine, originally invented
by Michell,
together with the results of tests.
Small Michell (Banki) Turbine. Arlington, Virginia:
Volunteers in
Technical
Assistance (VITA), 1979.
Appendix 4
THE AUTHOR AND REVIEWERS
Hans W. Hamm, a
VITA Volunteer, was a consultant on small water
power developments for twenty years with a Pennsylvania
manufacturer
of water wheels and small turbines.
He earned a degree in mechanical
engineering from the State Technical University of
Braunschweig in his
native Germany. He
retired in 1966 from the York, Pennsylvania, works
of Allis-Chalmers.
***
Other VITA
Volunteers have helped in producing this manual:
Morton
Rosenstein, public relations and market research manager at
Ionics, Inc.,
Watertown, Massachusetts, edited the entire manual.
Harry Wiersoma,
consulting engineer of Knoxville, Tennessee, made
many helpful suggestions based on more than fifty years'
experience in
hydraulic engineering.
He also wrote the preface for the manual and
prepared the bibliography.
Dr. John J.
Cassidy, associate professor of civil engineering,
University of Mitsouri, and Robert H. Emerick, consulting
engineer
of Charleston, South Carolina, both reviewed the manual for
technical
accuracy.
Ian D. Burnet,
projects officer of the Department of Trade and
Industry, Port Moresby, Papua, New Guinea, reviewed the book
from the
point of view of the eventual user, the community
development leader.
***
The manual was also
reviewed by Jeffrey Ashe and John Brandi,
Peace Corps Volunteers who were working on a project to
develop a small
water power site in Loja, Ecuador, by Ossberger
Turbinenfabrik,
Weissenburg (Bayern), Germany and by James Leffel &
Company,
Springfield, Ohio.
Appendix 5
DATA SHEET
This form is given
as a guide to help you collect the
information a VITA engineer would need to help you plan a
small
water power site.
TO: Volunteers in
Technical Assistance
1600 Wilson
Boulevard, Suite 500
Arlington, Virginia
22209 USA
1. Minimum flow of
water available in cubic feet per second
(or cubic meters)
per second.
__________________
2. Maximum flow of
water available in cubic feet per second
(or cubic meters)
per second.
__________________
3. Head or fall of
water in feet (or meters)
__________________
4. Length of pipe
line in feet (or meters) needed to get the
required
head.
__________________
5. Describe water
condition (clear, muddy, sandy, acid)
__________________
6. Describe soil
condition (see Table II)
__________________
7. Minimum tailwater
elevation in feet (or meters)_________________
8. Approximate area
of pond above dam in acres (or square
kilometers).
__________________
9. Approximate depth
of the pond in feet (or meters)_______________
10. Distance from power plant to where electricity will be
used in feet (or
meters).
__________________
11. Approximate distance from dam to power plant
__________________
12. Minimum air temperature.
__________________
13. Maximum air temperature.
__________________
14. Estimate power to be used.
__________________
15. ATTACH SITE SKETCH WITH ELEVATIONS, OR TOPOGRAPHICAL MAP
WITH
SITE SKETCHED IN.
Date_______________
Name__________________ _____________
Address_______________ _____________
See reverse for guide in
_______________ _____________
collecting further helpful
_____________________________
information.
DATA SHEET - 2
The following
questions cover information which, although
not necessary in starting to plan a water power site, will
usually be needed later.
If it can possibly be given early in
the project, this will save time later.
1. Give the type, power and speed of the machinery to be
driven and
indicate whether direct, belt or gear drive is
desired or
acceptable.
2. For electric current, indicate whether direct current is
acceptable or
alternating current is required. Give
the
desired voltage,
number of phases and frequency
3. Say whether manual flow regulation can be used (with D.C.
and very small
A.C. plants) or if regulation by an automatic
governor is
needed.
Appendix 6
DECISION MAKING WORK SHEET
If you are using this guide in a development effort, collect
as
much information as possible and if you need assistance with
the
project, write VITA.
A report on your experiences and the uses of
this manual will help VITA both improve the book and aid
other
similar efforts.
Volunteers in Technical Assistance
1600 wilson Boulevard, Suite 500
Arlington, Virginia 22209, USA
CURRENT USE AND AVAILABILITY
o Describe current agricultural and domestic practices that
rely
on water.
What are the sources of water and how are
they used?
o What water power sources are available? Are they small but
fast-flowing? Large
but slow-flowing? Other characteristics?
o What is water used for traditionally?
o Is water harnessed to provide power for any purpose? If
so,
what and with what
positive or negative results?
o Are there dams already built in the area? If so, what have
been
the effects of the
damming? Note particularly any evidence of
sediment carried by
the water--too much sediment can create a
swamp.
o If water resources are not harnessed, what seem to be the
limiting factors?
Does cost seem prohibitive? Does the lack of
knowledge of water
power potential limit its use?
NEEDS AND RESOURCES
o Based on current agricultural and domestic practices, what
seems to be the
area of greatest need? Is power needed to run
simple machines
such as grinders, saws, pumps?
o Given available water power sources, which ones seem to be
available and most
useful? For example, one stream that runs
quickly year around
and is located near the center of agricultural
activity may be the
only feasible source to tap for
power.
o Define water power sites in terms of their inherent
potential
for power
generation.
o Are materials for constructing water power technologies
available
locally? Are local
skills sufficient? Some water power
applications demand
a rather high degree of construction skill.
o How much skilled labor is necessary for construction and
maintenance? What
kinds of skills are available locally? Can
you meet the need?
Do you need to train people?
o Some aspects of turbine construction require someone with
experience in metalworking
and/or welding. Is this skill
available?
o Waterwheel construction may require woodworkers.
Are they
available?
o Is help available for dam building? Surveying? Determining
environmental
impacts?
o Do a cost estimate of the labor, parts, and materials
needed.
o How will the project be funded?
o What is your schedule? Are you aware of holidays and
planting
or harvesting
seasons, which may affect timing?
o How will you arrange to spread information on and promote
use
of the technology?
IDENTIFY POTENTIAL
o Is more than one water power technology applicable?
Remember to
look at all the
costs. While one technology appears to
be much
more expensive in
the beginning, it could work out to be less
expensive after all
costs are weighed.
o Are there choices to be made between a waterwheel and a
windmill, for
example, to provide power for grinding grain?
Again weigh all the
costs: economics of tools and labor,
operation
and maintenance,
social and cultural dilemmas.
o Are there local skilled resources to introduce water power
technology? Dam
building and turbine construction should be
considered
carefully before beginning work.
Besides the higher
degree of skill
required in turbine manufacture (as opposed to
waterwheel
construction), these water power installations tend
to be more
expensive.
o Where the need is sufficient and resources are available,
consider
a manufactured
turbine and a group effort to build the
dam and install the
turbine.
o Is there a possibility of providing a basis for small
business
enterprise?
FINAL DECISION
o How was the final decision reached to go ahead--or not go
ahead--with this
project? Why?
Appendix 7
RECORD KEEPING WORK SHEET
Detailed records of project implementation are helpful to
ongoing
project management and to other people who may be involved
in
similar efforts elsewhere.
CONSTRUCTION
Photographs of the construction and installation process, as
well
as the finished result, are helpful.
They add interest and detail
that might be overlooked in the narrative.
A report on the construction process should include much
very
specific information.
This kind of detail can often be monitored
most easily in charts (such as the one below). <see
report 1>
lcdrp10.gif (437x437)
Some other things to record include:
o Specification of materials used in construction.
o Adaptations or changes made in design to fit local
conditions.
o Equipment costs.
o Time spent in construction--include volunteer time as well
as
paid labor; full-
or part-time.
o Problems--labor shortage, work stoppage, training
difficulties,
materials shortage,
terrain, transport.
OPERATION
Keep log of operations for at least the first six weeks,
then
periodically for several days every few months.
This log will
vary with the technology, but should include full
requirements,
outputs, duration of operation, training of operators, etc.
Include special problems that may come up--a damper that
won't
close, gear that won't catch, procedures that don't seem to
make
sense to workers, etc.
MAINTENANCE
Maintenance records enable keeping track of where breakdowns
occur most frequently and may suggest areas for improvement
or
strengthening weakness in the design.
Furthermore, these records
will give a good idea of how well the project is working out
by
accurately recording how much of the time it is working and
how
often it breaks down.
Routine maintenance records should be kept
for a minimum of six months to one year after the project
goes
into operation. <see report 2>
lcdrp2.gif (437x437)
SPECIAL COSTS
This category includes damage caused by weather, natural
disasters,
vandalism, etc.
Pattern the records after the routine
maintenance records.
Describe for each separate incident:
o Cause and extent of damage.
o Labor costs of repair (like maintenance account).
o Material costs of repair (like maintenance account).
o Measures taken to prevent recurrence.
========================================
========================================