WIND ENERGY FOR WATER PUMPING
Overview
There are many places in the world where wind energy is a
good alternative for
pumping water. Specifically these include windy areas with
limited access to other
forms of power. In order to determine whether wind power is
appropriate for a
particular situation an assessment of its possibilities and
the alternatives should
be undertaken. The necessary steps include the following:
1. Identify the
users of the water.
2. Assess the water
requirement.
3. Find the pumping
height and overall power requirements.
4. Evaluate the wind
resources.
5. Estimate the size
of the wind machine(s) needed.
6. Compare the wind
machine output with the water requirement on a
seasonal basis.
7. Select a type of
wind machine and pump from the available options.
8. Identify possible
suppliers of machines, spare parts, repair, etc.
9. Identify
alternative sources for water.
10. Assess costs of various systems and perform economic
analysis to find
least cost
alternative.
11. If wind energy is chosen, arrange for obtaining and
installing the
machines and for
providing for their maintenance.
Decision Making Process
The following summarizes the key aspects of those suggested
steps.
1. Identify the Users
This step seems quite obvious, but should not be ignored. By
paying attention to
who will use the wind machine and its water it will be
possible to develop a
project that can have continuing success. Questions to
consider are whether they
are villagers, farmers, or ranchers; what their educational
level is; whether they
have had experience with similar types of technology in the
past; whether they
have access to or experience with metal working shops. Who
will be paying for
the projects? Who will be owning the equipment; who will be
responsible for
keeping it running; and who will be benefitting most?
Another important question
is how many pumps are planned. A large project to supply
many pumps may well
be different than one looking to supply a single site.
2. Assess the Water Requirements
There are four main types of uses for water pumps in areas
where wind energy is
likely to be used. These are: 1) domestic use, 2) livestock
watering, 3) irrigation,
4) drainage.
Domestic use will depend a great deal on the amenities
available. A typical
villager may use from 15 - 30 liters per day (4-8 gallons
per day). When indoor
plumbing is used, water consumption may increase
substantially. For example, a
flush toilet consumes 25 liters (6 1/2 gallons) with each
use and a shower may
take 230 (60 gallons.) When estimating water requirements,
one must also consider
population growth. For example, if the growth rate is 3
percent, water use would
increase by nearly 60 percent at the end of 15 years, a
reasonable lifetime for a
water pump.
Basic livestock requirements range from about 0.2 liters
(0.2 quart) a day for
chickens or rabbits to 135 liters (36 gallons) a day for a
milking cow. A single
cattle dip might use 7500 liters (2000 gallons) a day.
Estimation of irrigation requirements is more complex and
depends on a variety of
meteorological factors as well as the types of crops
involved. The amount of
irrigation water needed is approximately equal to the
difference between that
needed by the plants and that provided by rainfall. Various
techniques may be
used to estimate evaporation rates, due for example to wind
and sun. These may
then be related to plant requirements at different stages
during their growing
cycle. By way of example, in one semi-arid region irrigation
requirements varied
from 35,000 liters (9,275 gallons) per day per hectare (2.47
acres) for fruits and
vegetables to 100,000 liters (26,500 gallons) per day per
hectare for cotton.
Drainage requirements are very site dependent. Typical daily
values might range
from 10,000 to 50,000 liters (2,650 to 13,250 gallons) per
hectare.
In order to make the estimate for the water demand, each
user's consumption is
identified, and summed up to find the total. As will become
apparent later. It is
desirable to do this on a monthly basis so that the demand
can be related to the
wind resource.
3. Find Pumping
Height and Total Power Requirement
If wells are already available their depth can be measured
directly. If new wells
are to be dug, depth must be estimated by reference to other
wells and knowledge
of ground water characteristics in the area. The total
elevation, or head, that the
pump must work against, however, is always greater than the
static well depth.
Other contributors are the well draw down (the lowering of
the water table in
the vicinity of the well while pumping is underway), the
height above ground to
which the water will be pumped (such as to a storage tank),
and frictional losses
in the piping. In a properly designed system the well depth
and height above
ground of the outlet are the most important determinants of
pumping head.
The power required to pump water is proportional to its mass
per unit volume, or
density (1000 kg/[m.sup.3]), the acceleration of gravity (g=
9.8 m/[s.sup.2], the total pumping
head (m), and the volume flow rate of water ([m.sup.3]/s).
Power is also inversely
proportional to the pump efficiency. Note that 1 cubic meter
equals 1000 liters.
Expressed as a formula,
Power = Density x Gravity x Head x Flow rate
Example:
To pump 50
[m.sup.3] in one day (0.000579 [m.sup.3]/s) up a total head of 15 m
would require:
Power = (1000
kg/[m.sup.3]) (9.8m/[s.sup.2]) (15m) (.000579[m.sup.3]/s) = 85 watts.
Actual power
required would be more because of the less than perfect
efficiency of the
pump.
Sometimes needed pumped power is described in terms of daily
hydraulic requirement,
which is often given in the units of [m.sup.3] [multiplied
by] m/day. For example, in the above
example the hydraulic requirement is 750 [m.sup.3]
[multiplied by] m/day.
4. Evaluate Wind Resource
It is well known that the power in the wind varies with the
cube of the wind
speed. Thus if the wind speed doubles, the available power
increases by a factor
of eight. Hence it is very important to have a good
understanding of the wind
speed patterns at a given site in order to evaluate the
possible use of a wind
pump there. It is sometimes recommended that a site should
have an average wind
speed at the height of a wind rotor of at least 2.5 m/s in
order to have potential
for water pumping. That is a good rule of thumb, but by no
means the whole
story. First of all, one seldom knows the wind speed at any
height at a prospective
windmill site, except by estimate and correlation. Second,
mean wind speeds
generally vary with the time of day and year and it makes an
enormous difference
if the winds occur when the water is needed.
The best way to evaluate the wind at a prospective site is
to monitor it for at
least a year. Data should be summarized at least monthly.
This is often impossible,
but there should be some monitoring done if a large wind
project is envisioned.
The most practical approach may be to obtain wind data from
the nearest weather
station (for reference) and try to correlate it with that at
the proposed wind
pump site. If at all possible the station should be visited
to ascertain the
placement of the measuring instrument (anemometer) and its
calibration. Many
times anemometers are placed too near the ground or are
obscured by vegetation
and so greatly underestimate the wind speed. The correlation
with the proposed
site is best done by placing an anemometer there for a
relatively short time (at
least a few weeks) and comparing resulting data with that
taken simultaneously at
the reference site. A scaling factor for the long-term data
can be deduced and
used to predict wind speed at the desired location.
Of course, possible locations for wind machines are limited
by the placement of
the wells, but a few basic observations should be kept in
mind. The entire rotor
should be well above the surrounding vegetation, which
should be kept as low as
possible for a distance of at least ten times the rotor
diameter in all directions.
Wind speed increases with elevation above ground, usually by
15-20 percent with
every doubling of height (in the height range of most wind
pumps). Because of
the cubic relationship between wind speed and power, the
effect on the latter is
even more dramatic.
5. Estimate Wind Machines Size
A typical wind pump is shown in Figure 1. Most wind pumps
have a horizontal
fig1x121.gif (600x600)
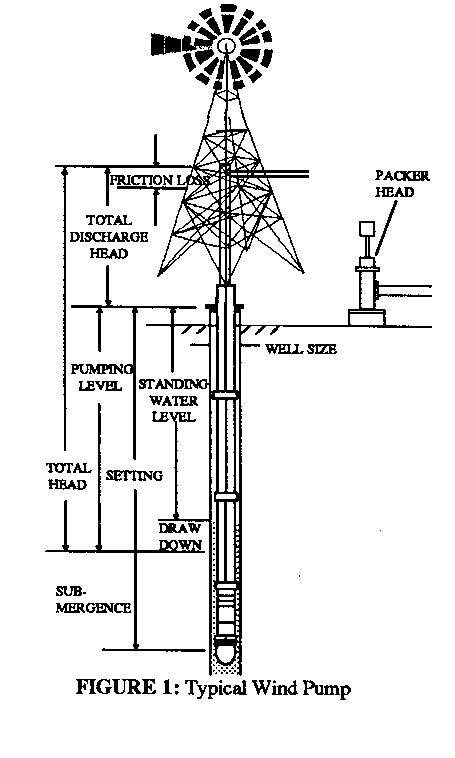
axis (that is, the rotating shaft is parallel to the
ground). Vertical axis machines,
such as the Savonius rotor, have usually been less
successful in practice.
In order to estimate wind machine's size it is first
necessary to have some idea
how it will perform in real winds. As previously mentioned,
the power in wind
varies with the cube of the wind speed. It is also
proportional to the density of
the air. Atmospheric density is 1.293 kg/[m.sup.3] at sea
level at standard conditions but
is affected by temperature and pressure. The power that a
wind machine produces,
in addition, depends on the swept area of its rotor and the
aerodynamic characteristics
of its blades. Under ideal conditions the rotational speed
of the rotor
varies in direct relation to the wind speed. In this case
the efficiency of the
rotor remains constant and power varies as the cube of the
wind speed (and
rotational speed).
With wind pumps, however, the situation is more complicated.
The majority use
piston pumps, whose power requirements vary directly with
the speed of the
pump. At high wind speeds the rotor can produce more power
than the pump can
use. The rotor speeds up, causing its efficiency
to drop, so it produces less power. The
pump, coupled to the rotor, also moves more
rapidly so it absorbs more power. At a
certain point the power from the rotor equals
the power used by the pump, and the rotational
speed remains constant until the wind
speed changes.
The net effect of all this is that the whole
system behaves rather differently than an
ideal wind turbine. Its actual performance is
best described by a measured characteristic
curve (Figure 2), which relates actual water
fig2x121.gif (540x540)
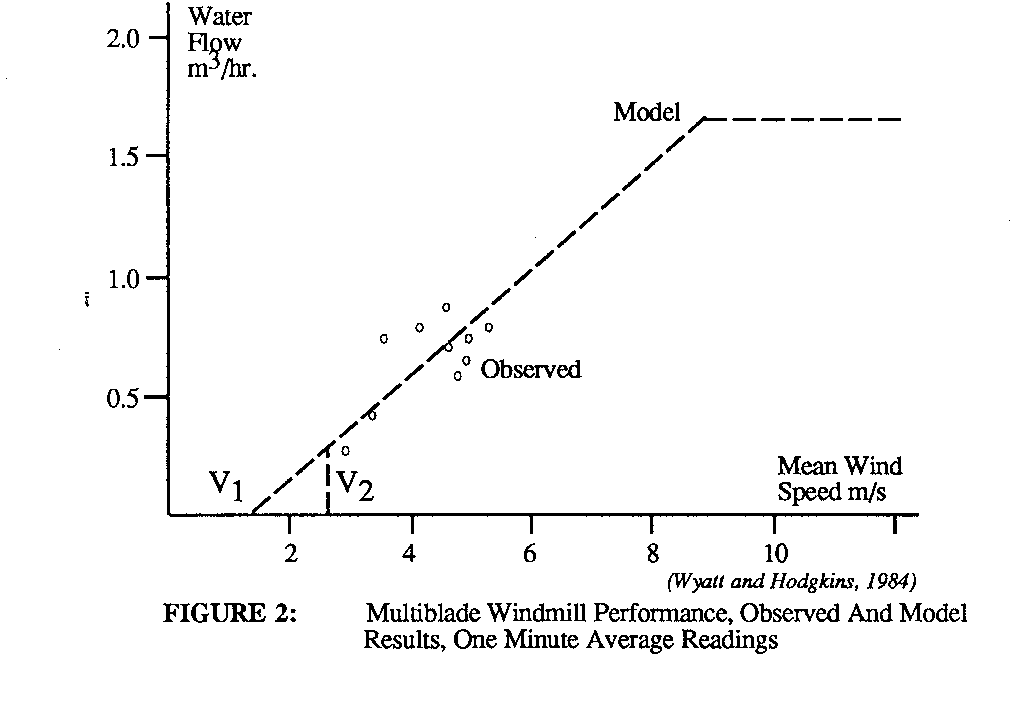
flow at given pumping heads to the wind
speed. This curve also reflects other important
information such as the wind speeds at
which the machine starts and stops pumping
(low wind) and when it begins to turn away
in high winds (furling).
Most commercial machines and those developed and tested more
recently have
such curves and these should be used if possible in
predicting wind machine
output. On the other hand, it should be noted that some
manufacturers provide
incomplete or overly optimistic estimates of what their
machines can do. Sales
literature should be examined carefully.
In addition to the characteristic curve of the wind machine,
one must also know
the pattern of the wind in order accurately to estimate
productivity. For example,
suppose it is known how many hours (frequency) the average
wind speed was
between 0-1 m/s, 1-2 m/s, 2-3 m/s, etc., in a given month.
By referring to the
characteristic curve, one could determine how much water was
pumped in each of
the groups of hours corresponding to those wind speed ranges.
The sum of water
from all groups would be the monthly total. Usually such
detailed information on
the wind is not known. However, a variety of statistical
techniques are available
from which the frequencies can be predicted fairly
accurately, using only the
long-term mean wind speed and, when available, a measure of
its variability
(standard deviation). See Lysen, 1983, and Wyatt and
Hodgkin, 1984.
Many times there is little information known about a
possible machine or it is
just desired to know very approximately what size machine
would be appropriate.
Under these conditions the following simplified formula can
be used:
Power = Area x
0.1 x [(Vmean).sup.3]
where
Power = useful
power delivered in pumping the water, watts
Area = swept area
of rotor (3.14 x Radius squared), [m.sup.2]
Vmean = mean wind
speed, m/s
By rearranging the above equation, an approximate diameter
of the wind rotor can
be found. Returning to the earlier example, to pump 50
[m.sup.3]/day, 15 m would
require an average of 85 watts. Suppose the mean wind speed
was 4 m/s. Then
the diameter (twice the radius) would be:
Diameter = 2
[Power/(3.14) x 0.1 x [Vmean.sup.3])]
or
Diameter = 2 x
[85/(3.14 x 0.1 x [4.sup.3])] = 4.1 m
6. Compare Seasonal Water Production to Requirement
This procedure is usually done on a monthly basis. It
consists of comparing the
amount of water that could be pumped with that actually
needed. In this way it
can be told if the machine is large enough and conversely if
some of the time
there will be excess water. This information is needed to
perform a realistic
economic analysis. The results may suggest a change in the
size of machines to be
used.
Comparison of water supply and requirement will also aid in
determining the
necessary storage size. In general storage should be equal
to about one or two
days of usage.
7. Select Type of Wind Machine and Pump
There is a variety of types of wind machines that could be
considered. The most
common use relatively slow speed rotors with many blades,
coupled to a reciprocating
piston pump.
Rotor speed is described in terms of the tip speed ratio,
which is the ratio
between the actual speed of the blade tips and the free wind
speed. Traditional
wind pumps operate with highest efficiency when the tip
speed ratio is about 1.0.
Some of the more recently developed machines, with less
blade area relative to
their swept area, perform best at higher tip speed ratios
(such as 2.0).
A primary consideration in selecting a machine is its
intended application.
Generally speaking, wind pumps for domestic use or livestock
supply are designed
for unattended operation. They should be quite reliable and
may have a relatively
high cost. Machines for irrigation are used seasonally and
may be designed to be
manually operated. Hence they can be more simply constructed
and less expensive.
For most wind pump applications, there are four possible
types or sources of
equipment. These are: 1) Commercially available machines of
the sort developed
for the American West in the late 1800s; 2) Refurbished
machines of the first
types that have been abandoned; 3) Intermediate technology
machines, developed
over the last 20 years for production and use in developing
countries; and 4) Low
technology machines, built of local materials.
The traditional, American "fan mill," is a well
developed technology with very
high reliability. It incorporates a step down transmission,
so that pumping rate is
a quarter to a third of the rotational speed of the rotor.
This design is particularly
suitable for relatively deep wells (greater than 30m--100').
The main
problem with these machines is their high weight and cost
relative to their
pumping capacity. Production of these machines in developing
countries is often
difficult because of the need for casting gears.
Refurbushing abandoned traditional pumps may have more
potential than might at
first appear likely. In many windy parts of the world a
substantial number of
these machines were installed early in this century, but
were later abandoned
when other forms of power became available. Often these
machines can be made
operational for much less cost than purchasing a new one. In
many cases parts
from newer machines are interchangeable with the older ones.
By coupling refurbishing
with a training program, a maintenance and repair
infrastructure can be
created at the same time that machines are being restored.
Development of this
infrastructure will facilitate the successful introduction
of newer machines in the
future.
For heads of less than 30m, the intermediate technology
machines may be most
appropriate. Some of the groups working on such designs are
listed at the end of
this entry. These machines typically use a higher speed
rotor and have no gear
box. On the other hand they may need an air chamber to
compensate for adverse
acceleration effects due to the rapidly moving piston. The
machines are made of
steel, and require no casting and minimal welding. Their
design is such that they
can be readily made in machine shops in developing
countries. Many of these wind
pumps have undergone substantial analysis and field testing
and can be considered
reliable.
Low technology machines are intended to be built with
locally available materials
and simple tools. Their fabrication and maintenance, on the
other hand, are very
labor intensive. In a number of cases projects using these
designs have been less
successful than had been hoped. If such a design is desired,
it should first be
verified that machines of that type have actually been built
and operated successfully.
For a sobering appraisal of some of the problems encountered
in building
wind machines locally, see Wind Energy Development in Kenya
(see Sources).
Although most wind machines use piston pumps, other types
include mono pumps
(rotating), centrifugal pumps (rotating at high speed),
oscillating vanes, compressed
air pumps, and electric pumps driven by a wind electric
generator.
Diaphragm pumps are sometimes used for low head irrigation
(5-10 m or 16-32').
No matter what type of rotor is used, the pump must be sized
appropriately. A
large pump will pump more water at high wind speeds than
will a small one. On
the other hand, it will not pump at all at lower wind
speeds. Since the power
required in pumping the water is proportional to the head
and the flow rate, as
the head increases the volume pumped will have to decrease
accordingly. The
piston travel, or stroke, is generally constant (with some
exceptions) for a given
windmill. Hence, piston area should be decreased in
proportion to the pumping
head to maintain optimum performance.
Selecting the correct piston pump for a particular
application involves consideration
of two types of factors: 1) the characteristics of the rotor
and the rest of
the machine, and 2) the site conditions. The important
machine characteristics
are: 1) the rotor size (diameter); 2) the design tip speed
ratio; 3) the gear ratio;
and 4) the stroke length. The first two have been discussed
earlier. The gear
ratio reflects the fact that most wind pumps are geared down
by a factor of 3 to
4. Stroke length increases with rotor size. The choice is
affected by structural
considerations. Typical values for a machine geared down
3.5:1 range from 10 cm
(4") for a rotor diameter of 1.8 m (6') to 40 cm
(15")for a diameter of 5 m (16').
Note that it is the size of the crank driven by the rotor
(via the gearing) that
determines the stroke of the pump.
The key site conditions are: 1) mean wind speed and 2) well
depth. These site
factors can be combined with the machine parameters to find
the pump diameter
with the use of the following equation. This equation
assumes that the pump is
selected so that the machine performs best at the mean wind
speed.
DP = [square root of] (0.1) ([pi]) (DIAMR)[sup.3]
(VMEAN)[sup.2] (GEAR)
--------------------------------------------------
(DENSW) (G) (HEIGHT) (TSR) (STROKE)
where:
DP = Diameter of piston, m
[pi] = 3.1416
DIAMR = Diameter of the rotor, m
VMEAN = Mean wind speed, m/s
GEAR = Gear down ratio
DENSW = Density of water, 1000 kg/[m.sup.3]
G = Acceleration of gravity, 9.8 m/[s.sup.2]
HEIGHT = Total pumping head, m
TSR = Design tip speed ratio
STROKE = Piston stroke length, m
Example:
Suppose the wind machine
of the previous examples has a gear down ratio of
3.5:1, a design
tip speed ratio of 1.0 and a stroke of 30 cm. Then the
diameter of the
piston would be:
DP = [square
root of] (0.1) (3.14) (4.1)[sup.3] (4.0)[sup.2] (3.5)
-------------------------------------------- =
.166m
(1000) (9.8) (15) (1.0) (0.3)
8. Identify Suppliers of Machinery
Once a type of machine has been selected, suppliers of the
equipment or the
designs should be contacted for information about
availability of equipment and
spare parts in the region in question, references, cost,
etc. If the machine is to
be built locally, sources of material, such as sheet steel,
angle iron, bearings, etc.
will have to be identified. Possible machine shops should be
visited and their work
on similar kinds of fabrication should be examined.
9. Identify Alternative Power Sources for Water Pumping
There are usually a number of alternatives in any given
situation. What might be
a good option depends on the specific conditions. Some of
the possibilities include
pumps using human power (hand pumps), animal power (Persian
wheels, chain
pumps), internal combustion engines (gasoline, diesel, or
biogas), external combustion
engines (steam, Stirling cycle), hydropower (hydraulic rams,
norias), and solar
power (thermodynamic cycles, photovoltaics).
10. Evaluate Economics
For all the realistic options the likely costs should be
assessed and a life cycle
economic analysis performed. The costs include the first
cost (purchase or
manufacturing price), shipping, installation, operation
(including fuel where
applicable), maintenance, spare parts, etc. For each system
being evaluated the
total useful delivered water must also be determined (as
described in Step 6). The
life cycle analysis takes account of costs and benefits that
accrue over the life of
the project and puts them on a comparable basis. The result
is frequently
expressed in an average cost per cubic meter of water
(Figure 3).
fig3x126.gif (600x600)
It should be noted that the most economic option is strongly
affected by the size
of the project. In general, wind energy is seldom
competitive when mean winds
are less than 2.5 m/s, but it is the least cost alternative
for a wide range of
conditions when the mean wind speed is greater than 4.0 m/s.
11. Install the Machines
Once wind energy has been selected, arrangements should be
made for the
purchase or construction of the equipment. The site must be
prepared and the
materials all brought there. A crew for assembly and
erection must be secured,
and instructed. Someone must be in charge of overseeing the
installation to
ensure that it is done properly and to check the machine out
when it is up.
Regular maintenance must be arranged for.
With proper planning, organization, design, construction,
and maintenance, the
wind machines may have a very useful and productive life.
Source:
James F. Manwell, VITA Volunteer, University of
Massachusetts.
References:
Fraenkel, Peter. Water-Pumping Devices: A Handbook for Users
and Choosers.
London: Intermediate Technology Publications, 1986.
Johnson, Garry. Wind Energy Systems. Englewood Cliffs, New
Jersey: Prentice
Hall, Inc.
Lierop, W.E. and van Veldheizen, L.R. Wind Energy
Development in Kenya, Main
Report, Vol. 1: Past and Present Wind Energy Activities, SWD
82-3/Vol. 1
Amersfoort, The Netherlands: Consultancy for Wind Energy in
Developing Countries,
1982.
Lysen, E.H. Introduction to Wind Energy. SWD 82-1
Amersfoort, The Netherlands:
Consultancy for Wind Energy in Developing Countries, 1983.
Manwell, J.F. and Cromack, D.E. Understanding Wind Energy:
An Overview.
Arlington, Virginia: Volunteers in Technical Assistance,
1984.
McKenzie, D.W. "Improved and New Water Pumping
Windmills," Proceedings of
Winter Meeting, American Society of Agricultural Engineers,
New Orleans,
December, 1984.
Vilsteren, A.V. Aspects of Irrigation with Windmills.
Amersfoort, The Netherlands:
Consultancy for Wind Energy in Developing Countries, 1981.
Wegley, H.L., et al. A Siting Handbook for Small Wind Energy
Conversion Systems.
Richland, Washington: Battelle Memorial Institute, 1978.
Wyatt, A.S. and Hodgkin, J., A Performance Model for
Multiblade Water Pumping
Windmills. Arlington, Virginia: VITA, 1984.
Groups Involved with Wind Pumping in Developing Countries
Consultancy for Wind Energy in Developing Countries, P.O.
Box 85, 3800 AB,
Amersfoort, The Netherlands
Intermediate Technology Development Group, Ltd., 9 King
Street, Coven Garden,
London, WC2E 8HW, UK
IPAT, Technical University of Berlin, Sekr. TH2, Lentzallee
86, D-1000 Berlin 33,
West Germany
Renewable Energy Research Laboratory, Dept. of Mechanical
Engineering, University
of Massachusetts, Amherst, Massachusetts 01003, USA
SKAT, Varnbuelstr. 14, CH-9000 St. Gallen, Switzerland
The Danish Center for Renewable Energy, Asgaard, Sdr. Ydby,
DK-7760 Hurup
Thy, Denmark
Volunteers in Technical Assistance (VITA), 1815 N. Lynn
Street, Suite 200,
Arlington, Virginia 22209-2079 USA
Manufacturers of Water Pumping Windmills
Aermotor, P.O. Box 1364, Conway, Arkansas 72032, USA
Dempster Industries, Inc., Beatrice, Nebraska 68310, USA
Heller Aller Company, Perry & Oakwood St., Napoleon,
Ohio 43545, USA