TP# 37: 9/85
UNDERSTANDING
SOLAR STILLS
by
Horace McCracken
Joel Gordes
Technical Reviewers:
Daniel Dunham
Jacques Le Nonmand
Darrell G. Phippen
Published by:
VITA
1600 Wilson Boulevard, Suite 500
Arlington, Virginia 22209 USA
Tel: 703/276-1800 * Fax:
703/243-1865
Internet: pr-info@vita.org
PREFACE
This paper is one of a series published by Volunteers in
Technical
Assistance to provide an introduction to specific
state-of-the-art
technologies of interest to people in developing countries.
The papers are intended to be used as guidelines to help
people choose technologies that are suitable to their
situations.
They are not intended to provide construction or
implementation
details. People are
urged to contact VITA or a similar organization
for further information and technical assistance if they
find that a particular technology seems to meet their needs.
The papers in the series were written, reviewed, and
illustrated
almost entirely by VITA Volunteer technical experts on a
purely
voluntary basis.
Some 500 volunteers were involved in the production
of the first 100 titles issued, contributing approximately
5,000 hours of their time.
VITA staff included Maria Giannuzzi
as editor, Suzanne Brooks handling typesetting and layout,
and
Margaret Crouch as project manager.
The author of this paper, VITA Volunteer Horace McCracken,
is the
president of the McCracken Solar Company in Alturas,
California.
The co-author, VITA Volunteer Joel Gordes, is currently the
solar
design analyst for the State of Connecticut's Solar Mortgage
Subsidy Program. The
reviewers are also VITA volunteers.
Daniel
Dunham has done consulting in solar and alternative sources
of
energy for VITA and AID.
He has lived and worked in India, Pakistan,
and Morocco. Mr.
Dunham has also prepared a state-of-the-art
survey on solar stills for AID.
Jacques Le Normand is Assistant
Director at the Brace Research Institute, Quebec, Canada,
which does research in renewable energy.
He has supervised work
with solar collectors and has written several publications
on
solar and wind energy, and conservation.
Darrell G. Phippen is a
mechanical engineer and development specialist who works
with
Food for the Hungry in Scottsdale, Arizona.
VITA is a private, nonprofit organization that supports
people
working on technical problems in developing countries.
VITA offers
information and assistance aimed at helping individuals and
groups to select and implement technologies appropriate to
their
situations. VITA
maintains an international Inquiry Service, a
specialized documentation center, and a computerized roster
of
volunteer technical consultants; manages long-term field
projects;
and publishes a variety of technical manuals and papers.
For more information about VITA services in general, or the
technology presented in this paper, contact VITA at 1815
North
Lynn Street, Suite 200, Arlington, Virginia 22209 USA.
UNDERSTANDING SOLAR STILLS
by VITA
Volunteers Horace McCracken and Joel Gordes
I. INTRODUCTION
Ninety-seven percent of the earth's water mass lies in its
oceans. Of the
remaining 3 percent, 5/6 is brackish, leaving a
mere .5 percent as fresh water.
As a result, many people do not
have access to adequate and inexpensive supplies of potable
water. This leads to
population concentration around existing
water supplies, marginal health conditions, and a generally
low
standard of living.
Solar distillation uses the heat of the sun directly in a
simple
piece of equipment to purify water.
The equipment, commonly
called a solar still, consists primarily of a shallow basin
with
a transparent glass cover.
The sun heats the water in the basin,
causing evaporation.
Moisture rises, condenses on the cover and
runs down into a collection trough, leaving behind the
salts,
minerals, and most other impurities, including germs.
Although it can be rather expensive to build a solar still
that
is both effective and long-lasting, it can produce purified
water
at a reasonable cost if it is built, operated, and
maintained
properly.
This paper focuses mainly on small-scale basin-type solar
stills
as suppliers of potable water for families and other small
users.
Of all the solar still designs developed thus far, the
basin-type
continues to be the most economical.
HISTORY OF SOLAR DISTILLATION
Distillation has long been considered a way of making salt
water
drinkable and purifying water in remote locations.
As early as
the fourth century B.C., Aristotle described a method to
evaporate impure water and then condense it for potable use.
P.I. Cooper, in his efforts to document the development and
use
of solar stills, reports that Arabian alchemists were the
earliest known people to use solar distillation to produce
potable water in the sixteenth century.
But the first documented
reference for a device was made in 1742 by Nicolo Ghezzi of
Italy, although it is not known whether he went beyond the
conceptual stage and actually built it.
The first modern solar still was built in Las Salinas,
Chile, in
1872, by Charles Wilson.
It consisted of 64 water basins (a
total of 4,459 square meters) made of blackened wood with
sloping
glass covers. This
installation was used to supply water (20,000
liters per day) to animals working mining operations.
After this
area was opened to the outside by railroad, the installation
was
allowed to deteriorate but was still in operation as late as
1912--40 years after its initial construction.
This design has
formed the basis for the majority of stills built since that
time.
During the 1950s, interest in solar distillation was
revived, and
in virtually all cases, the objective was to develop large
centralized
distillation plants.
In California, the goal was to
develop plants capable of producing 1 million gallons, or
3,775
cubic meters of water per day.
However, after about 10 years,
researchers around the world concluded that large solar
distillation
plants were much too expensive to compete with fuel-fired
ones. So research
shifted to smaller solar distillation plants.
In the 1960s and 1970s, 38 plants were built in 14
countries,
with capacities ranging from a few hundred to around 30,000
liters of water per day.
Of these, about one third have since
been dismantled or abandoned due to materials failures.
None in
this size range are reported to have been built in the last
7
years.
Despite the growing discouragement over community-size
plants,
McCracken Solar Company in California continued its efforts
to
market solar stills for residential use.
Worldwide interest in
small residential-units is growing, and now that the price
of oil
is ten times what it was in the 1960s, interest in the
larger
units may be revived.
Although solar distillation at present cannot compete with
oil-fired
desalination in large central plants, it will surely become
a viable technology within the next 100 years, when oil
supplies
will have approached exhaustion.
When that day arrives, the
primary question will be, "Which method of solar
distillation is
best?"
Meanwhile, almost anyone hauling drinking water any
distance would be economically better off using a solar still.
NEEDS SERVED BY SOLAR DISTILLATION
Solar distillation could benefit developing countries in
several
ways:
o
Solar distillation can be a cost-effective
means of
providing
clean water for drinking, cooking, washing,
and bathing--four
basic human needs.
o
It can improve health standards by removing
impurities
from
questionable water supplies.
o
It can help extend the usage of existing
fresh water in
locations
where the quality or quantity of supply is
deteriorating. Where sea water
is available, it can
reduce a
developing country's dependence on rainfall.
o
Solar stills, operating on sea or brackish
water, can
ensure
supplies of water during a time of drought.
o
Solar distillation generally uses less
energy to purify
water than
other methods.
o
It can foster cottage industries, animal
husbandry, or
hydroponics
for food production in areas where such
activities
are now limited by inadequate supplies of
pure
water. Fishing could become important
on desert
seacoasts
where no drinking water is available for
fishermen.
o
Solar distillation will permit settlement in
sparsely-populated
locations,
thus relieving population
pressures in
urban areas.
APPLICATIONS
The energy from the sun used to distill water is free.
But the
cost of building a still makes the cost of the distilled
water
rather high, at least for large-scale uses such as
agriculture
and flushing away wastes in industry and homes.
Consequently,
the solar still is used principally to purify water for
drinking
and for some business, industry, laboratory, and green-house
applications. It
also appears able to purify polluted water.
Solar Distilled Water for Irrigation
For field agriculture, the solar still is not very
promising. It
takes about one meter depth of irrigation water per year to
produce crops in dry climates, whereas the solar still can
evaporate
about two meters' depth.
Thus, one square meter of solar
still would irrigate two square meters of land.
Unquestionably,
the cost of building the still would make water more
valuable
than the crops being produced.
This may not be true, however,
for agriculture in controlled environments, i.e.,
greenhouses. A
well-designed hydroponically-operated greenhouse should be
able
to produce 8 to 10 times as much food, per unit volume of
water
consumed, as field crops.
Recovery of Salt from a Solar Still
Since salt is a very cheap industrial material, and a solar
still
cannot produce anymore than an open pond, combining the
recovery
of salt with the distilling of water is not attractive
economically. Where
a family is using a solar still to provide
water valued at $1 per day, the amount of salt they need
might
cost them half a cent.
Recovery of Potable Water from Sewage
Although it seems possible that potable water can be
recovered
from sewage, if contaminants such as odorous gases are
present in
sewage water fed to the still, some portion of those gases
will
evaporate and condense with the distilled water.
In all
probability they could be filtered out with activated
carbon, but
to date, however, no one has had any experience with this.
Alcohol Production
If the "contaminant" is alcohol, it can be
separated from the
water. But it would
take two or three passes through the still
to attain a high enough concentration of alcohol to be used
as a
fuel. Considering
the current availability of fossil fuels,
producing alcohol in this way is not yet economical.
However,
when fossil fuel supplies run low and the price rises, solar
distillation could play a significant role.
Recovery of Distilled Water From Polluted Water Bodies
Whether or not solar distillation can actually purify
polluted
water is not yet known.
Laboratory tests have shown, however,
that a solar still can eliminate bacteria.
If after additional
research, a quantity of clean water can be recovered from
polluted water, this capability may become economically more
important than the purification of sea water.
It may also be
used to remove toxic substances such as pesticides.
Preliminary laboratory tests show that a modified version of
the
still--now commercially available--can do a very good job of
removing such substances from feed water.
Trichloroethylene
(TCE), for example, has been removed by a factor of 5,000 to
1;
ethylene dibromide (EDB) by 100 to 1; nitrates by 50 to 1;
and
others within those ranges.
Of course, more work must be done to
quantify these numbers, not to mention the unending list of
chemicals that need to be tested.
Elimination of Algae.
While algae will grow in some deep basin
stills where the water temperature seldom gets very high, in
the
shallow basin still it is usually killed by the high
temperature.
II. OPERATING
PRINCIPLES
GENERAL THEORY OF SOLAR DISTILLATION
Distillation operates by the escape of moving molecules from
the
water surface into the gases above it.
Sensible heat--the kind
you can measure with a thermometer--is caused by the
movement of
molecules, zig-zagging about constantly, except that they
are not
all moving at the same speed.
Add energy and they move faster,
and the fastest-moving ones may escape the surface to become
vapor.
It takes a lot of energy for water to vaporize.
While a certain
amount of energy is needed to raise the temperature of a
kilogram
of water from 0 [degrees] to 100 [degrees] Celsius (C), it
takes five and one-half
times that much to change it from water at 100 [degrees] C
to water vapor
at 100 [degrees] C.
Practically all this energy, however, is given back
when the water vapor condenses.
The salts and minerals do not evaporate along with the
water.
Ordinary table salt, for example, does not turn into vapor
until
it gets over 1400 [degrees] C, so it remains in the brine
when the water
evaporates. This is
the way we get fresh water in the clouds
from the oceans, by solar distillation.
All the fresh water on
earth has been solar distilled.
It is not necessary for the water to actually boil to bring
about
distillation.
Steaming it away gently does the same job as
boiling, except that in the solar still, it will usually
turn out
even more pure, because during boiling the breaking bubbles
may
contaminate the product water with tiny droplets of liquid
water
swept along with the vapor.
THE SOLAR DISTILLATION PROCESS
The solar distillation process is shown in Figure 1.
Solar
29p06.gif (486x486)
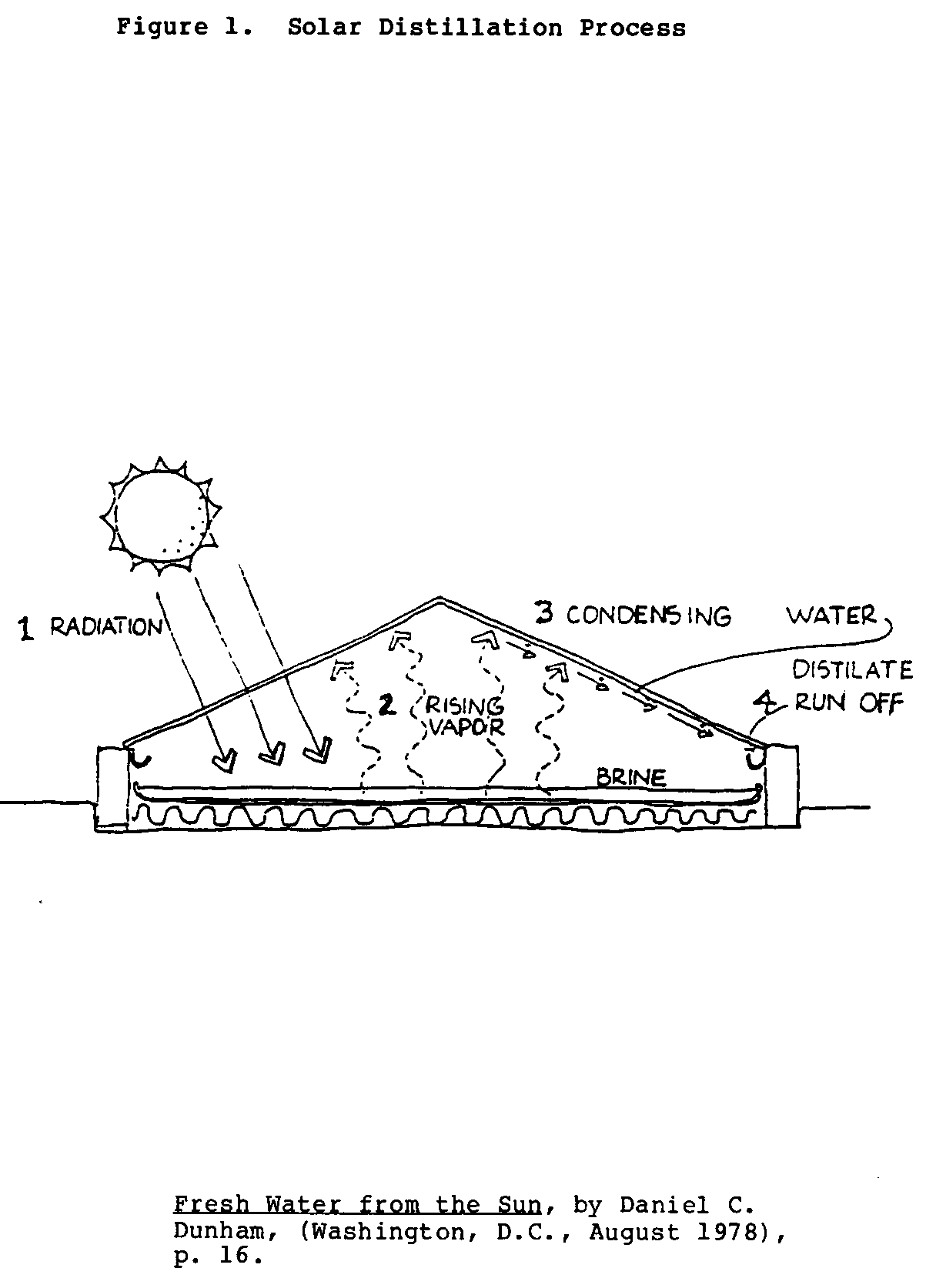
energy passing through a glass cover heats up the brine or
sea
water in a pan; this causes the water to vaporize.
The vapor
then rises and condenses on the underside of the cover and
runs
down into distillate troughs.
Fresh Water from the Sun, by Daniel C.
Dunham, (Washington, D.C., August 1978),
p. 16.
A more technical description follows.:
1.
The sun's energy in the form of short
electromagnetic
waves passes
through a clear glazing surface such as
glass.
Upon striking a darkened surface, this light
changes
wavelength, becoming long waves of heat which
is added to the water in a shallow basin
below the
glazing. As the water heats up,
it begins to evaporate.
2.
The warmed vapor rises to a cooler
area. Almost all
impurities
are left behind in the basin.
3.
The vapor condenses onto the underside of
the cooler
glazing and
accumulates into water droplets or sheets
of water.
4.
The combination of gravity and the tilted
glazing
surface
allows the water to run down the cover and into
a collection trough, where it is channeled
into
storage.
In most units, less than half the calories of radiant energy
falling on the still are used for the heat of vaporization
necessary
to produce the distilled water.
A commercial stills are
sold to date have had an efficiency range of 30 to 45
percent.
(The maximum efficiency is just over 60 percent.) Efficiency
is
calculated in the following manner:
Energy required for the vaporization
of the distillate that is recovered
Efficiency
= Energy in the sun's radiation
that falls on the still.
Providing the costs don't rise significantly, an efficiency
increase of a few percent is worth working for.
Improvements are
principally to be sought in materials and methods of
construction.
III. SOLAR STILL
DESIGN VARIATIONS
Although there are many designs for solar stills, and four
general categories, (concentrating collector stills;
multiple
tray tilted stills; tilted wick solar stills; and basin
stills)
95 percent of all functioning stills are of the basin type.
CONCENTRATING COLLECTOR STILL
A concentrating collector still, as shown in Figure 2, uses
29p08.gif (486x486)
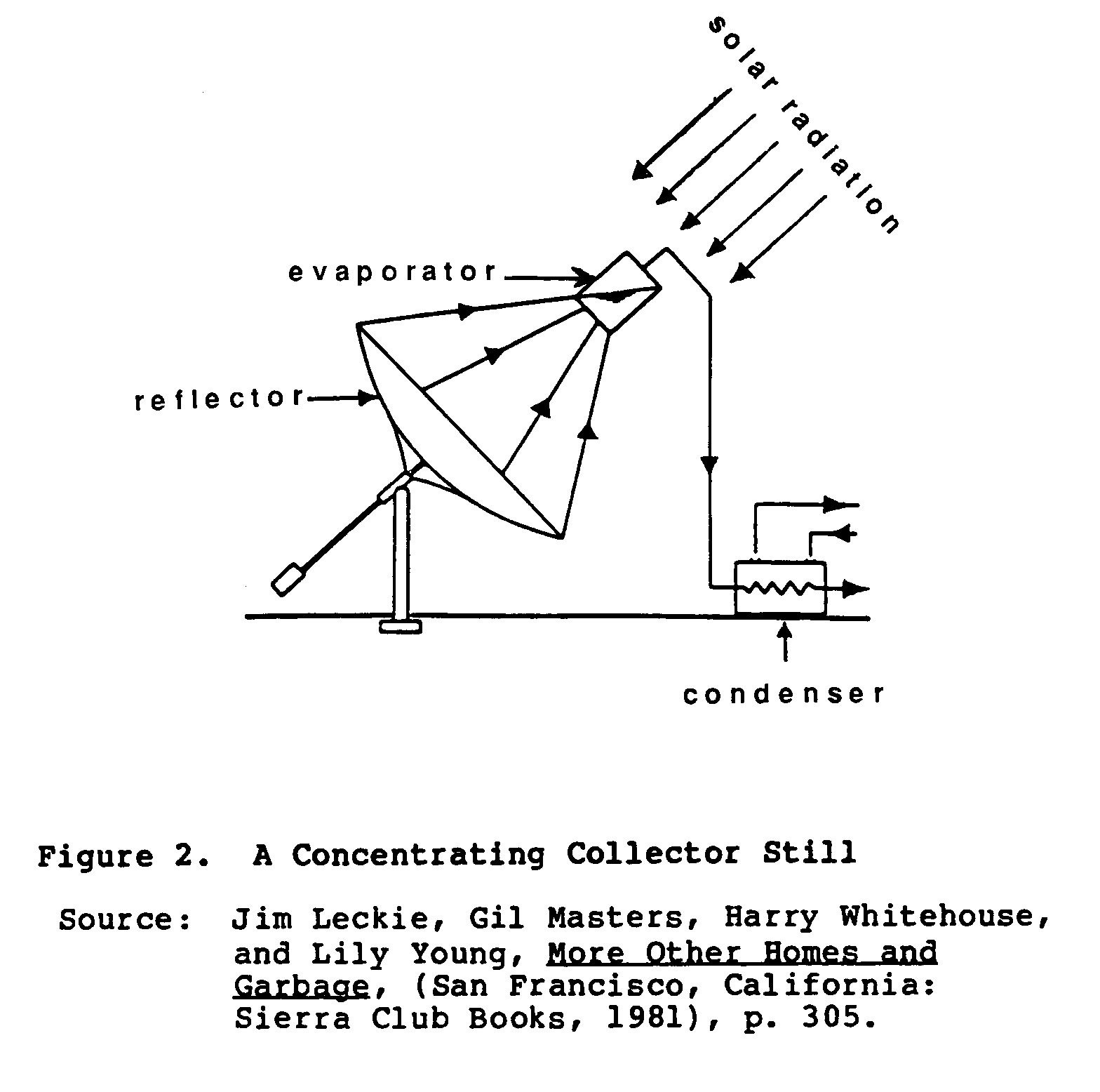
parabolic mirrors to focus sunlight onto an enclosed
evaporation
vessel. This
concentrated sunlight provides extremely high
temperatures which are used to evaporate the contaminated
water.
The vapor is transported to a separate chamber where it
condenses, and is transported to storage. This type of still
is
capable of producing from .5 to .6 gallons per day per
square
foot of reflector area.
This type of output far surpasses other
types of stills on a per square foot basis. Despite this
still's
outstanding performance, it has many drawbacks; including
the
high cost of building and maintaining it, the need for
strong,
direct sunlight, and its fragile nature.
MULTIPLE TRAY TILTED STILL
A multiple tray tilted still (Figure 3), consists of a
series of
29p09.gif (486x486)

shallow horizontal black trays enclosed in an insulated
container
with a transparent top glazing cover.
The vapor condenses onto
the cover and flows down to the collection channel for
eventual
storage.
This still can be used in higher latitudes because the whole
unit
can be tilted to allow the sun's rays to strike perpendicular
to
the glazing surface.
The tilt feature, however, is less important
at and near the equator where there is less change in the
sun's
position over the still.
Even though efficiencies of up to 50
percent have been measured, the practicality of this design
remains doubtful due to:
o
the complicated nature of construction
involving many
components;
o
increased cost for multiple trays and
mounting requirements.
TILTED WICK SOLAR STILL
A tilted wick solar still draws upon the capillary action of
fibers to distribute feed water over the entire surface of
the
wick in a thin layer.
The water is then exposed to sunlight.
(See Figure 4.)
29p10.gif (486x486)
A tilted wick solar still allows a higher temperature to
form on
this thin layer than can be expected from a larger body of
water.
This system is as efficient as the tilted tray design, but
its
use in the field remains questionable because of:
o
increased costs due to mounting requirements
and
essential
insulation;
o
the need to frequently clean the cloth wick
of built-up
sediments,
highlighting the need for an operable
glazing
cover;
o
the need to replace the black wick material
on a
regular basis
due to sun bleaching and physical
deterioration
by ultra-violet radiation;
o
uneven wetting of the wick which will result
in dry
spots,
leading to reduced efficiency; and
o
the unnecessary aspect of the tilt feature
except where
it is
required higher latitudes.
BASIN STILL
A basin still (See Figure 5), is the most common type in
use,
29p11.gif (540x540)
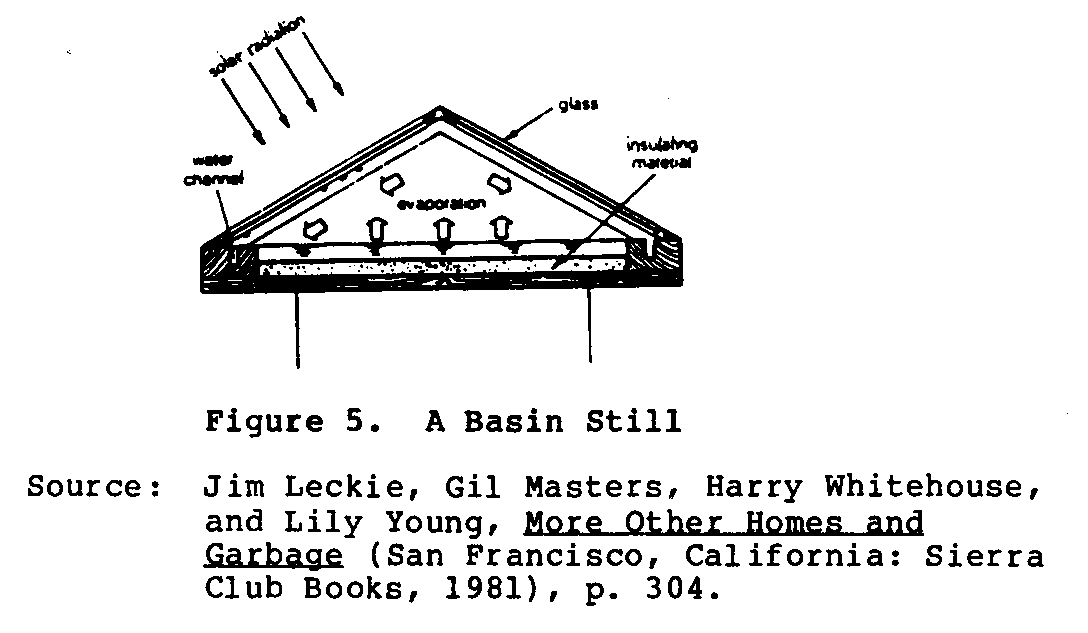
although not in current production.
While the basic design can take on many variations, the
actual
shape and concept have not changed substantially from the
days of
the Las Salinas, Chile stills built in 1872.
The greatest
changes have involved the use of new building materials,
which
may have the potential to lower overall costs while
providing an
acceptably long useful life and better performance.
All basin stills have four major components:
1.
a basin;
2.
a support structure;
3.
a transparent glazing cover; and
4.
a distillate trough (water channel).
In addition to these, ancillary components may include:
1.
insulation (usually under the basin);
2.
sealants;
3.
piping and valves;
4.
facilities for storage;
5.
an external cover to protect the other
components from
the weather
and to make the still esthetically
pleasing;
and
6.
a reflector to concentrate sunlight.
Physical Dimensions of the Basin Still
The actual dimensions of basin stills vary greatly,
depending on
the availability of materials, water requirements, ownership
patterns, and land location and availability.
If the only glazing available is one meter at its greatest
dimension, the still's maximum inner width will be just
under one
meter. And the
length of the still will be set according to what
is needed to provide the amount of square meters to produce
the
required amount of water.
Likewise, if an entire village were to
own and use the still, the total installation would have to
be
quite large.
It is generally best to design an installation with many
small
modular units to supply the water.
This allows:
o
units to be added;
o
manageable components to be handled by
unskilled
persons
without expensive mechanical equipment;
o
maintenance can be carried out on some units
while
others
continue to operate.
Most community size stills 1/2 to 21/2 meters wide, with
lengths
ranging up to around 100 meters.
Their lengths usually run along
an eastwest axis to maximize the transmission of sunlight
through
the equatorialfacing sloped glass.
Residential, appliance type
units generally use glass about 0.65 to 0.9 meter wide with
lengths ranging from two to three meters.
A water depth of 1.5
to 2.5 cm is most common.
The usual argument for greater depths is that the stored
heat
can be used at night to enhance production when the air
temperatures
are lower.
Unfortunately, no deep basin has ever attained
the 43 percent efficiency typical of a still of minimum
water
depth. The results
to date are clear: the shallower the
depth
the better. Of
course, if the basin is too shallow, it will dry
out and salts will be deposited, which is not good.
Note that
solar heat can evaporate about 0.5 cm of water on a clear
day in
summer. By setting
the initial charge at about 1.5 cm depth,
virtually all of the salts remain in the solution, and can
be
flushed out by the refilling operation.
MATERIAL REQUIREMENTS OF BASIN STILLS
The materials used for this type of still should have the
following
characteristics:
o Materials
should have a long life under exposed
conditions or
be inexpensive enough to be replaced upon
degradation.
o They should be
sturdy enough to resist wind damage and
slight earth
movements.
o They should be
nontoxic and not emit vapors or instill
an unpleasant
taste to the water under elevated temperatures.
o They should be
able to resist corrosion from saline
water and
distilled water.
o They should be
of a size and weight that can be
conveniently
packaged, and carried by local
transportation.
o They should be
easy to handle in the field.
Although local
materials should be used whenever possible to
lower initial costs
and to facilitate any necessary repairs, keep
in mind that solar
stills made with cheap, unsturdy materials
will not last as
long as those built with more costly, high-quality
material.
With this in mind, you must decide whether
you
want to build an
inexpensive and thus short-lived still that
needs to be replaced
or repaired every few years, or build
something more
durable and lasting in the hope that the distilled
water it produces
will be cheaper in the long run. Of the
low-cost
stills that have
been built around the world, many have been
abandoned.
Building a more durable still that will last
20 years
or more seems to be
worth the additional investment.
Choosing materials for the components in contact with the
water
represents a serious problem.
Many plastics will give off a
substance which can be tasted or smelled in the product
water,
for periods of anywhere from hours to years.
As a general guide,
if you are contemplating using any material other than glass
or
metal in contact with water, you may perform a useful
screening
test by boiling a sample of the material in a cup of good
water
for half an hour, then let the water cool, and smell and
taste
it. This is a
considerably accelerated test of what happens in
the still. If you
can tell any difference between the test water
and that you started with, the material is probably safe to
use.
To get some experience, try this on polyethylene tubing, PVC
pipe
and fiberglass resin panel.
Basic Components
A basin still consists of the following basic
components: (1) a
basin, (2) support structures, (3) glazing, (4) a distillate
trough, and (5) insulation.
The section that follows describes
these components, the range of materials available for their
construction, and the advantages and disadvantages of some
of
those materials.
The Basin. The basin
contains the saline (or brackish) water that
will undergo distillation.
As such, it must be waterproof and
dark (preferably black) so that it will better absorb the
sunlight and convert it to heat.
It should also have a
relatively smooth surface to make it easier to clean any
sediment
from it.
There are two general types of basins.
The first is made of a
material that maintains its own shape and provides the
waterproof
containment by itself or with the aid of a surface material
applied directly to it.
The second type uses one set of
materials (such as wood or brick) to define the basin's
shape.
Into this is placed a second material that easily conforms
to the
shape of the structural materials and serves as a waterproof
liner. No one
construction material is appropriate for all
circumstances or locations.
Table 1 lists the various materials
and rates them according to properties desirable for this
application.
Table 1.
A Comparison of
Various Materials Used
in Solar Basin Construction
Type of Dura-
Local Avail-
Skill
Port-
Toxi-
Material bility
Cost
ability Needed
Cleaning
ability city
Enameled High
High
Low Low
High
Medium Low
Steel
EPDM High
High
Low Low
High
High Low
Rubber
Butyl High
High
Low Low
High
High Low
Rubber
Asphalt High
Medium
Medium Medium
Medium
Medium [a]
Mat
Asbestos High
Medium
Low Medium
Medium
Medium High
Cement
Black Medium
Low Low
Low
Medium
High Low
Poly-
ethylene
Roofing Medium
Medium High
Medium Medium
Low
[a]
Asphalt
on
Concrete
Wood Low
[a]
[a] Medium
Medium
Medium Low
Formed Medium
Medium Low
Low
High
Medium Low
Fiber-
glass
[a] = Unknown or depends upon local conditions.
Selecting a suitable material for basin construction is the
biggest problem in the solar still industry.
The corrosion
conditions at the water line can be so severe that basins
made of
metal--even those coated with anti-corrosive materials--tend
to
corrode. Basins made
of copper, for example, are likely to be
eaten out in a few years.
Galvanized steel and anodized uncoated
aluminum are likely to corrode in a few months.
This is also
true of aluminum alloys used to make boats.
There are many
chemical reactions that double in rate with each 10
[degrees] centigrade
increase in temperature.
Whereas an aluminum boat might last 20
years in sea water at 25 [degrees] C if you increase that
temperature by
50 [degrees], the durability of that aluminum may well be
only one or two
years.
Porcelain-coated steel lasts only a few years before it is
eaten
out by corrosion.
The special glass used for porcelain is
slightly soluble in water, and inside a still it will
dissolve
away. The typical
life of stills equipped with porcelain basins
is about five years, although several have been kept
operating
much longer than that by repairing leaks with silicone
rubber.
People have also tried to use concrete because it's
inexpensive
and simple to work with, but the failure rate has been high
because it often develops cracks if not during the first
year,
then later on.
Concrete and abestoscement also absorb water.
The
water may not run right on through, but it does soak it up.
Everybody knows that satisfactory cisterns and reservoirs
are
built of concrete, but in a solar still the rules
change. Any
part of it that is exposed to outside air will permit
evaporation. Since
it is salt water that is being evaporated,
salt crystals will form in the concrete near the surface and
break it up, turning it to powder.
What about plastic?
Every few years, someone decides that if we
could just mold the whole still--except for the glass and
glass
seal--out of some plastic such as styrofoam, it would be so
easy
and inexpensive. But
styrene foam melts at about 70 [degrees] Centigrade.
Urethane foam is a little more promising, but it tends to be
dimensionally unstable, and, if a still is constructed in
the
inclined-tray configuration, the efficiency suffers, because
the
non-wetted portions do not conduct heat to the wetted
portions
very well.
What about fiberglass?
People have spent a lot of time trying to
build stills from fibreglass resin formulations.
Thus far, they
have found the material to be unusable for any part of the
still
(e.g., the basin or distillate trough) that comes in contact
with
water, either in liquid or vapor form.
Epoxy and polyester
resins can impart taste and odor to the distilled water, not
just
for weeks, but for years.
Researchers have found that this
problem cannot be eliminated by covering these materials
with a
coat of acrylic br anything else.
The odors migrate right
through the coating and make the distilled water unsalable,
if
not undrinkable.
Moreover, using fiberglass resin is not a
particularly low-cost approach.
Finally, a fiberglass basin or
trough that is subjected to hot water for many years
develops
cracks. Unless
researchers find a way to solve these problems,
fiberglass remains an unsuitable material.
One alternative is ordinary aluminum coated with silicone
rubber.
The durability of basins made with this material increased
into
the 10- to 15-year range.
For the hundreds of stills one company
sold using this material, the coating was all done by
hand. With
production roll coating equipment, the basin's durability
could
probably be increased even more.
Although stainless steel has been used, success has been
poor.
Support Structures.
Support structures form the sides of the
still as well as the basin, and support the glazing
cover. As
noted earlier, some materials used in forming the basin also
form
the still support structure while other still configurations
demand separate structures, especially to hold the glazing
cover.
The primary choices for support structures are wood, metal,
concrete, or plastics.
In most cases the choice of material is
based upon local availability.
Ideally, the frame for the
glazing cover should be built of small-sized members so they
do
not shade the basin excessively.
Wooden support structures are subject to warping, cracking,
rot,
and termite attack.
Choosing a high-quality wood, such as
Cypress, and letting it age may help to alleviate these
problems,
but, if high heat and high humidity prevail inside and
outside
the still, the still will require frequent repair or
replacement.
The main advantage of wood is that it can be easily worked
with
basic hand tools.
Metal may be used for the supports but is subject to
corrosion.
Since metals are not subject to warping, they can aid in
maintaining
the integrity of the seals, although the expansion rate
of a metal must be taken into account to ensure its
compatibility
with the glazing material and any sealants used.
Use of metal
for frame members is practically limited to aluminum and
galvanized
steel. Both will
last almost indefinitely, if protected
from exposure.
Silicone rubber will not adhere well to galvanized steel,
but
does so very well to aluminum.
Concrete and other masonry materials may form the sides and
glazing support of a still as well as the membrane.
This is more
readily possible in a single-slope still (Figure 6) rather
than
29p18a.gif (486x486)

in a double-slope still (Figure 7).
29p18b.gif (486x486)
Glazing Cover. After
the pan, the glazing cover is the most
critical component of any solar still.
It is mounted above the
basin and must be able to transmit a lot of light in the
visible
spectrum yet keep the heat generated by that light from
escaping
the basin. Exposure
to ultraviolet radiation requires a material
that can withstand the degradation effects or that is
inexpensive
enough to be replaced periodically.
Since it may encounter
temperatures approaching 95 [degrees] celsius (200 [degrees]
F), it must also be
able to support its weight at those temperatures and not
undergo
excessive expansion, which could destroy the airtight
seals. A
film type cover, which must be supported by tension or air
pressure, seems like a very poor choice.
Ideally, the glazing material should also be strong enough
to
resist high winds, rain, hail, and small earth movements,
and
prevent the intrusion of insects and animals.
Moreover, it must
be "wettable."
Wettability allows the condensing vapor to form
as sheets of water on the underside of a glazing cover
rather
than as water droplets.
If the water does form as droplets, it
will reduce the performance of the still for the following
reasons:
o
Water droplets restrict the amount of light
entering
the still
because they act as small mirrors and reflect
it back out.
o
A percentage of the distilled water that
forms as
droplets on
the underside will fall back into the basin
rather than
flow down the glazing cover into the
collection
trough. Except for temporary conditions
at
startup,
such a loss of water should not be tolerated.
Other factors determining the suitability of glazing
material
include the cost of the material, its weight, life
expectancy,
local availability, maximum temperature tolerance, and
impact
resistance, as well as its ability to transmit solar energy
and
infrared light.
Table 2 compares various glazing materials based
on these factors.
Of the glazing materials listed in Table 2, tempered glass
is the
best choice in terms of wettablity and its capability to
withstand high temperatures.
It is also three to five times
stronger than ordinary window glass and much safer to work
with.
One disadvantage of tempered glass is its high cost.
While
tempered low-iron glass, in one series of tests, gave 6
percent
additional production, it also added about 15 percent to the
cost
of the still.
Moreover, glass cannot be cut after it has been
tempered.
Nevertheless, it is a valid choice, certainly for a
top-quality, appliance type product.
Table 2.
A Comparison of Various Glazing Materials
Used in Building Solar Stills
Type
Estimated
Solar Infrared Light
Glazing
Cost(a)
Weight
Life Maximum
Transmittance
Transmittance
Impact
Local
Material
(Dollars/[Ft.sup.2])
(Lb/[Ft.sup.2]) Expectancy
Temperature
(Percent)
(Percent)
Resistance
Wettability Availability
Tempered Low-Iron
1.6 to
400 [degrees]-600 [degrees] F
Glass
3.60
2.5
50+ years
204 [degrees]-316 [degrees] C
91 less than 2
Low
Excellent No
Ordinary Window
400 [degrees] F
Glass
.95
1.23
50 years 204 [degrees]
C 86
2
Low
Excellent Yes
Tedlar
.60 .029
5-10 years
225 [degrees] F
107
[degrees] C 90
58
Low
Treatable No
Mylar
? ?
?
?
?
?
Low
Treatable No
Acrylic
1.50 .78
25+ years
200 [degrees] F
93 [degrees] C
89
6
Medium
Treatable No
Polycarbonate
2.00 .78
10-15 years
260 [degrees] F
127 [degrees]
C 86
6
High
Treatable No
Cellulose Acetate
180
[degrees] F
Butyrate
.68
.37
10 years 82 [degrees]
C 90
?
Medium
? No
Fiberglass
.78 .25
8-12 years
200 [degrees] F
93
[degrees] C 72-87
2-12
Medium
Treatable No
Polyethylene
.03 .023
8 months
160 [degrees] F
Possibly
71 [degrees] C
90 80
Low
treatable ?
(a) Costs are in
U.S. dollars, and were developed based on data published between 1981
and 1983.
Ordinary window glass is the next best choice, except that
it has
an oily film when it comes from the factory, and must be
cleaned
carefully with detergent and/or ammonia.
If you choose glass as
a glazing material, double-strength thickness (i.e.,
one-eighth
of an inch, or 32 millimeters) is satisfactory.
While some plastics are cheaper than either window glass or
tempered glass, they deteriorate under high temperatures and
have
poor wettability.
Moreover, under temperature conditions typical
of solar stills, the chemicals in plastics are likely to
interact
with the distilled water, possibly posing a health hazard.
What about the size of the glass?
Using a low slope of glass,
the goal is to make it as wide from north to south as
possible.
It doesn't take any more labor to install a 90 centimeter
piece
of glass than it does to install one of 60 centimeters and
you
get more absorber area.
Also, loss of heat through the walls
will be the same whether the still is large or small.
Using
pieces of glass wider than 90 centimeters (3 ft.) introduces
two
problems: (1) the
price per unit area of the glass goes up; and
(2) the labor costs and the danger of handling it
increase. On
the basis of experience, one optimal size is about 86
centimeters
(34"), a size that is commonly stocked and widely
available,
especially in the solar collector industry.
Distillate Trough.
The distillate trough is located at the base
of the tilted glazing.
It serves to collect the condensed water
and carry it to storage.
It should be as small as possible to
avoid shading the basin.
The materials used for the trough must satisfy the general
material requirements outlined previously.
Those most commonly
used include metal, formed materials used in basin
construction
(with or without plastic liners), or treated materials.
Stainless steel is the material of choice, although it is
expensive.
Common varieties, such as 316, are acceptable.
Other
metals require protective coatings to prevent
corrosion. Aluminum
is not supposed to corrode in distilled water, but it seems
preferable to rub a coating of silicone rubber over it
anyway.
Galvanized iron probably will not last more than a few years
at
most, and copper and brass should not be used because they
would
create a health hazard.
Also, steel coated with porcelain is a
poor choice because the glass will dissolve slowly and allow
the
steel to rust.
Basins lined with butyl rubber or EPDM can have their liners
extend beyond the basin to form the trough.
This method is
inexpensive to implement and provides a corrosion-free
channel.
No version of polyethylene is acceptable because it breaks
up and
emits an unpleasant odor and taste.
Some people have used
polyvinyl chloride (PVC) pipe, slit lengthwise.
However, it is
subject to significant distortion inside the still, can give
off
an undesirable gas, and is subject to becoming brittle when
exposed to sunlight and heat.
Butyl rubber should be okay, but
because it is black, the distillate trough becomes an
absorber and
re-evaporates some of the distilled water (a minor problem).
Ancillary Components
Ancillary components include insulation, sealants, piping,
valves, fixtures, pumps, and water storage facilities.
In
general, it is best to use locally available materials,
which are
easily replaceable.
Insulation.
Insulation, used to retard the flow of heat from a
solar still, increases the still's performance.
In most cases,
insulation is placed under the still basin since this is a
large
area susceptible to heat loss.
In stills where the depth of water in the basin is two
inches or
less, performance has been increased by as much as 14
percent,
but this gain decreases as the depth of the water in the
basin
increases. Increases
in performance resulting from the
installation of insulation materials are also less in those
locations where greater amounts of solar energy are
available.
The least expensive insulation option is to build a solar
still
on land that has dry soil and good drainage.
The use of sand
helps to minimize solar heat losses, and may also serve as a
heat
sink, which will return heat to the basin after the sun sets
and
prolong distillation process.
Insulation, which adds approximately 16 percent to
construction
costs, may be extruded styrofoam or polyurethane (Note:
polyurethane
in contact with soil will absorb moisture and lose much of
its insulation value.)
Sealants. Although
the sealant is not a major component of a
solar still, it is important for efficient operation.
It is used
to secure the cover to the frame (support structure), take
up any
difference in expansion and contraction between dissimilar
materials,
and keep the whole structure airtight.
Ideally, a good
sealant will meet all of the general material requirements
cited
earlier in this paper.
Realistically, however, it might be
necessary to use a sealant that is of lesser quality and has
a
shorter lifespan but that may be locally available at prices
more
affordable to people in developing countries.
One major drawback
of applying low-cost sealants to stills is the frequent
labor
input the stills require to keep them in serviceable
condition.
Sealing a solar still is more difficult than sealing a solar
water-heating panel on two counts:
(1) an imperfect seal could
cause a drop of rain water carrying micro-organisms to enter
the
still, which would contaminate the water; and (2) applying a
sealant that imparts a bad taste or odor to the distilled
water
will make it unpalatable.
Traditional sealants that are locally available include:
o
window putty (caulk and linseed oil);
o
asphalt caulking compound;
o
tar plastic;
o
black putty.
A wide variety of other caulks sealants is also
available. These
include latex, acrylic latex, butyl rubber and synthetic
rubbers,
polyethylene, polyurethane, silicone, and urethane
foam. Most of
these will be more costly than traditional varieties, but
they
may wear longer.
Of this group of sealants, molded silicone or EPDM, clamped
in
place, seems to be the most promising.
Silicone rubber sealant,
applied from a tube, is certainly a superior choice,
although
people have reported a few instances of degradation and seal
failure after 5 to 15 years when the seal was exposed to
sunlight.
Covering the sealant with a metal strip should extend its
life greatly.
Researchers are experimenting with an extruded
silicone seal, secured by compression.
One final note:
Remember a sealant that works well for windows
in a building does not assure that it will work in a solar
still,
due to higher temperatures, presence of moisture, and the
fact
that the water must be palatable and unpolluted.
Piping. Piping is
required to feed water into the still from the
supply source and from the still to the storage reservoir.
The
general material requirements cited earlier hold true for
this
component.
While stainless steel is preferred, polybutylene is a
satisfactory pipe material.
Black polyethylene has held up well
for at least 15 years as drain tubing.
Nylon tubing breaks up if
exposed to sunlight for 5 to 10 years.
PVC (polyvinyl chloride)
pipe is tolerable, although during the first few weeks of
still
operation it usually emits a gas, making the distilled water
taste bad. Ordinary
clear vinyl tubing is unacceptable.
There
is a "food grade" clear vinyl tubing that is
supposed to be
satisfactory for drinking water, but the sun's rays are
likely to
degrade it if it's used in a solar still.
Companies sell
drinking water and milk in high-density polyethylene
bottles, and
have had satisfactory results.
But put the same plastic bottle
filled with water in the sun, and the plastic will degrade,
imparting a bad taste to the water.
Few plastics can withstand
heat and sunlight.
Brass, galvanized steel, or copper may be
used in the feed system, but not in the product system.
One final note:
Although a solar still repeatedly subjected to
freezing will remain unharmed, drain tubes so exposed may
freeze
shut unless you make them extra large.
Feed tubes can easily be
arranged with drain-back provision to prevent bursting.
Fittings. Fittings
are connection devices that hold pipe
segments together.
If you put a solar still on the market with
instructions to consumers that connections be made
"finger tight
only", people could put a wrench on a connection,
loosen it, and
be faced with an expensive repair problem.
So, the options
include having tight control of installation personnel, or
doing
a thorough training job, or making the equipment rugged
enough to
withstand ordinary plumbing practice.
A solar still is fed on a batch basis for an hour or two
every
day. It is necessary
to admit some extra water each day, to
flush out the brine.
There is very little pressure available to
get the water to drain, so drainage cannot proceed
rapidly. To
prevent flooding, it's good practice to insure that the feed
rate
does not exceed this maximum drainage rate.
If one uses needle
valves thus to restrict the flow, such valves have been
found to
be unstable over the years, generally tending to plug up and
stop
the flow. It has
proven to be a satisfactory solution to this
problem--when feeding from city water pressure of typically
50
p.s.i.--to use a length of small diameter copper tubing,
such as
25 feet or more of 1/8 inch outside diameter, or 50 feet of
3/16
inch outside diameter tubing, to serve as a flow
restrictor. It
needs to have a screen ahead of it, such as an ordinary hose
filter washer, with 50 mesh or finer stainless steel screen,
to
prevent the inlet end from plugging.
Storage Reservoir.
In selecting materials for the storage reservoir,
two precautions should be noted.
1) Distilled water
is chemically aggressive, wanting to dissolve
a little of
practically anything, until it gets "satisfied,"
and then the
rate of chemical attack is greatly slowed.
What this number
is, in terms of parts per million of
different
substances, is not well documented, but the
practical consequences
are that some things, such as steel,
galvanized
steel, copper, brass, solder, and mortar, which
distilled water,
resulting in damage or destruction of the
tank component,
and quite possibly in contamination of the
water.
Stainless steel type 316) is a good
choice. Polypropylene
laboratory tanks
are okay but must not be exposed
to
sunlight. Butyl rubber lining of some
structural
framework should
be okay. Galvanized steel would last
for
only a few
years, adding some zinc and iron to the water.
Concrete should
serve, again with the expectation that the
concrete will
slowly crumble over many years' time.
The
tiny amount of
calcium carbonate that is leached out can be
used by the body
in the diet. In fact, one way to
prevent
such chemical
attack is to introduce some limestone or
marble chips
into the distilled water stream, or in the
reservoir
itself, to pick up some calcium carbonate on
purpose, thus
greatly slowing the attack on the tank itself.
2) Extreme
precautions need to be taken to prevent entry of
insects and
airborne bacteria. Air must leave the
reservoir
every time water
enters it, and must re-enter every time
water is drawn
off. Use a fine mesh--50 x 50 wires to
the
inch--or finer
screen covering the vent, and turn the opening
of the
vent/screen assembly downward, to prevent entry
of rain
water. If this is ignored for even one
hour, an
insect can get
in, and you have germ soup from then on.
Storage capacity should be adequate to contain four to five
times
the average daily output of the still.
Factors to Consider in Selecting Materials for Basin Still
Let us review the functions of the basin:
o
It must contain water without leaking.
o
It must absorb solar energy.
o
It must be structurally supported to hold
the water.
o
It must be insulated against heat loss
from the bottom
and edges.
An infinite number of combinations of materials will serve
those
functions. The
membrane that holds water, for example, may be
stiff enough to support the water, but it doesn't have to
be.
The basin may be rigid enough to support the glass, but it
doesn't have to be.
In short, a component need not satisfy two
functions at the same time.
Indeed, it is usually better to
select local material that will best do each job separately,
and
then put them together.
But if you can find a material that does
a couple of jobs well, so much the better.
In selecting materials for a solar still, there are almost
always
tradeoffs. You can
save money on materials, but you may lose so
much in productivity or durability that the
"saving" is poor
economy.
Summary of Materials Recommended for Basin Still
Construction
Where the objective is the lowest cost of water on a 20-year
life
cycle cost basis, the best materials for building a basin
still
are:
o
silicone compound coating to blacken the
bottom of the
basin;
o
metal ribs spaced 40 centimeters (16
inches) apart to
support the
underside of the basin;
o
about 25 to 38 millimeters of insulation
between the
ribs (this
may be high-temperature urethane foam, or
fiberglass);
o
a bottom covering of lightweight galvanized
steel, or
aluminum
sheet (note: if you plan to put the
still on
the ground
and use an insulation that is impervious to
water, no
bottom sheet is needed);
o
metal siding, such as extruded aluminum, to
support the
still
(note: extruded aluminum can be
assembled
quickly, but
it is expensive; thus, you may prefer a
lower cost
material such as painted steel or aluminum;
o
a stainless steel trough;
o
tempered low-iron glass, or regular
double-strength
window
glass. (If using patterned glass, put
the
pattern side
down);
o
extruded gaskets, compressed into final
position;
o
type 316 stainless steel fittings
(note: brass is not
acceptable;
PVC is acceptable, but poor in very hot
climates);
o
a mirror behind the still for higher
latitudes.
Although these materials are representative of a high-cost
still
design, they are probably a good investment since none of
the
inexpensive designs has stayed on the market.
However, we must
also ask the question, "Expensive compared to
what?" Compared to
hauling purified water in bottles or tanks, solar distilled
water
would almost always be much less expensive.
Compared to hauling
vegetables by airplane to hot desert places, using a solar
still
to raise vegetables in a greenhouse should be less
expensive.
Compared to the cost of boiling water to sterilize it, the
solar
still should be competitive in many situations.
And although the
materials used in building a high-cost still will probably
always
be expensive, mass production could ultimately drive down
the
unit cost per still.
IV. OPERATION AND
MAINTENANCE OF SOLAR STILLS
OPERATING REQUIREMENTS OF BASIC STILLS
Protecting Distilled Water from Contamination
Protecting a solar still against the entry of insects and
polluted
rainwater is important.
After your still is installed, you
must:
o
disinfect the interior of the still and
tubing with
chlorine
compounds (adding a few spoonfuls of laundry
bleach to a
few liters of water does the job nicely);
and
o
provide a vent(*) in the feed tube at the
still, screened
with fine
stainless steel screen filter washer in a
pipe
fitting, turned downward to prevent entry of
contaminated
rainwater. If these precautions are not
taken,
flying insects, attracted by the moisture, might
find their
way in and die in the distillate trough.
Preventing contamination in a storage reservoir is a little
more
difficult, as the daily high temperature are not available
to
pasteurize the water.
Nevertheless, with diligent attention to
detail, the system can be used for decades without
contamination.
Filling and Cleaning a Basin Still
Filling a basin still is a batch process (*), done once a
day, at
night or in the morning.
With a still of this design, about 5 to
7 percent of the day's total distilled water is produced
after
sundown, so it is important to wait until the still is cold.
Refilling it between three hours or more after sundown and
up to
one or two hours after sunrise will cause little, if any,
loss of
production.
(*) A vent allows air to enter and exit the still daily
during the
operation and refilling.
It is not necessary to drain the still completely.
Refilling it
with at least twice as much as it produces will normally
dilute
and flush it adequately.
Three times as much would keep it a
little cleaner, and could be worth doing, provided the cost
of
feed water is nominal.
A rapid mechanical flushing is not
required; a gentle trickle does the job.
Feeding Hot Water to a Basin Still
If a basin still is fed water that is hotter than the ambient
air, the unit becomes a conventional distiller, except that
it
uses glass instead of copper as the condenser.
If the hot water
is virtually cost-free, as is geothermal or waste water, it
can
be well worth doing.
If the feed water is heated by fossil fuels
or by separate solar panels, the economics look doubtful,
and the
feed line tends to plug up with scale.
FACTORS INFLUENCING SOLAR STILL OPERATING PERFORMANCE
In this section, we discuss some important factors that
influence
the rate of production of distilled water.
These include
climatic factors, thermal loss factors, and solar still
design
factors.
Climate Factors
Radiation: Its
Effect on Efficiency. The amount of
solar radiation
a solar still receives is the single most important factor
affecting its performance.
The greater the amount of energy
received, the greater will be the quantity of water
distilled.
Figure 8 shows the rate of production of a basin still on
the
29p38a.gif (534x534)
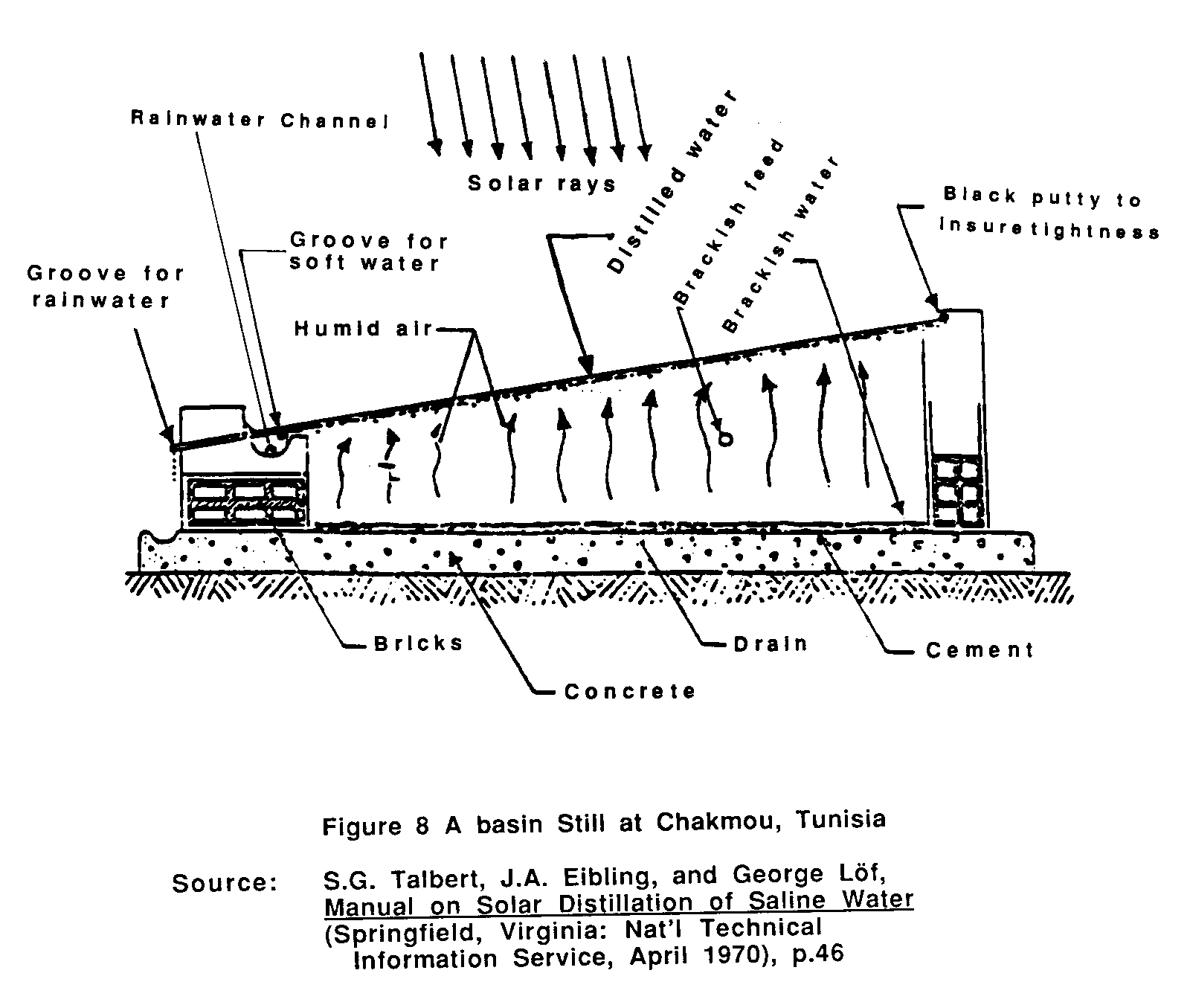
basis of specific solar inputs.
Solar stills produce less distilled water in winter than in
summer, which is a problem.
To some extent, the demand for
drinking water also varies with the seasons, by as much as
perhaps
2 to 1, summer over winter.
But the annual sunlight
variation affecting a still's solar distillation rate is
greater
than that, at least in regions well outside the
tropics. In the
tropics, at latitudes of less than 20 [degrees], the annual
sunlight
variation is probably well under 2 to 1, so it may not be a
problem there. The
farther away from the equator, the greater
the annual sunlight variation, to perhaps 7 to 1 at 40
[degrees]
latitudes. This is
unacceptable, making use of a solar still
difficult in winter at high latitudes.
(*) Note that there are other methods available for large
distillation plants.
However, because they fall outside the
scope of this paper, they are not discussed here.
Many approaches have been tried to solve this problem.
Tilting
the whole still up to more or less an equatorial mount
brings the
ratio down very nicely.
This is called the "inclined-tray"
still, and is accomplished by using many small pans in a
stair-step
arrangement. With
this arrangement, total sunlight
striking the aperture of the glass remains more constant,
and the
light which glances off the water of one small tray warms
the
bottom of the one above it, improving performance.
While this is
a substantial advantage, it is the only advantage of this
design,
and it must be weighed against the disadvantages of higher
costs
associated with putting many small pans vs. only one in the
enclosure, and, most probably, higher installation costs due
to
holding the end of the pan higher off the supporting
surface, and
protecting it against wind loads.
In latitudes perhaps 20 [degrees] on
up, it seems possible that the inclined-tray will find a
place in
the market.
Using an inclined-tray still is only one solution to the
problem
of annual variation in higher latitudes.
Some other steps that
can be taken include:
o
buying an extra large still that produces enough
distilled
water in winter, resulting in a likelihood
that you
will have more water than you need in summer;
o
using less water in winter and/or using
some tap water;
o
buying supplemental water in winter; or
o
saving some of the excess distilled water
made in
summer or
fall for use in winter;
o
installing a mirror behind the basin to
reflect
additional
sunlight back into the still in winter.
To
reflect
back as much light as possible, use a
reflective
surface of about one-third to one-half of
the
aperture of the glass cover, tilted forward 10 [degrees]
from the
vertical, mounted at the rear edge of the
still.
In latitudes between 30 [degrees] and 40
[degrees], this gives
from 75 to
100 percent more yield in mid-winter.
Condensing-Surface Temperature.
Much work has been done to try
to obtain lower condensing temperatures, thereby increasing
the
temperature difference between the heated feed water and the
condensing surface.
This approach undoubtedly derives from 100
years of steam power engineering, in which it is most
important
to get the steam temperature high and the condensing
temperature
low to gain efficiency.
But this principle does not hold true
for a solar still.
Steam for power is pure steam, whereas the
contents of a solar still are both air and water vapor.
It has
been demonstrated repeatedly that the higher the operating
temperature of the still--insolation being equal--the higher
the
efficiency. For each
6 [degrees] celsius (10 [degrees] F) increase in ambient
temperature, the production of a still increases by 7 to 8
percent.
The practical effect of this is that a still operating in
a hot desert climate will produce typically as much as
one-third
more water than the same unit in a cooler climate.
(By the same token, cooling the glazing cover of a solar
still by
spraying water on it or blowing air over it does not help
the
still produce more distillate.
In an experiment at the
University of California in the United States, two identical
stills were built.
The glazing cover of the first still was fan-cooled;
the cover of the second still was not.
Of the two
stills, the cooled unit produced significantly less
distillate.
Consequently, it's better to put the still in a protected
area
rather than a windy area.)
Thermal Loss Factors
Production is also associated with the thermal efficiency of
the
still itself. This
efficiency may range from 30 to 60 percent,
depending on still construction, ambient temperatures, wind
velocity, and solar energy availability.
Thermal losses for a
typical still vary by season, as shown in Table 5.
Table 5.
Distribution of Incoming Solar Radiation
in the Distillation Process
December
May
Thermal Loss Factors
(Percent)
(Percent)
Reflection by Glass
11.8
11.8
Absorption by Glass
4.1
4.4
Radiative Loss from
Water
36.0 16.9
Internal Air Circulation
13.6
8.4
Ground and Edge Loss
2.1
3.5
Re-Evaporation and Shading
7.9
14.5
[Remainder of Energy Used to Distill Water]
24.5
40.5
Direct Use of the Sun's Energy, Daniels, Farrington, 1964,
Ballantine Books, page 124.
Solar Still Design Factors
Slope of the Transparent Cover.
The angle at which the transparent
cover is set influences the amount of solar radiation
entering a solar still.
When sunlight strikes glass straight on,
at 90 [degrees] to the surface, about 90 percent of the
light passes
through. Tip the
glass a little, so that it strikes at a "grazing
angle" of 80 [degrees], and only a few percent is
lost. But tilt it
a few more tens of [degrees], and the curve goes over the
hill, dropping
off to practically zero at 20 [degrees] grazing angle, where
virtually no
direct light gets through.
In a greenhouse-type still, for a
large part of the year the half of the glass that is facing
away
from the equator is receiving sunlight at very low grazing
angles.
It is actually shadowing the back one-third of the still.
It is more efficient to make that half of the glass facing
the
equator as long as possible, and put a more or less
reflective
back wall to the rear.
This was one of the significant steps
that has increased the efficiency of basin stills from 31 to
about 43 percent, using a single slope of glass.
And it costs
less to build.
The slope of the glass cover does not affect the rate at
which
the distillate runs down its inner surface to the collection
trough. A common
misconception was that the glass cover must be
tilted to get the water to run off.
This may have arisen from
the fact that ordinary window glass, as it comes from the
factory, has a minute oily film on it.
But if the glass is
clean, the water itself will form filmwise condensation on
it,
and will be able to run off at a slope as little as 1
[degrees].
There are three reasons why it is best to use as low a slope
as
possible: (1) the
higher the slope, the more glass and supporting
materials are needed to cover a given area of the basin; (2)
the higher slope increases the volume and weight [of the
still]
and therefore shipping costs; and (3) setting the glass at a
high
slope increases the volume of air inside the still, which
lowers
the efficiency of the system.
A glass cover that is no more
than 5 to 7 centimeters from the water surface will allow
the
still to operate efficiently.
Conversely, as glass-to-water
distance increases, heat loss due to convection becomes
greater,
causing the still's efficiency to drop.
Some important stills have been built following the
low-slope
design concept for the glass cover, yet using a short,
steeply
sloping piece of glass at the rear.
This requires either providing
an extra collection trough at the rear, or else making the
successive troughs touching heel and toe, so that it is
exceedingly difficult to get out in the middle of the array
to
service anything. It
also increases the condensing surface relative
to the absorber, which reduces operating temperatures in the
still, and is clearly disadvantageous.
A reflective and
insulated back may be preferable to glass.
Some years ago at the University of California, researchers
built
an experimental multiple tray tilted still with an average
glass-to-water
distance of about 30 millimeters, showing an efficiency
of 62 percent, one of the highest ever recorded.
The loss of
efficiency is greatest the first centimeter, rather less the
second cm, and so on, tailing off to smaller rates of loss
per cm
distance as far as the test was carried.
This is one of the
principle reasons a high slope of glass is to be avoided.
In sum, it is clear that a solar still should be built in a
way
that will get the water as hot as possible, and keep it as
close
to the glass as possible.
This is achieved by keeping the glass
cover at a minimum distance from the water surface, which in
practical terms, falls between 5 and 7 cm., and by
minimizing the
depth of water in the pan, to about 1.5 cm.
Wicks and Related Techniques
Researchers have tried to improve the efficiency of a solar
still
by enhancing its surface evaporation area using wicks.
In a
side-by-side test of two identical stills at the University
of
California, using a floating black synthetic fabric in one
still
and nothing in the other, the difference in production
between
the stills was indistinguishable, though similar tests have
reported some improvement.
It seems exceedingly difficult to
find a wick material that will last for 20 years in hot
saline
water, and that will not get crusted up with salts over a
period
of time. As for
putting dye in the water, studies suggest that
the slight improvement in performance does not justify the
increased cost and maintenance and operating problems
associated
with this technique.
Putting dark-colored rocks in the feedwater to store heat
for use
after nightfall has
been reported by Zaki and his associates to
improve performance by 40 percent, but he does not give the
reference point from which this is measured.
If he was comparing
one still containing 4 cm. of water with another same water
depth
but containing black stones, the productivity would increase
somewhat due to the decrease in thermal mass and resulting
increase
in operating temperature.
Reducing the initial water
depth might have accomplished the same result.
For this reason,
placing dark-colored rocks in the feedwater does not appear
to be
a promising technique for improvements in solar still
performance.
MAINTENANCE REQUIREMENTS OF BASIN STILLS
Ways of Handling the Buildup of Mineral Deposits
It is inevitable that some minerals are deposited on the
bottom
of the basin. In
most situations, including sea water and city
tap water, the amount deposited is so small that it creates
no
problem for decades.
One still in particular has been operated
for 20 years without ever having been opened or
cleaned. As long
as there is not an excessive buildup of deposits, indicated
by
formation of a dried-out island in the afternoon, they
create no
problem. Such
mineral deposits become the normal absorber.
An
accumulation of these deposits changes the interior surface
of a
basin from its original black color to a dark earth brown,
reflecting some sunlight, causing a 10 percent drop in still
production. To
offset this reduction, simply make the still 10
percent larger than it would need to be if it were cleaned
out
periodically.
Some desert waters high in alkalis will deposit a whitish
gray
scale on the bottom and sides of a basin.
In fact, almost any
feed water will do so, especially if the basin is allowed to
dry
out. In some cases,
the alkaline water may form a crust of scale
which is held on the water's surface by air bubbles that are
discharged when the feed water is heated.
Light-colored deposits
such as these may reduce production of the still by 50
percent or
more. Those that
settle to the bottom of the basin can be easily
coated black by mixing one tablespoon of black iron oxide
concrete coloring powder with about 10 or 15 liters of water
and
adding the solution to the still by means of a funnel
connected
to the feed water pipe.
This blackening agent is inert, and
imparts no bad taste or odor to the distilled water.
After the
solution reaches the basin through the feed water pipe, it
settles on the bottom of the basin and restores it to its
original
black color. Some
owners do this each fall, when production
begins to drop. Cost
is only pennies per application.
Deposits that float on the surface of the water in a basin
are a
tougher problem and one that requires more research.
An
Australian solar still expert suggests agitating the
contents of
the still by recirculating, or stirring, the water in the
pan for
one hour each night, to minimize the buildup of floating
deposits. Adding a
pint or two of hydrochloric (swimming pool)
acid to the still whenever the bottom becomes
grayish-white--every
year or two, maybe oftener in some cases--is a satisfactory
way of removing practically all of the scale.
Accumulation of Dust on the Glazing Cover:
What to Do
In the vast majority of stills, dust accumulates on the
glass
cover. But it does
not keep building up; it's held more or less
constant by the action of rain and dew.
This "normal"
accumulation causes production to drop from 5 to 15
percent. To
offset this, simply make your still 10 percent larger than
it
would need to be if kept clean.
However, if the still is in an
unusually dusty area, or if it is large enough that a
caretaker
is available at modest cost, cleaning the glazing cover is
justified. Ten
percent of 10,000 liters per day may be enough
to justify cleaning the cover once a month in the dry
season.
Repair and Replacement of Basin Still Components
As with all devices, the components of a basin still may
need to
be repaired or replaced from time to time.
The frequency depends
on the type of material used to construct the still.
One built
with premium materials will require almost no maintenance,
but
will entail a higher capital cost because many of the
materials
must be imported materials.
Use of cheaper materials subject to
degradation will almost certainly lower the initial cost,
but
will increase the amount of maintenance.
Even so, if the long-term
cost of maintenance and the lower initial cost are less than
the higher initial cost for premium materials, this may
present a
better option, especially if cost of capital is high.
This is
called "life cycle cost analysis," and it is
strongly recommended.
SKILLS REQUIRED TO BUILD, OPERATE, AND MAINTAIN A BASIC
STILL
Craftmanship and attention to detail in construction are
important for an efficient, cost-effective still.
In addition, supervisory personnel must be on hand who know
how
to size stills to meet a community's water supply needs; who
know
how to orient stills; who are familiar with required
construction
techniques; and who have the ability to train others in the
construction, operation and maintenance of stills.
Finally, it is important to ask local workers to participate
in
the planning and construction phases of a solar still
project to
get the indigenous population to accept the technology.
A sense
of pride in the building of the project may well mean the
difference
between long-term success or failure of the project.
COST/ECONOMICS
The cost and economics of solar stills depend on many
variables,
including:
o
cost of water produced or obtained by
competing
technologies;
o
water requirements;
o
availability of sunlight;
o
cost of locally-available materials;
o
cost of local labor;
o
cost of imported materials; and
o
loan availability and interest rates.
Table 6 shows the variation in costs for stills built in the
1970s in the Philippines, India, Pakistan, and Niger.
Note that
stills built in Niger in 1977 cost twice as much as those
built
in the Philippines in the same year, reflecting the wide
variation in local cost.
Table 6.
Variation in Costs for Stills Built in the
1970s
Location
Year Built
(Dollars/Square Foot)
Philippines
1977
$3.56
India
1975
1.39
Pakistan
1973
1.37
Niger
1977
6.30
(Costs today are undoubtedly higher.)
WHY BUY A STILL?--It saves money.
A solar still must operate with extremely low costs for
maintenance arid operation.
Over a long period according to a
study by George Lof, it is valid to assume that 85 percent
of the
cost of water from the still will be chargeable to the costs
of
buying it; the remainder to operation and maintenance.
It is easy to calculate the return on investment in a solar
still. Say you have
one that produces a daily amount of water
that would cost you $1 to buy in bottles:
then that still
returns you $365 per year.
If the still had cost you $365, then
it paid for itself in one year; if five times that much,
then
five years, etc.--not counting interest.
Cost of feeding water
into it is pretty small, but will increase the payout period
a
little also. In the
United States, the payout period tends to
run between two and five years, depending on the still's
size and
features.
SPECIAL DESIGN VARIATIONS
The majority of information presented thus far has centered
on
the basin-type solar still because it is the easiest to
construct
and may use a wide range of materials, making it adaptable
to
different locales.
But variations of the basin still are
possible, such as the double-slope and single-slope stills
depicted earlier in this paper.
In addition to these options,
there are other ways to design the still to increase its
efficiency or potential to produce potable water.
Some of these
are discussed below.
Basin Stills Equipped with Reflectors
Some stills have been equipped with reflective materials
which
have the potential to increase the amount of sunlight
falling on
the still without having to increase the area of the
still. At
latitudes in the thirties, performance increases in winter
of
100% have been achieved with a mirror of less than 1/2 the
area
of the glass. In the
tropics, of course, this function is not
required. A second
question arises about using mirrors to
enhance production year round.
This becomes a focusing collector,
which introduces substantial additional costs and
problems. If the
mirror assembly is cheaper than the pan
assembly, then it deserves to be looked at further, but it
is not
attractive at this time.
Tentatively, reflective aluminum sheet
has the most advantages.
Basin Stills Equipped with Insulated Glazing Covers
Another innovation is the use of an insulated glazing cover
to
be put over the glazing at night or during extremely cold
weather. This cuts
heat losses, allowing distillation to
continue longer, and retains heat overnight, causing
production
to start earlier the next day.
Cost-benefit analysis of this
approach has not been made.
V. COMPARING THE
ALTERNATIVES
For a couple of gallons of purified water a day, there is no
method that can compete with solar distillation. For a
couple of
million gallons a day--AS LONG AS WE ARE WILLING TO BURN UP
OUR
INHERITANCE OF FOSSIL CHEMICAL BUILDING BLOCKS JUST TO
EVAPORATE
WATER--boiling distillation is the cheapest way to purify
sea
water.
In sum, solar stills have:
o
high initial costs;
o
the potential to use local materials;
o
the potential to use local labor for
construction and
maintenance;
o
low maintenance costs (ideally);
o
no energy costs (not subject to fuel supply
interruptions);
o
few environmental penalties; and
o
in residential sizes, no subsequent costs
for
delivering
water to the end user.
Most competing technologies are:
o
low in initial costs;
o
dependent on economy of scale;
o
high in operating and maintenance-costs;
o
high in energy input costs;
o
low in local job creation potential;
o
vulnerable to changes in energy supply and
costs; and
<Figure 9>
29p38b.gif (594x594)
29p39.gif (600x600)
29p40.gif (600x600)
<Figure 10>
<Figure 11>
VI. CHOOSING THE TECHNOLOGY RIGHT FOR YOU
FACTORS TO CONSIDER
Solar energy is an excellent choice for water distillation
in
those areas of the Third World that meet the following
conditions:
o
expensive fresh water source (US) $1 or
more per 1,000
gallons);
o
adequate solar energy; and
o
available low-quality water for
distillation.
Other conditions suitability for solar stills are:
o
competing technologies that require
expensive
conventional wood, or petroleum fuels;
o
isolated communities that may not have
access to clean
water
supplies;
o
limited technical manpower for operation
and maintenance
of
equipment;
o
areas lacking a water distribution system;
and
o
the availability of low-cost construction
workers.
The greater the number of these conditions present, the more
solar stills are likely to be a viable alternative.
If the cost
of the water produced by a still over its useful life is
less
than by alternate methods, it is economical to pursue.
Other factors to consider are the availability and cost of
capital, as well as the local tax structure, which may allow
tax
credits and depreciation allowances as a means to recover a
portion of the cost.
This has proved to be a major incentive in
the United States.
Finally, the acceptance of solar distillation will depend
greatly
on how well one understands and handles the many social
issues
and cultural constraints that can hamper the introduction of
new
technologies. Some
of the more important issues that may affect
the acceptance of solar distillation are outlined below.
o
Stills built for village use require
community
cooperation
that may be foreign to some cultural
groups. If the distilled water
is incorrectly
distributed, causing a family unit not to receive its
fair share
of water, this could become a source of
conflict. For this reason, a
family-sized solar still
unit, which
a household has complete control over, may
be more
practical than a unit that serves an entire
village.
o
Potential users who think they will find
distilled
water
tasteless or not in keeping with what they are
accustomed
to may become disappointed and possibly
abandon
altogether the thought of drinking the water.
The problem
of taste must be dealt with early on so as
not to give
people a reason to respond negatively to
the
technology as a whole.
o
In some societies, conflicts may arise
over whether it
is the
responsibility of the man or the woman of the
household to operate the solar still.
Not dealing with
this issue
early on could result in the household's
total
rejection of the technology.
o
If solar distillation is perceived to be a
threat to a
community's
traditional lifestyle, the community may
reject the
technology. Such concerns can be headed
off
if the
technology is designed appropriately from the
start and
introduced at the proper time.
Moreover, a
community
is more likely to accept the technology if it
recognizes
the importance of clean water and considers
it a
priority to the degree that it is willing to
change
certain aspects of its lifestyle.
MARKET POTENTIAL
Three potential markets exist for solar stills.
First, a solar
still can be economically attractive almost any place in the
world where water is hauled and where a source of water is
available to feed the still.
Second, many people who boil their water to kill germs could
use
a solar still for the same purpose.
It will take more work to
demonstrate this function adequately, but early tests have
made
it seem highly promising.
A third market is in arid regions, whose untapped water
resources
may be sufficient to economically provide a population with
potable water.
CONCLUSION
Worldwide experience in researching and marketing solar
stills
over three decades has provided an ample foundation for a
solar
still industry. No
inherent technical or economic barriers have
been identified. A
solar still is suited to village
[manufacturing] techniques and to mass production.
Around the
world, concerns over water quality are increasing, and in
special
situations a solar still can provide a water supply more
economically than any other method.
Commercial activities are
picking up after a lull during the late 1970s.
It is now
possible to predict a rapid increase in the manufacture and
marketing of solar stills.
SUPPLIERS
AND MANUFACTURERS OF SOLAR STILLS
Lodestone Engineering
P.O. Box 981
Laguna Beach, California 92652-0981
USA
SOLEFIL
Tour Roussel-Nobel
CEDEX No. 3
F. 92080 Paris La Defense
FRANCE
Cornell Energy, Inc.
4175 South Fremont
Tucson, Arizona
85714
USA
BIBLIOGRAPHY
Cooper, P.I., "Solar Distillation--State of the Art and
Future
Prospects." Solar Energy
and the Arab World (1983): 311-30.
Daniels, Farrington.
Direct Use of the Sun's Energy.
New York,
New York:
Ballantine Books, 1975.
El-Rafaie, M.E.; El-Riedy, M.K.; and El-Wady, M.A.
"Incorporation
of Fin Effect in
Predicting the Performance of Cascaded
Solar
Stills." Solar Energy and the Arab
World (1983): 336-40.
Goetchew, Martin.
"Shedding Light on Solar Collector Glazing."
Materials
Engineering 90 (September 1979): 55-58.
Langa, Fred; Flower, Bob; and Sellers, Dave. "Solar
Glazzings: A
Product
Review." New Shelter (January
1982): 58-69.
Leckie, Jim; Master, Gil; Whitehouse, Harry; and Young,
Lily.
More Other Homes
and Garbage. San Francisco, California:
Sierra Club
Books, 1981.
Mohamed, M.A.
"Solar Distillation Using Appropriate Technology."
Solar Energy and
the Arab World (1983): 341-45.
Talbert, S.G.; Eibling, J.A.; and Lof, George.
Manual on Solar
Distillation of
Saline Water. Springfield, Virginia:
National
Technical Information Service, April 1970.
Dunham, Daniel C.
Fresh Water From the Sun.
Washington, D.C.:
U.S. Agency for
Internation Development, August 1978.
Zaki, G.M.; El-Dali, T.; and El-Shafiey, M.
"Improved Performance of
Solar
Stills." Solar Energy and the Arab
World (1983):
331-35.
***
McCracken, Horace:
Only a small amount of McCracken's work has been
published, but the data are
available. Inquiries
will be welcomed:
McCracken Solar Co.
P.O. Box 1008
Alturas, California 96101
USA
========================================
========================================