COMPARING CHARCOAL AND WOOD-BURNING
COOKSTOVES
IN THE CARIBBEAN
by
Jeffrey L. Wartluft
MONTSERRAT
FUELWOOD/CHARCOAL/COOKSTOVE PROJECT
A cooperative effort by the
GOVERNMENT OF MONTSERRAT, MINISTRY OF
AGRICULTURE (GOM)
CARIBBEAN DEVELOPMENT BANK
(CDB)
VOLUNTEERS IN TECHNICAL
ASSISTANCE (VITA)
and
UNITED STATES AGENCY FOR INTERNATIONAL
DEVELOPMENT (USAID)
Published by
VITA
1600 Wilson Boulevard,
Suite 500
Arlington, Virginia 22209
USA
Tel:
703/276-1800 * Fax:
703/243-1865
Internet:
pr-info@vita.org
TABLE OF CONTENTS
Acknowledgements
1.
Introduction
2.
The Project
Stove selection
Trial charcoal cookstoves
Trial wood-burning cookstoves
Efficiency tests
Economics
Acceptability
3.
Results and discussion
Efficiency
Economics
Acceptability
4.
Conclusions and recommendations
Appendixes
I.
Cookstove designs
II.
Water boiling test procedures
III.
Water boiling test data sheet
IV.
Kitchen performance test data sheet
V.
Cookstove location sheet
VI.
Conversion factors
Bibliography
ACKNOWLEDGEMENTS
This paper
summarizes the efforts of many individuals, particularly
our
Montserrat project team, which consisted of:
Joseph
Daniel,
energy officer; Stedford White, project assistant; James
Silcott,
stove tester; and Meredith White, secretary.
Many other
Montserratians helped with cookstove fabrication, information
gathering and
dissemination, and field testing of cookstoves.
Support for
the team's efforts was provided by Dan Chalmers, Dr.
Jeffrey
Dellimore, Carolyn Cozier, and David Moore of the Caribbean
Development
Bank (CDB); and Richard J. Fera, John M. Downey,
Jane Kenny,
Paula Gubbins, Margaret Crouch, and Julie Berman of
Volunteers In
Technical Assistance.
--Jeffrey L. Wartluft
Project Manager
1.
INTRODUCTION
In
English-speaking countries of the Caribbean, liquid petroleum
gases (lpg)
are the most common cooking fuels. With
the exception
of Trinidad,
lpg is imported and so is expensive for families
as well as a
drain on a country's treasury. Lpg supply
to
these
countries is uncertain too. It depends
on seasonal demand
and shipping
and refinery schedules. The occasional
long lines
at the lpg
dealers bear witness to this problem.
Families who
can afford
to, have purchased two lpg cylinders to get around
delivery
uncertainties. Someday in the future
there will be no
affordable
lpg--it is not renewable.
For most
islands there is an alternative cooking fuel which is
local,
renewable, and viable right now. In
fact, families have
cooked with
it for centuries, and still do. This
fuel is wood
from
forests. However, this valuable
resource is renewable only
if used
wisely. Such use involves many
activities--measuring
supplies and
demands of different products, and satisfying these
demands over
the long term by efficient utilization of the forest
and, if
necessary, prudent plantations of suitable tree species.
The
Government of Montserrat had the foresight to initiate a
project that
would guide the country in managing its forest
resource,
particularly for fuel. In this effort
they enlisted
help from the
Caribbean Development Bank (CDB), Volunteers In
Technical
Assistance (VITA), and the United States Agency for
International
Development (USAID). The Montserrat
Fuelwood/Charcoal/Cookstove
Project, begun
in 1982, is studying 20 fast-growing
tree species
in experimental plantations, assessing the
fuel supply
from natural forests, finding efficient ways to
convert wood
to charcoal, and finding efficient ways to cook with
both charcoal
and wood. This paper reports on the
results of the
cookstove
portion of the Montserrat project.
Because cooking
methods and
cookstoves are similar enough throughout most of the
Caribbean,
the results of the Montserrat work are likely applicable
across the
region.
The 1980
Commonwealth Caribbean Population Census stated that 40
percent of
the people in Montserrat cooked with traditional wood
and charcoal
fuels (GOM, 1980). This surprisingly
high estimate
prompted the
initiation of the project out of concern for the
future of
Montserrat's forest resource. Our own
estimates of
traditional
fuel use were:
Use
Fuel
Percent of Population
full time
charcoal
20
occasional
charcoal 60
full time
wood
5
occasional
wood 40
Meals cooked
with charcoal customarily used cookstoves called
coal pots
(Appendix I). There were several models
using various
materials,
but with very similar designs and sizes (Figure 2).
48p02b.gif (393x393)
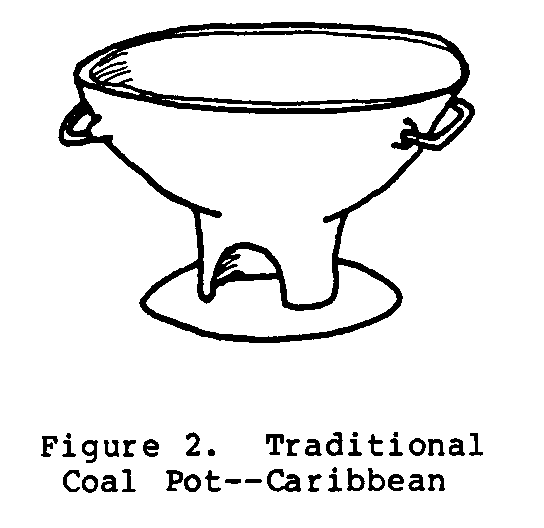
In fact, the
Caribbean coal pot design was similar to many charcoal
cookstove
designs in Asia and Africa. Cookstoves
like these
have been
shown in laboratory tests to have efficiencies (amount
of heat
absorbed by the water/amount of heat available in the
fuel x 100)
around 30 percent (de Silva, 1981; Singer, 1961; and
Tata,
1980). Little is known about the
efficiency of these
stoves in
actual use.
When wood is
used as a cooking fuel, it is usually burned in a
three-stone
fireplace (Figure 1 and Appendix I).
The literature
48p02a.gif (393x393)
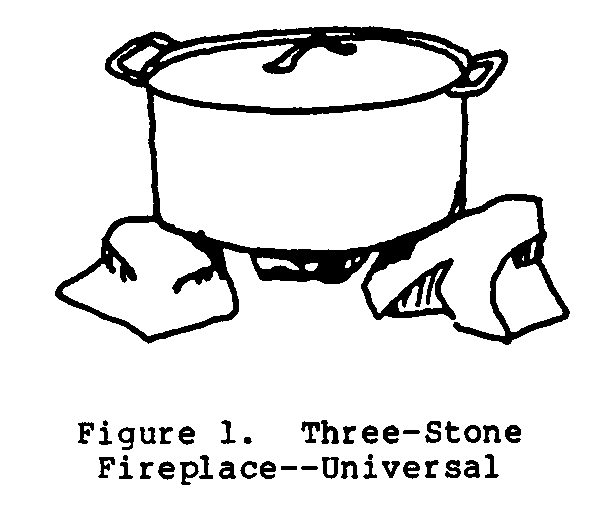
has been
harsh in its evaluation of three-stone fireplace efficiency,
leading one
to believe it is in the order of five to 10
percent.
Recent laboratory and field testing,
however, has shown
a higher
percentage of efficiency, around 17 (Yameogo et al.,
1983).
For certain
cookstove models to "catch on" we felt they should be
efficient,
economical, and acceptable. So we
tested cooking
techniques to
measure these three criteria.
Twenty-six cookstove
models
including the current standards were compared.
Interpretation
of the data
suggested that the smaller cookstoves were
more
efficient and economical, but at a cost in time to bring
food to
cooking temperatures. Positive air
control was important
for
efficiency but difficult to achieve in inexpensive stoves.
Kitchen
performance field testing was valuable in determining
efficiency,
economics, and fuel demand, but definitive data would
require a
large input of time and effort.
2.
THE PROJECT
The
objectives of the Montserrat Fuelwood/Charcoal/Cookstove
Project were
to:
1.
Substitute local renewable cooking fuel from the forest
for imported liquid fuels,
2.
Use the forest resource wisely, and
3.
Create local industry and employment.
Specifically
for the cookstove portion of the project, all three
objectives
would be enhanced by identifying and testing
techniques
for efficiently using charcoal and wood fuel for
cooking.
STOVE
SELECTION
In order to
know if any improvements were made, we had to know
the
performance of the stoves currently in use.
So we selected
four models
of coal pots--cast iron, cast aluminum, clay, and the
converted
steel auto wheel--and the only cookstove used with wood
fuel, the
three-stone fireplace (Figures 1 and 2).
In Montserrat,
wood fuel is
also used in massive stone ovens for baking, but
ovens were
not tested.
Trial
cookstove designs expected to be improvements over the
standard
cookstoves were chosen according to strict criteria.
They had to
be:
1.
simple to build and use,
2.
made locally with local materials,
3.
inexpensive,
4.
appealing in looks, and
5.
formerly tried and reported in the literature.
The only
locally available materials in quantity were sand,
stone, and
clay. From the start, "mud"
stoves were not considered
due to the
strong local feeling that their use would be a
step backward
in progress. Even though clay coal pots
were not
in much favor
because they broke so easily, attractive double-walled
models were
made for both charcoal and for wood fuel.
A limited
number of metal recyclable components were also available
locally.
Our trial designs incorporated used oil
drums,
five-gallon
buckets, steel pipe, paint cans, and tin cans.
All
other materials,
galvanized sheet metal, wire mesh, one quarter
inch rod, and
cement used in trial stoves were imported.
The large
variety in design and size of pots used for cooking in
Montserrat
made decisions on stove dimensions difficult.
Improved
stove features
called for shielding and insulating around the
pots.
So a stove designed for a 10-inch diameter
pot would be
too small for
a 12-inch pot, and allow unnecessary heat loss when
cooking with
an eight-inch pot. Most trial designs
were dimensioned
for 10-12-inch
pots. Coal pots and three-stone
fireplaces
were very
flexible in accommodating various pot sizes, even
frying pans.
Chimneys were
not considered very important in our trial designs.
Other stove
programs have found chimneys to be a mixed blessing
(Foley and
Moss, 1983). And Montserratians were
not fond of the
idea of holes
in their roofs. Cooking with wood was
generally
done
outside. Even though much charcoal was
used inside, Montserratian
homes were
always well ventilated to get the cooling
effects of
constant breezes. Smoke and carbon
monoxide have not
caused
problems. Only the two-hole cement
wood-burning trial
cookstoves
had chimneys.
Even though
there was interest in ovens and grills based on
traditional
fuels, the project did not have sufficient time to
design and
test these. There were several types of
charcoal
"Charlie
Man" ovens in use. One design
employed a used oil drum,
inside of
which was placed a coal pot for heat.
It had a hinged
door for
access, and two steel mesh shelves for baking.
For
added heat,
charcoal was burned on the top. These
drums were not
insulated.
A better design was the wooden box with
hinged door,
tin lining
inside, and shelves. This oven was
heated by placing
a coal pot
with burning charcoal inside. Both
ovens were easy to
build and
required no welding tools or special skills.
Trial
Charcoal Cookstoves
The simplest
design selected for testing was a coal pot modification,
a sheet metal
pot ring. The ring fit over the top of
a
standard coal
pot and had a hole cut in it to match the pot
diameter
(Appendix I). This was an attempt at
keeping the heat
closer
to the pot to enhance heat transfer
into the pot.
The double
skin (DS) fired clay charcoal stove mentioned earlier
provided a
wind screen, preheated secondary air, an insulated
firebox, and
draft control (Figure 3; Appendix I; and Joseph and
48p05a.gif (393x393)
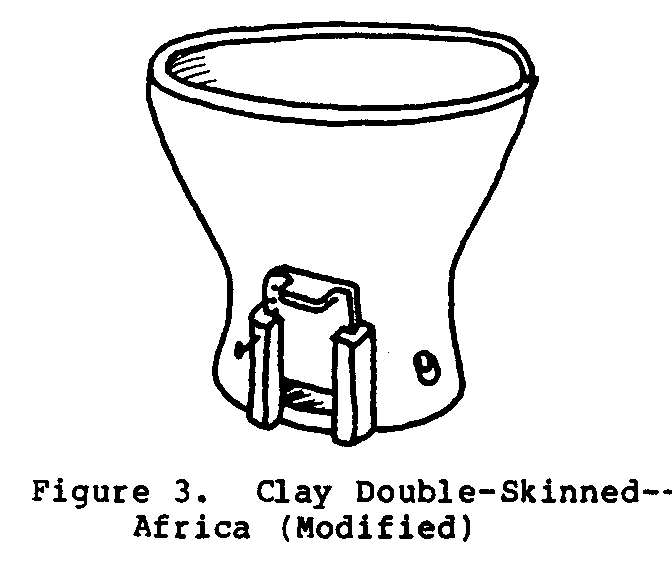
Trussell,
1981). This sophisticated design
originated in Africa.
For use in
Montserrat, the design was slightly modified and was
beautifully
executed by potter Joseph Howson.
Another
design of African origin, the Umeme, was selected.
The
Umeme was
made with galvanized sheet metal and several types of
insulation--air,
soil, and cement. It featured a wind
screen,
tapered
firebox, ash drawer, and draft control (Figure 4; Appendix
48p05b.gif (393x393)
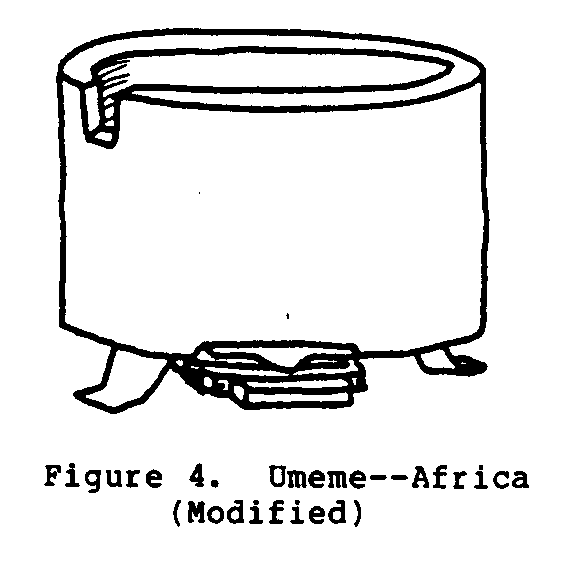
I; and
Hassrick, 1982). Craftsmen fabricating
trial cookstoves
for the
project were encouraged to add their own creativity
to their
work. Three tinsmiths, James Sweeney,
Cecil Roach,
and John
Harris, were enlisted to build the Umeme.
Using the
same
drawings, each came up with quite different looking versions.
Only one
stove selected was manufactured outside Montserrat.
The
Z Ztove, mass
produced in California, USA, was a sophisticated
design made
with sheet metal and ceramic fiber insulation.
It
was tested
because of the possibility of mass producing them in
Montserrat
for the Caribbean market. Features of
the Z Ztove
included
preheated secondary air, firebox insulation, and positive
separate
controls for primary and secondary air (Figure 5
48p06a.gif (437x437)
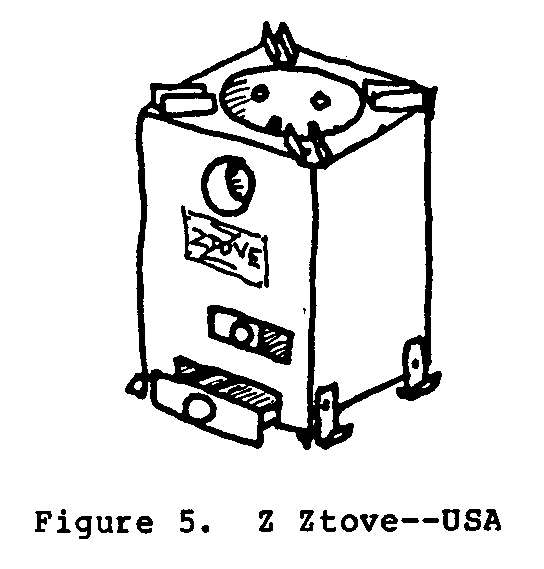
and Appendix
I).
As stove
testing progressed, modifications and new trial designs
were born as
a result of user feedback and our own efforts to
improve stove
performance or acceptance. For
instance, the Z Z
Corporation
made several two-burner and larger burner Z Ztoves at
our request.
Two models
that would be inexpensive and easy to construct in the
home were
tried. The Advanced Charcoal (AC) Stove
used a juice
tin inside of
a paint can, with cement insulation between the
cans (Figure
6 and Appendix I). It was conceived by
Joseph
48p06b.gif (437x437)
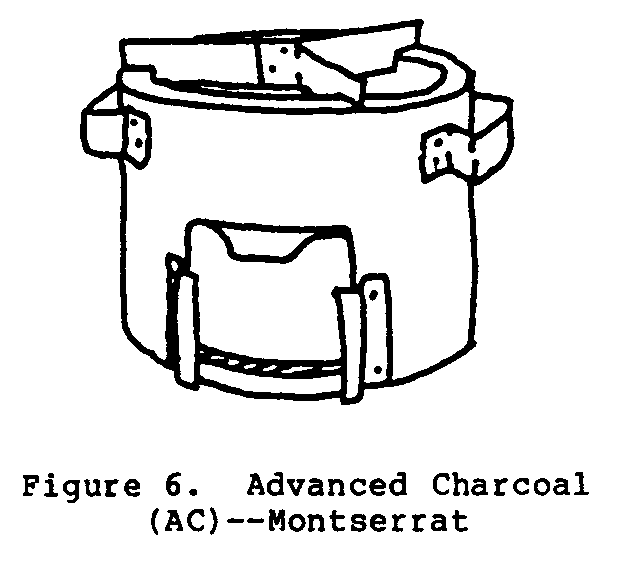
Daniel, the
Energy Officer in Montserrat. The AC
stove was
tested in
three sizes, and with and without a combustion air
preheater and
draft control.
The idea for
the two-can stove design was sparked by a simplified
copy of the Z
Ztove built by Montserratian stove tester James
Bradshaw.
In this simple design a motor oil can was
placed
inside a
paint can (Figure 7 and Appendix I).
The design allowed
48p06c.gif (437x437)
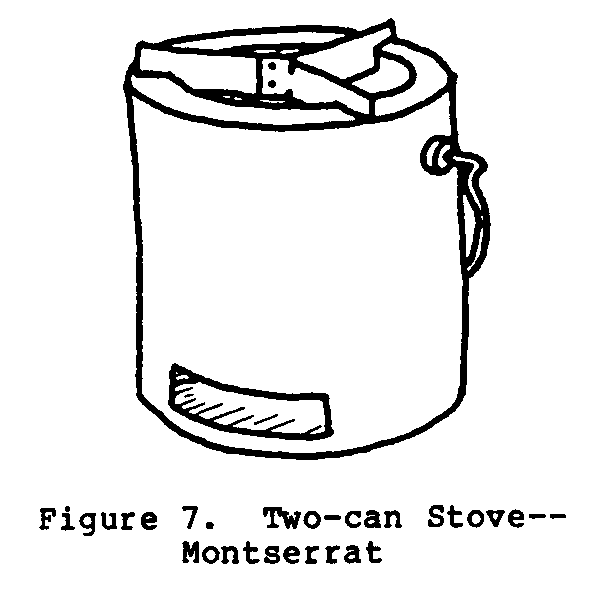
both primary
and secondary air to reach the burning charcoal.
In an effort
to overcome the lack of durability of the Z Ztove
and two-can
stove, the project team designed an attractive Satellite
stove (Figure
8 and Appendix I). Materials used
included
48p06d.gif (437x437)
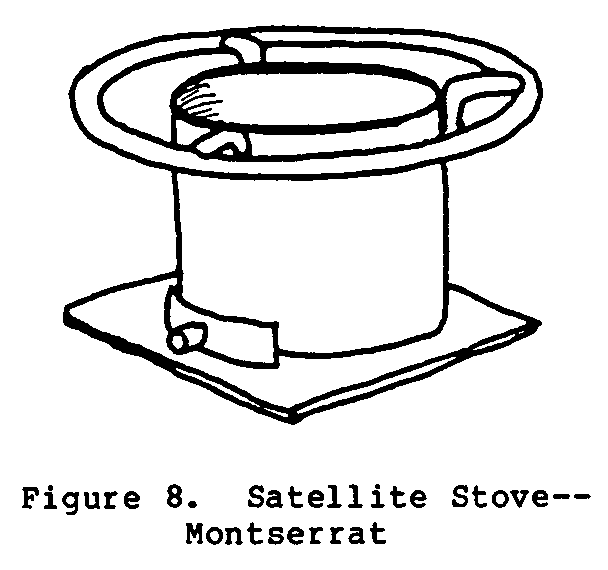
six-inch
diameter steel pipe, steel plate, and steel reinforcing
rod.
The Satellite stove had an ash drawer and
draft control.
Tests were
run with clay and cement liners.
Trial
Wood-burning Cookstoves
The African
double-skinned fired clay stove was selected for
testing.
It had provision for primary and secondary combustion
air (Figure 9
and Appendix I).
48p07a.gif (437x437)
A simple
stove was made from a used five-gallon resin bucket and
some 1/4-inch
rod. The bucket served as the firebox
and pot wind
screen.
The large fuel opening in both the clay and
bucket
stoves
allowed sticks of any length to be used with the stove,
but did not
allow for combustion air control.
Two
reinforced cement cookstoves were built for trial with wood
fuel.
Each was built by different masons,
incorporating some
individual
creativity. One built by Tony Carty and
Charles White
had thicker
walls, a grate, and a removable firebox door.
The
other, built
by Joseph Sweeney and David Lake, had thinner walls,
a hinged
firebox door, and a weight-saving hollow under the
sloping
firebox floor (Figure 10). Each had two
holes for pots
48p07b.gif (486x486)
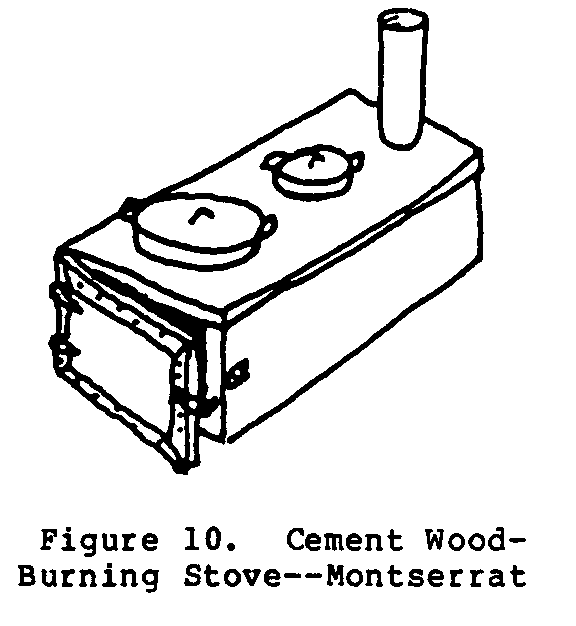
and a short
four-inch diameter chimney. They were
built to be
portable for
demonstration purposes (Appendix I).
EFFICIENCY
TESTS
Two different
tests for efficiency were performed with trial
cookstoves:
the water boiling test (WBT), and the
kitchen performance
test
(KPT). Provisional international
standards for
these tests
were developed during a meeting of experts at VITA
headquarters
(VITA, 1982). We followed these
standard procedures
with a few
modifications.
The WBT
measured the amount of heat used in raising water
temperature
and evaporating water in a ratio over the amount of
heat used
from the fuel. Results were reported as
percent heat
utilized
(PHU). We also reported the time
required for a
standard
quantity of water to boil, and the amount of fuel that
would fit in
the firebox.
Equipment
used in the WBT included:
*
two 11-inch diameter aluminum pots with flat bottoms
and lids,
*
two eight-inch diameter aluminum pots with flat bottoms
and lids,
*
balance accurate to 1/10 gram with a capacity of 6,250
grams,
*
four rubber stoppers with single holes,
*
four mercury thermometers reading to 250 [degrees] F (two spares),
*
electric oven with accurate temperature control to 220 [degrees] F,
*
small tongs,
*
heavy leather gloves,
*
clock reading to the nearest minute,
*
Zip fire fuel pellets (for standardized kindling), and
*
magic markers.
The detailed
procedure is presented in Appendixes II and III.
The second
test measured the relative efficiency of the stove and
operator
together. The KPT was performed by many
different
Montserratian
families. Participating families were
selected to
represent
different economic levels and geographic areas.
In
order to have
reliable results, we needed many families to participate
due to the
added variability of different stove operators,
cooking
styles, food prepared, and eating habits.
Since our time
was limited,
we field tested stoves with as many families as we
could
accommodate in our schedule. Only
charcoal stoves were
tested in the
KPT.
We loaned a
trial stove to each family and gave them a 10-pound
bag of
charcoal with instructions to keep track of the number of
meals cooked
on that stove with that bag of charcoal--no more or
less.
We also asked them to keep track of the
number of people
who ate those
meals, their ages and sex. Each family
was given a
KPT data
sheet to help them record data (Appendix IV).
When we
returned in
two to four weeks we reviewed the data sheet with
them.
We asked for their likes and dislikes about
the stove, if
they used it
for heat needs other than daily meals, and checked
to make sure
they did not use the fuel in different stoves, they
used all the
fuel, and no fuel in addition to what was in the
bag.
At that point we offered to let them repeat
the KPT with a
different
model stove. Once a family had tested
two or more
trial stoves,
we asked them to repeat the KPT with their standard
coal
pot. When we returned for the last
results, we gave them a
bag of
charcoal in appreciation for their cooperation.
The charcoal
was from our
kiln trials in the other segment of our Montserrat
project.
Results of
the KPT were expressed as the number of standard adult
equivalent
meals (SAEM) prepared per 10 pounds of charcoal.
SAEM
were figured
according to a widely used League of Nations formula
which uses
the following values.
Sex and Age
Standard Adult Equivalent Meal
Child, 0-14 years
0.5
Female, over 14 years
0.8
Male, 15-59 years
1.0
Male, over 59 years
0.8
Since there
were a number of stoves with different Montserratian
families
under test simultaneously, and the stoves were switched
around among
families, we used a stove location sheet for each
stove
(Appendix V). By keeping these up to
date, we knew where
each stove
was and when it was time to visit each family.
ECONOMICS
Economic
comparisons of stoves were figured on the cost to use
each type of
stove per SAEM. We maintained records
on the:
1.
material and labor costs of building the stoves,
2.
maintenance costs, and
3.
fuel costs.
To arrive at
the investment or depreciation cost, we estimated
stove life
and divided the original cost of the stove by the expected
SAEM over its
life. Maintenance costs included any
replacement
of parts over
the life of the stove. Again these
costs
were divided
by the expected SAEM over its life.
Fuel costs were
based on EC$5
per 10 pounds of charcoal divided by the average
SAEM per 10
pounds of charcoal from all families testing a particular
stove.
To get the total cost to use each stove
model,
the three
costs per SAEM were added. Each trial
stove model's
cost of
operation was compared to the average cost of operating
all standard
coal pots over one year. This showed
the savings or
losses of
trial stove operation compared to the conventional
cooking
methods. Since we only ran KPT on
charcoal stoves, no
economic
comparisons were made for wood-burning stoves.
ACCEPTABILITY
It was very
difficult to quantify the acceptability of any given
stove model,
so all comparisons made about stove acceptability
were
subjective. Notes were kept on the
comments that people
made about
each stove model. Most information was
collected from
families
participating in the KPT. During each
visit with a family,
they were
specifically asked what they liked and disliked
about the
stove (Appendix IV).
When participants were reluctant
to answer the
general questions, more specific questions were
asked about
stove size, materials, looks, and operating features.
Feedback from
families testing stoves was valuable in guiding our
attempts to
modify stove features for greater acceptance.
3. RESULTS
AND DISCUSSION
The limited
duration of this project did not allow definitive
answers to
the question of which cooking technique among those
tested was
the best in terms of efficiency, economics, and acceptability.
However, the
tests did allow us to establish some
baseline data
on traditional cooking practices and to pick out
some general
indications for improving them.
EFFICIENCY
There were
several differences between the two tests for efficiency.
With WBT we
intended to screen stove models and features
in order to
select two or three of the best for the important KPT
field
testing. WBT results were not
indicative of expected fuel
savings of
cookstoves in actual use because they did not measure:
the operator
variable. So to get a measure of the
efficiency of
stoves and
operators together, we ran the KPT.
We found the
KPT results particularly useful.
Besides (1) comparing
the
efficiency of different stove models in actual use, we
(2) applied
the results in our economic comparison of stoves, (3)
used feedback
for gauging acceptance of different stove models,
and were able
to (4) estimate the demand for fuel from the forest,
which could
then be matched with forest inventory data to
see if tree
plantations were-necessary to satisfy demand without
depleting the
resource.
WBTs were
easier to conduct than KPTs. WBTs only
involved our
project team,
while KPTs involved many people and required travel
and visit
time. In two months time, 160 WBTs were
performed, an
average of
four per day. In approximately six
months time, 55
families
participated in the KPT, with 37 usable responses collected.
Many families
did not fully understand our purpose--or
pretended not
to understand in order to keep the trial stoves for
longer
periods of time. We made up to four
visits to the same
family to get
a single response. In order to speed up
data
collection,
we enlisted the help of teachers and agriculture
extension
agents. This effort, too, brought
variable results.
Due to the
greater variability of KPT results, more tests were
needed than
in WBT for the same degree of predictability.
Unfortunately,
the more
useful information required a much greater
effort.
Interestingly,
the cheapest and simplest cookstove, the two-can,
had the
highest average WBT efficiency, 34 PHU (Table 1).
Other
cookstoves
that rated above 30 PHU in this comparison were the
small AC with
preheater and air control and the cast aluminum
coal pot,
each with 32 PHU, and the five-gallon bucket woodburning
stove at 31
PHU. The poorest performers were the
cement
wood-burning
stoves, the Satellites, and the Umemes, all with
less than 20
PHU.
Among the
traditional coal pots, the cast aluminum averaged 10
percentage
points better than the clay, cast iron, or steel.
All
tested coal
pots had similar shapes and sizes.
Since clay was
the best
insulator of the materials tested, we expected it to
perform
better than the metals, which were all good conductors of
heat.
One possible explanation for aluminum's
superiority was
that its
relatively high emissivity or ability to reflect heat
back into the
fire overcame its ability to conduct heat away from
the
fire. Indeed, some cookstove
researchers have lined fireboxes
with shiny metals
to improve stove efficiency. Perhaps if
the firebox
walls of the cast aluminum coal pot were polished, it
would be an
even better stove.
We got
conflicting results testing firebox insulation.
The Umeme
stove worked
best with cement, next best with soil, and poorest
with air
insulation. The Satellite did best with
clay, next best
with cement,
and poorest with no insulation. On the
other hand,
the two-can
stove was more efficient without a clay liner, and
Table 1.
Cookstove Efficiency Test Results
Water Boiling Test
[a] Kitchen Performance
Time
No. Meals
Fuel
to
PHU
of
per
SAEM
charge
boil
coef.
re- lb
coef.
(lbs)
(min)
PHU of
spon-
coal of
Cookstove
& features [b]
[c]
(%) var.
ses
(SAEM) var.
Charcoal Cookstoves
Clay coal
pot 1.27
22
21 .57
-
- -
Cast iron
coal pot 1.29
21
22
.27
2 2.5
.04
Cast alum.
coal pot 1.16
22
32 .40
2
3.7 .11
Wheel coal
pot 1.46
24
22 .24
1
1.0 -
" /pot ring
1.32
25 22
.14
2 5.4
.28
Umeme/cement
insul. 1.40
22
20 .28
6
2.8 .30
" /soil insul.
1.11
22 16
.24
6 4.0
.37
" /air insul.
1.27
29 14
.09
- -
-
Small AC
.57
34
21 .22
4
5.7 .57
" /preheater
.32
38 25
.11
1 6.2
-
Medium
AC .57
27
25 .26
-
- -
Large AC
.79
24
24 .15
-
- -
" /preheater
.66
22 25
.16
- -
-
Z Ztove
.42
24
27 .45
5
4.7 .80
" /double burner
.48
26 25
.14
6 5.6
.66
" /large burner
1.26
20 22
.10
- -
-
Two can
.28
27
34 .28
1
3.3 -
" /clay liner
.34
29 26
.27
-
- -
Satellite
1.36
29
11 .43
-
- -
" /cement liner
.91
29 16
.27
1 2.0
-
Table 1 - Continued
Water Boiling Test
[a] Kitchen Performance
Time
No.
Meals
Fuel
to
PHU of
per
SAEM
charge
boil
coef. re-
lb
coef.
(lbs)
(min) PHU
of spon- coal
of
Cookstove
& features [b]
[c]
(%) var.
ses
(SAEM) var.
"
/clay/preheat. .72
23
24 .14
-
- -
Short
satellite/cement .63
26
22 .25
-
- -
Wood-burning
Cookstoves
3-stone
fireplace 27
.43
- -
-
5-gallon
bucket 31
.45
-
- -
Cement/grate
[d] 10
14
.94 -
-
-
"
/sloping floor [e]
10 12
.59
- -
-
[a]
Averages based on at least five tests.
[b]
To convert to kilograms, multiply by .454.
[c]
Amount boiled was 2 kg. Does not include first five
minutes from the time of lighting.
[d]
Based on four tests, PHU total of two pots.
[e]
Based on three tests, PHU total of two pots.
the
non-insulated five-gallon bucket wood-burning stove was more
efficient
than the cement walled wood-burning stoves.
In the
case of the
two-can stove, the air that was insulating the firebox
was heated,
then moved beneficially into the fire as preheated
secondary
combustion air. The insulating air in
the Umeme
was dead
air. Once heated, it then transferred
the heat to the
outer shell
of the stove from where it escaped into the air.
In the
five-gallon bucket stove, increased efficiency was probably
due more to
the fact that in the simmer stage the fuel was
retracted
from the firebox for heat control. In
the Umeme,
Satellite,
and cement wood-burning stoves, heat was not as effectively
lowered by
closing the not-so-positive air controls, loose
fitting ash
drawers and doors. Therefore, more heat
than needed
was used
up. So if positive air control or
ability to manipulate
fuel are
features of a cookstove, insulation is not as important.
For instance,
the three-stone fireplace did not have insulation
or even a
wind shield; but with manipulation of the fuel, its PHU
was a
respectable 27.
Recent
African stove testing programs pointed out that thin-walled
metal
cookstoves were more efficient than massive cookstoves
for cooking
durations less than 100 minutes. Only
when
cooking times
were longer, say for restaurants or institutions,
or at high
altitudes, would massive stoves lose less heat through
conduction
(Baldwin, 1984).
Combustion
air preheaters seemed to improve efficiency.
In both
the small and
large AC stoves and the Z Ztove (the double burner
Z Ztove did
not have preheated secondary air) where this feature
was tested,
the preheaters added one to four PHU to the stove's
efficiency.
Even though
grates were not tested for charcoal cookstoves, it
was obvious
in the smaller models that the maximum air possible
was
necessary. In small stoves without
secondary combustion air,
ash build-up
tended to close off the holes in grates.
For this
reason all of
the smaller charcoal cookstoves were provided with
grates of
1/4-inch wire mesh. One of the two
cement wood-burning
models had an
iron bar grate. Its efficiency was two
PHU greater
than the
model without a grate.
Control of
combustion air was important to stove efficiency.
With good air
control fuel consumption was lowered to the amount
needed for
simmering, once the pot was boiling. In
the AC stove,
a slide
control over the draft opening increased the stove's
performance
by seven PHU. The Z Ztoves all had
positive air
controls and
good PHUs.
The
variability of test results seemed high considering the tests
were
controlled to minimize variation. PHU
coefficients of variation
ranged from
10 to 94 percent. Wood-burning
cookstoves had
much more
variation than charcoal cookstoves.
Wood was a more
variable fuel
than charcoal in size, shape, and moisture content.
Wood fires
were trickier to control. Charcoal
cookstove results
with high
variation included the clay coal pot, Z Ztove, Satellite,
and cast
aluminum coal pot. There was no obvious
common
trait to
explain their higher variability. A
certain amount of
variation was
certainly due to the stove testers.
Three of us
from the
project team did the testing. I suspect
from observation
that some of
the variation in performance not specific to
any one stove
model but more likely to affect smaller stoves, was
due to the
random arrangement of fuel and how it affected air
flow through
the fuel. The same stove operated in
exactly the
same manner
would sometimes fire up quickly and lively and other
times barely
perk along.
It took
anywhere from 20 to 38 minutes to boil two kilograms of
water with
charcoal. This did not include the
first five minutes
after
lighting the fire and allowing it to catch.
Among charcoal
cookstoves
the ability to boil faster belonged to those with
larger
fireboxes (Table 1). The small AC stove
with the next to
smallest
amount of fuel charge required the longest times to
boil.
The five-minute waiting period before
putting on the pot
to boil was
arbitrary. Some additional testing
determined that a
charcoal fire
needed about 10 minutes to be fully lit, after
which boiling
times averaged around 15 minutes. The
fastest
individual
boiling time with charcoal was on the Z Ztove with 12
minutes to
fully light, and nine minutes to boil.
By contrast,
the same
amount of water was boiled in the same pot on an lpg
cookstove in
six to 14 minutes, depending on burner size.
The
manufacturer of the Z Ztove also made a multi-fuel backpacking
stove that
was supercharged with a C cell battery and small
fan.
Charcoal was fully lit in it after just one
minute. In
about two
minutes some of the charcoal was white hot, indicating
temperatures
near 2800 [degrees] F. And flames from
the stove made it look
like a gas
stove. The project team built a bellows
to supercharge
trial
stoves. It worked well, but required a
cook's
attention.
Besides, a traditional piece of cardboard
for fanning,
although not
as effective, was much cheaper.
In actual use
the AC stoves were the most efficient according to
KPT (Table
1). They cooked an average 5.8 SAEM per
pound of charcoal.
Next were the
Z Ztoves with 5.2 SAEM per pound of charcoal,
and then the
coal pots with 3.5 SAEM per pound of charcoal.
The Umeme
stoves averaged 3.4 SAEM per pound of charcoal, no
better than
the standard coal pots. Since there
were few test
responses, we
grouped these stove types for comparison.
These
tests
suggested that the smaller the stove, the more efficiently
it worked
under actual conditions.
Since the
two-can and Satellite charcoal cookstoves were models
developed
late in the project, only one KPT response was available
for
each. Dissemination of these results is
to take place
during the
second year of the project. The KPTs
will be ongoing
in conjunction
with dissemination.
No tests were
made of the clay DS stoves as they broke after a
few uses.
A comparison
of the results of the WBT and KPT showed that WBT
results could
not be used to predict fuel savings of cookstoves
under actual
use. For example, the WBT results for
coal pots as
a group were
in the mid range, but under KPT were clearly inferior.
Though the
KPT results indicated that a 49 to 66 percent fuel
savings would
be possible by using AC stoves or Z Ztoves rather
than coal
pots, these estimates were based on few data.
And
"improved"
stove use would also hinge on their economics and
their
acceptance.
ECONOMICS
A comparison
of the economics of using cookstoves showed that the
AC stoves
were cheapest, followed by the Z Ztoves (Table 2).
The
Umeme stoves
were more costly to use than the coal pots.
Since
the economic
calculations were based on KPT results, insufficient
data were
available to compare the two-can, Satellite, and all
wood-burning
cookstoves. In fact, we grouped the data
by stove
type for this
comparison because there were few KPT responses.
Fuel cost
emerged as a more influential cost than investment or
maintenance
costs. The stoves with smaller
fireboxes and less
fuel
consumption per meal, the AC and Z Ztoves, would save about
EC$100 and
EC$25 respectively per year compared with the use of
traditional
coal pots. The use of Umeme stoves
would actually
cost about
EC$65 more than using coal pots.
Theoretically,
with improvements in cooking practices brought
about by
public education campaigns, cooking could become more
efficient and
economical than our estimates of present day practices.
With this in
mind, the Energy Officer in Montserrat
issued a
kitchen calendar with tips on fuel conservation such as
using lids on
cooking pots, using smaller amounts of water when
cooking
vegetables, using pressure cookers, etc.
It is
important to realize that our economic comparisons ignored
the capacity
of a particular stove to cook for different sized
families.
A
small cookstove could not adequately cook a large
pot of
food. Of course a large family could
use several small
cookstoves
and experience the same savings, as
long as large pots
were not used
for cooking. However, cooking in large
pots is
common in the
Caribbean. The fact that smaller
cookstoves were
shown to be
more efficient and economical does not guarantee that
they would be
acceptable to users.
Table 2.
Economic Comparison of Charcoal Cookstove Use
Coal
Z
Item
pots
Umeme
Ztove AC
Purchase cost
(EC$) 44
180
83[a] 30
Estimated
stove life (years) 7
3
2 4
Maintenance
cost over life
of stove (EC$)
15
9 30
8
Stove/operator
efficiency
(SAEM/pound charcoal)
3.5
3.4 5.2
5.8
KPT responses
(no.) 7
12
11 5
Fuel cost
(EC$/SAEM) [b] 0.143
0.147
0.096 0.086
Investment
cost (EC$/SAEM) [c] 0.003
0.032
0.022 0.004
Maintenance
cost (EC$/SAEM) [c] 0.001
0.002
0.016 0.001
Total cost
(EC$/SAEM)
0.147
0.181 0.134
0.091
Savings
[loss] compared to
coal pots (EC$/year) [c]
-
[64.53] 24.67
106.29
[a]
Purchase cost as imported.
[b]
Fuel cost, EC$.50 per pound.
[c]
Average family of three cooks 5.2 SAEM per day or
1898 SAEM per year.
ACCEPTABILITY
Inasmuch as
people's opinions on any single subject vary tremendously,
there was no
one trial cookstove model that was universally
acceptable.
A range of cookstove models would have to be
available to
satisfy all people's desires and cooking needs.
To begin
with, there was no perceived need among the users of
coal pots and
three-stone fireplaces for improving upon traditional
cooking
systems. The government felt the need
to protect
its valuable
forest resource by introducing more efficient cooking
methods.
So there was
a need to develop a consciousness in the people
about cooking
fuel efficiency. Therefore, very few
comments were
made about a
cookstove's efficiency, the major reason for the
project's
existence. Most concerns were expressed
about cookstove
appearance,
how well they worked, how they fit the cooking
needs, how
durable they were, what the working features were,
their cost,
and their efficiency, in roughly that order of importance
to potential
users.
The most
excited feedback we received was based on a trial
stove's
looks. Older users seemed to prefer the
Umeme, perhaps
because they
were more like coal pots than other trial cookstoves.
Younger folks
seemed to like the smaller, more modern
looking
stoves. The most coveted design was the
Z Ztove, with
its
manufactured look.
People liked
the way the smaller stoves worked, but the stoves
did not
always fit their needs. Cooking
capacity generally was
lacking.
Comments such as these led us to enlarge
several cookstove
models.
At our request, the Z Ztove manufacturer
sent us
modifications
of the Z Ztove that were double burners and single
but larger
burners. We had local tinsmiths make
two larger sizes
of AC stoves.
The larger models were well received.
Cookstove
durability was a concern. Clay coal
pots were not
favored due
to their fragility. We found that
expensive sheet
metal lining
around fireboxes lasted only one to three months.
The Umeme, Z
Ztoves, AC stoves, and two-can stoves had these
liners.
It was of little concern in the Umeme and AC
stoves with
their cement
insulation. Once the tin burned out the
cement
became the
firebox wall. The tin merely acted as a
form for the
cement.
But the firebox lining had to be replaced
periodically
in the other
stoves. The Z Ztove had easily
replaceable liners,
and the
two-can stove used easily replaced motor oil cans.
But
the Umeme
with soil insulation required shaping sheet metal into
a cone for
relining. Concern was registered for
the durability
of wire mesh
grates, but these were inexpensive and easily replaced.
Of the
working features of cookstoves, the most appreciated was
the ash
drawer for ease in emptying the ashes.
The ash drawers
also doubled
as air control, but there seemed to be little esteem
for its value
in conserving fuel.
The fact that
much food was cooked in frying pans led to our
modified wind
shield with slot for frying pan handle on the Umeme
stoves.
That made them more acceptable.
The large
Umemes with cement or soil insulation were very heavy.
Montserratians
moved their coal pots around--to light them outside,
bring them
inside for cooking, and back outside for emptying
ashes.
We tried reducing the weight of cement
insulated
models by
incorporating charcoal fines into the cement mix.
We
never really
overcame that objection to the Umeme.
Another
objection to the Umeme stoves was the lack of air getting
to the
fire. The only combustion air in Umemes
was that which
was pulled up
to replace the hot air rising out of the stove.
Coal pots
were designed such that when the "arch" (draft opening)
was faced
into the breeze, the air going into the arch was all
forced up
into the fire. Breezes simply passed
under the Umeme.
For many
families the cost of a cookstove was not important.
Nevertheless
a segment of the stove testers complained about not
being able to
afford a new cookstove. For these
people we developed
the AC and
two-can charcoal stoves, and introduced the five-gallon
bucket wood-burning
stove. Each of these models was
inexpensive
and easy enough for most families to make in their
own
home. However, the two charcoal stoves
were small and had a
homemade
look, which detracted from their acceptance.
And because
wood fuel use
was associated with families in the lowest
economic
group, any wood-burning cookstove had to overcome that
debasement to
be acceptable.
If we had to
rank cookstoves according to their overall acceptability,
they would
roughly follow in order of descending acceptance:
1.
coal pots for their familiarity,
2.
Satellite stove for its good looks and durability,
3.
Z Ztove for its good looks and working ability,
4.
Umeme stove for its similarity to coal pots and ash
drawer,
5. AC stove for its
simplicity and low cost,
6.
two-can stove for its simplicity and low cost,
7.
five-gallon bucket stove for its simplicity and low
cost,
8.
the cement wood-burning stoves, and
9.
the clay cookstoves.
As time goes
by this ranking could change. People
will become
more aware of
the value of improved stove efficiency as lpg
becomes more
expensive and competition for wood and charcoal
becomes more
keen.
Cooking with
wood and charcoal was dirtier and slower than cooking
with
lpg. In an effort to help clean up the
handling of
charcoal, the
project introduced the use of inexpensive ice tongs
and scoops
cut from discarded plastic bleach bottles.
For faster
starting of
charcoal fires, a tin juice can with top and bottom
removed, and
side air holes punched around the bottom was promoted.
With one
sheet of crumpled newspaper in the bottom and
charcoal in
the top of the upright cylinder, a fast fire was
assured for
even the novice fire builder (providing the charcoal
was dry).
It was hoped
that all of these efforts at improving cookstoves
and cooking
systems would help elevate the status of using wood
and charcoal
fuels, and assure a perpetual supply of these local
renewable
resources.
4.
CONCLUSIONS AND RECOMMENDATIONS
Test results
and user comments led us to the following conclusions:
1.
Smaller charcoal cookstoves were more efficient and
economical than traditional coal
pots, but required
more cooking time and often were not
suitable to the
cooking needs of Montserratian
families.
2.
Positive air control was difficult to achieve in cookstoves,
but improved their efficiency.
3.
Insulating the firebox was most useful in cookstoves
without air control or the ability to retract the fuel.
4.
Grates in smaller charcoal cookstoves needed maximum
air holes.
5.
The cast aluminum coal pot was superior to other coal
pots in efficiency.
6.
Kitchen performance testing (KPT) of cookstoves yielded
information for many important uses,
but required a
large input of time and effort.
7.
The operator variable in cooking system efficiency is
so great that more impact on fuel
conservation might be
possible through public education
(people improvement)
than through stove improvement.
And finally,
we concluded that a number of suggestions for
further work
are in order:
1.
Continue kitchen performance testing of stove models to
obtain solid baseline data on the
number of standardized
meals prepared by each oven dry pound
of fuel.
2.
Participate in public education efforts to conserve
cooking fuels.
3.
To overcome problems in production and quality control,
develop systems to mass produce
inexpensive cookstoves.
4.
Develop a small battery-powered fan unit with variable
speeds to hook to small cookstoves
for supercharging
combustion air.
5.
Develop a more durable firebox and top for the Z Ztove.
6.
Polish the firebox walls of the aluminum coal pot and
retest for efficiency.
APPENDIX I
COOKSTOVE DESIGNS
FCCA
MONTSERRAT
FUELWOOD * CHARCOAL * COOKSTOVE
PROJECT
Name and
origin of stove TRADITIONAL COAL
POT-CARRIBEAN
Name of stove
builder(s) VARIOUS
Construction
date 1982
Materials used
CAST ALUMINUM,
CAST IRON,
CLAY, OR CEMENT WITH WIRE ROD AND DRUM STEEL.
<FIGURE
A>
48ap01.gif (600x600)
Details of
stove construction GRATE IS CAST
SEPARATELY. CLAY
COAL POTS
CLAY GRATES, WHILE CEMENT COAL POTS USE OIL DRUM
STEEL WITH
PUNCHED HOLES.
FCCA
MONTSERRAT
FUELWOOD * CHARCOAL * COOKSTOVE
PROJECT
Name and
origin of stove CLAY DOUBLE-SKINNED -
AFRICA (MODIFIED)
Name of stove
builder(s) Joseph Howson
Construction
date 2/83
Materials used
CLAY MIXTURE WITH
WHITE
VOLCANIC POWDER AND ONE NAIL.
<FIGURE
B>
48ap02.gif (600x600)
Details of
stove construction INSIDE AND OUTSIDE
CYLINDERS WERE
TURNED
SEPARATELY, JOINED, CURED, AND FIRED AT 900-1100 [degrees] C.
SECONDARY
AIR HOLES
WERE 12-IN. DIAM. AND SLANTED UPWARD TOWARD THE INSIDE.
WALLS
OF FIREBOX
WERE ROUGH TO PROMOTE MIXING OF GASES AND AIR.
DRAFT
DOOR
ADJUSTABLE WITH NAIL.
FCCA
MONTSERRAT
FUELWOOD * CHARCOAL * COOKSTOVE
PROJECT
Name and
origin of stove UMEME - AFRICA
(MODIFIED)
Name of stove
builder(s) John Harris, James Sweeney,
Cecil Roach
Construction
date 2/83
Materials used
SHEET METAL WITH
CEMENT, AIR,
OR SOIL INSULATION, NAILS, 1/4-INCH ROD, AND DRUM STEEL
<FIGURE
C>
48ap03.gif (600x600)
Details of
stove construction NAIL RIVETS FASTENED
THE ASH DRAWER,
DRAFT SLIDE
AND DRAWER RAIL TO THE BOTTOM, AND THREE LEGS
TO THE
BOTTOM. CHARCOAL FINES WERE MIXED WITH
CEMENT TO LESSEN
THE
WEIGHT. POT SUPPORT RODS EXTENDED INTO
THE CEMENT. NOTCH IN
WIND SCREEN
WAS FOR FRYING PAN HANDLE.
FCCA
MONTSERRAT
FUELWOOD * CHARCOAL * COOKSTOVE
PROJECT
Name and
origin of stove ADVANCED CHARCOAL (AC)
- MONTSERRAT
Name of stove
builder(s) JOHN HARRIS, JAMES DYER
Construction
date 4/83
Materials used
VARIOUS CANS, NAILS,
DRUM STEEL,
1/4-INCH AND 1-INCH WIRE MESH, 1/4-INCH ROD, AND CEMENT
<FIGURE
D>
48ap04.gif (600x600)
Details of
stove construction CEMENT INSULATION
WAS REINFORCED
BY 1-INCH
MESH WIRE. POT REST/WIND SHIELD AND
HANDLES MADE WITH
DRUM STEEL,
FASTENED WITH NAIL RIVETS. DRAFT DOOR
AND AIR PREHEATER
MADE WITH
TIN. 1/4-INCH ROD SUPPORTS AIR
PREHEATER WHICH
SUPPORTS
1/4-INCH MESH GRATE.
FCCA
MONTSERRAT
FUELWOOD * CHARCOAL * COOKSTOVE
PROJECT
Name and
origin of stove Z ZTOVE - U.S.A.
Name of stove
builder(s) ZZ CORPORATION
Construction
date 2/83
Materials used
SHEET METAL,
POP RIVETS,
1/4-INCH WIRE MESH, AND CERAMIC FIBER.
<FIGURE
E>
48ap05.gif (600x600)
Details of
stove construction THE Z ZTOVE IS MASS
PRODUCED
FROM PRE-CUT
SHEET METAL PARTS. THEY ARE BENT IN
PRESSES, GANG
DRILLED, AND
POP RIVETED. THE INNER BURNER BOWL IS
REPLACEABLE
AFTER IT
BURNS OUT.
FCCA
MONTSERRAT
FUELWOOD * CHARCOAL * COOKSTOVE
PROJECT
Name and
origin of stove TWO CAN STOVE -
MONTSERRAT
Name of stove
builder(s) ANYONE
Construction
date 7/83
Materials used
PAINT CAN, MOTOR
OIL CAN, DRUM
STEEL, AND NAILS.
<FIGURE
F>
48ap06.gif (600x600)
Details of
stove construction FIRST PUNCH MOTOR
OIL CAN FULL OF HOLES,
THEN REMOVE
ITS TOP, CUT PAINT CAN LID RADIALLY LEAVING SHORT TABS UNTIL
THE MOTOR OIL
CAN FITS DOWN IN IT AND IS SUPPORTED BY ITS FLARED TOP
EDGE.
PLACE LID WITH MOTOR OIL CAN ON PAINT
CAN. THEN CUT OPENING
FOR DRAFT AND
MAKE POT REST WITH DRUM STEEL AND NAIL RIVETS.
FCCA
MONTSERRAT
FUELWOOD * CHARCOAL * COOKSTOVE
PROJECT
Name and
origin of stove SATELLITE STOVE -
MONTSERRAT
Name of stove
builder(s) SYLVESTER MEADE
Construction
date 9/83
Materials used
SIX-INCH STEEL PIPE
1/8-INCH
STEEL PLATE, 1/2-INCH REBAR, 1/4 INCH
ROD, SHEET METAL, 1/4-INCH WIRE MESH
<FIGURE
G>
48ap07.gif (600x600)
Details of
stove construction PIECES WERE WELDED
TOGETHER,
ASH DRAWER
WAS FASHIONED FROM SHEET METAL. A CLAY
CYLINDER
AND CEMENT
WERE TRIED AS INSULATION.
FCCA
MONTSERRAT
FUELWOOD * CHARCOAL * COOKSTOVE
PROJECT
Name and
origin of stove THREE-STONE FIREPLACE -
UNIVERSAL
Name of stove
builder(s) ANYONE
Construction
date 9/83
Materials used
THREE STONES
<FIGURE
H>
48ap08.gif (600x600)
Details of
stove construction PLACE THREE STONES
SO THEY
SUPPORT THE
POT ABOVE THE GROUND AND LEVEL.
FCCA
MONTSERRAT
FUELWOOD * CHARCOAL * COOKSTOVE
PROJECT
Name and
origin of stove CLAY DOUBLE-SKINNED
WOOD-BURNING STOVE-AFRICA (MONFIED)
Name of stove
builder(s) Joseph Howson
Construction
date 2/83
Materials used
<FIGURE
I>
48ap09.gif (600x600)
Details of
stove construction INSIDE AND OUTSIDE
CYLINDERS WERE
TURNED
SEPARATELY, JOINED, CURED, AND FIRED AT 900-1100 [degrees].
SECONDARY
AIR HOLES
WERE 1/2-INCH DIAM. AND SLANTED UPWARD TOWARD THE
INSIDE.
WALLS OF FIREBOX WERE ROUGH TO PROMOTE
MIXING OF GASES
AND AIR.
FCCA
MONTSERRAT
FUELWOOD * CHARCOAL * COOKSTOVE
PROJECT
Name and
origin of stove FIVE-GALLON BUCKET
WOOD-BURNING STOVE-AFRICA
Name of stove
builder(s) ANYONE
Construction
date 8/83
Materials used
FIVE-GALLON BUCKET
AND 1/4-INCH
ROD.
<FIGURE
J>
48ap10.gif (600x600)
Details of
stove construction SIMPLY PUNCH THREE
EQUIDISTANT
HOLES AROUND
THE CIRCUMFERENCE, INSERT 11-INCH LONG RODS AND
BEND ROD
ENDS. THEN CUT OUT THE DRAFT OPENING.
FCCA
MONTSERRAT
FUELWOOD * CHARCOAL * COOKSTOVE PROJECT
Name and
origin of stove CEMENT WOOD-BURNING
STOVE-MONTSERRAT
Name of stove
builder(s) TONY CARTY AND CHARLES WHITE
Construction
date 4/83
Materials used
CEMENT, 1/2-INCH
REBAR, REINFORCING
MESH, WOOD, SHEET METAL, AND NAILS.
<FIGURE
K>
48p11.gif (600x600)
Details of
stove construction THE TOP SLAB IS
POURED AROUND THE
ACTUAL
POTS. POTS ARE REMOVED AND POT HOLES
SMOOTHED WHEN CEMENT
IS PARTIALLY
CURED. DOOR IS WOOD-LINED WITH TIN
INSIDE. GRATE IS
MADE OF
REGARS. AND REBAR HANDLES ALLOW FOR
PORTABILITY. REINFORCING
MESH IS
INSIDE CEMENT.
FCCA
MONTSERRAT
FUELWOOD * CHARCOAL * COOKSTOVE
PROJECT
Name and origin
of stove CEMENT WOOD-BURNING
STOVE-MONTSERRAT
Name of stove
builder(s) Joseph Sweeney and David
Lake
Construction
date 9/83
Materials used
CEMENT, CHICKEN
WIRE, WOOD,
SHEET METAL, HINGES, AND NAILS.
<FIGURE
L>
48ap12.gif (600x600)
Details of stove
construction THE TOP SLAB IS POURED
AROUND THE
ACTUAL
POTS. POTS ARE REMOVED AND POT HOLES
SMOOTHED WHEN CEMENT
IS PARTIALLY
CURED. THE HINGED DOOR IS WOOD LINED
WITH TIN ON
THE
INSIDE. THE CHIMNEY IS SHEET
METAL. CHICKEN WIRE IS USED
TO REINFORCE
THE CEMENT.
APPENDIX II
WATER BOILING TEST PROCEDURES
In order to
compare different designs of stoves, all variables
other than
stove design that might affect efficiency such as
fuelwood
species, moisture content, size, and amount; operator
and operating
sequence and schedule; weather (mainly wind); and
pot design,
size, material, and contents were held as consistent
as possible.
The testing
was conducted according to the following procedures:
1.
We sampled the fuel to determine moisture
content (MC). For
charcoal we disregarded MC unless it had
been wetted. The
MC samples were at least 100 grams and
were chosen to be
representative of the fuel being
used. They were cut just
before the WBT.
We weighed the samples immediately to the
nearest 1/10 gram and recorded the
weight. We identified
each sample by marking a number directly
on it with a magic
marker.
The samples were put in an oven at 215 [degrees] F for at
least 24 hours (until they lost no more
weight) and reweighed.
The oven dry weights were recorded.
Then MC was
calculated on the green weight basis by
the formula:
percent MC = (green weight - oven dry
weight/green
weight) x 100.
2.
We weighed the fuel put in the stove and
recorded the weight
in pounds.
3.
We weighed an 11-inch diameter flat bottomed
aluminum pot
without the lid.
The weight was recorded.
Then we added
two kilograms (four pounds, six ounces) of
water at ambient
temperature and recorded the weight.
The lid was fitted
with a stopper through which a mercury
thermometer was
placed.
The lid was put on the pot and the thermometer
adjusted to be about one inch from the
bottom of the pot.
For two-pot stoves we used an 11-inch and
an eight-inch
diameter pot of the same design.
4.
We used two Zip fire fuel pellets for
kindling, lit them and
recorded the time.
We added the fuel.
5.
After allowing five minutes for the fire to
get started, we
put the pot(s) on.
The fire was maintained for maximum heat
until the water was boiling.
6.
At each five-minute interval, the time and
temperature of
each pot were recorded.
When the thermometer reached 212 [degrees] F
the
time was recorded. For two-pot stoves
only the first
pot directly over the fire was used for
this determination.
7.
After the water boiled, the stove was
adjusted to simulate
simmering, to provide just enough heat to
keep the water
lightly boiling for 30 minutes.
In charcoal stoves this was
done by closing draft controls or loosely
blocking draft
openings on stoves without draft
controls. In the cement
wood-burning cookstoves the doors were
closed. And in the
three-stone fireplace and five-gallon
bucket, we pulled the
wood pieces outward to slow down the fire.
8.
During the test we recorded miscellaneous
observations such
as the amount of flame or smoke, how hot
the stove was to
touch, etc.
9.
At the end of the 30 minutes of simmering we
did the following
in rapid sequence:
-
recorded the water temperature,
-
weighed and recorded in pounds the amount of water
remaining, and
-
weighed and recorded in pounds the amount of unburned
fuel.
When wood was the fuel, we separated the wood and
charcoal before weighing.
10.
Calculations were made on the following:
WE - Amount
of water evaporated (pounds) = initial weight of pot
and water minus the final weight of pot
and water.
CT - Change
in water temperature ([degrees] F) = highest water temperature
minus the beginning water temperature.
CB - Weight
of charcoal burned (pounds) = initial fuel weight
minus the weight of the unburned remainder.
DW - Weight
of oven-dry wood burned (pounds) = [initial weight of
wood put in stove times 1 - MC in decimal
form] minus the
weight of wood and charcoal unburned.
FM - Weight
of moisture in fuel (pounds) = initial weight of fuel
put in stove times MC in decimal form.
EF - Stove
efficiency (PHU) = [CT x original weight of water in
pounds] + [WE x 1,050]/[DW x 8,500 - FM X
1,2001 - [pounds
of charcoal remaining x 12,500] x 100.
where:
- 1,050 was the latent heat of water
in Btu per pound at
room temperature,
- 8,500 was the heat value of oven dry
wood in Btu per
pound,
- 1,200 was the heat needed to drive
moisture out of wood
fuel in Btu per pound of water,
- 12,500 was the heat value of oven
dry charcoal in Btu
per pound,
- for charcoal stoves the denominator
was simply CB x
12,500, and
- DW and FM were considered accurate
for our use since
there was little unburned fuel.
SSC -
Standard Specific Consumption = DW/WE.
APPENDIX III
WATER BOILING TEST
DATA SHEET
DATE:
______________________________
STOVE TYPE: ______________
OPERATOR(S):
_______________________
MODIFICATIONS: ___________
TEST NUMBER:
_______________________ FUEL:
____________________
MOISTURE
CONTENT SAMPLES:
Identification
Fresh weight
Oven-dry weight MC (Green
basis)
FUEL WEIGHT
AT START: __________________ POT
WEIGHT: _____________
INITIAL
WEIGHT OF POT & WATER: _________
INITIAL WATER TEMP: _____
ELAPSED
WATER FUEL
WEIGHT
TIME
TIME TEMPERATURE
ADDED
COMMENTS
______
0_______
_________________
_______________ __________
______
5_______
_________________
_______________ __________
______
10______
_________________
_______________ __________
______
15______
_________________ _______________
__________
______
20______
_________________
_______________ __________
______
25______
_________________
_______________ __________
______
30______
_________________
_______________ __________
______
35______
_________________
_______________ __________
______
60______
_________________
_______________ __________
FINAL WEIGHT
OF POT AND WATER: _____________
WEIGHT OF
WOOD REMAINING: __________________
WEIGHT OF
CHARCOAL REMAINING: ______________
APPENDIX IV
KITCHEN PERFORMANCE TEST
DATA SHEET
STOVE TYPE:
________________________ FAMILY NAME:
___________________
LOCATION:
_____________________________________________________________
NUMBER OF
PEOPLE FED: ______________ STANDARD
ADULT EQUIVALENTS:
children 0 -
14 years _________ x 0.5 =
women over 14
years _________
x 0.8 =
men aged 15 -
59 years ________ x 1.0 =
men over 59
years _____________ x 0.8 =
NUMBER OF
MEALS COOKED: OTHER USES:
breakfast
__________
ironing
____________
lunch
__________
baking
____________
dinner
__________
others
____________
other
cooking__________
____________
WAS THERE ANY
LEFTOVER CHARCOAL IN THE STOVE?
________________
WHAT DID YOU
DO WITH IT?
WOULD YOU USE
MORE _____ OR LESS _____ FUEL FOR
SIMILAR
MEALS IN THE
CONVENTIONAL COAL POT?
GENERAL
COMMENTS:
APPENDIX V
COOKSTOVE LOCATION SHEET
STOVE MODEL:
_____________________ FEATURES:
_________________________
DATE
DATE
START
FINISH
ADDRESS
USER COMMENTS
APPENDIX VI
CONVERSION FACTORS
1 pound =
0.454 kilograms
1 kilogram =
2.2 pounds
1 Btu = 0.252
kilocalories
1 kilocalorie
= 3.968 Btus
1 Btu/pound =
2.32 Joules/gram
[degree] C =
[degree] F - 32/1.8
[degree] F =
(1.8 x [degree] C) + 32
BIBLIOGRAPHY
Baldwin,
Sam. "New Directions In Woodstove
Development." VITA
News, January 1984, pp. 3-13, 19-23.
de Silva,
Dhammika. "A Charcoal Stove From
Sri Lanka." Appropriate
Technology Vol. 7, No. 4, 1981, pp.
22-24.
Foley, Gerald
and Moss, Patricia. "Improved
Cooking Stoves In Developing
Countries."
Earthscan Technical Report No. 2, 1983,
175 pp. Illus.
Government of
Montserrat. Preliminary Data of the
1980 Commonwealth
Caribbean Population Census, Part I:
Household and
Housing Information, 1980, 26 pp.
Hassrick,
Phillip. "Umeme:
A Charcoal Stove from Kenya."
Appropriate
Technology Vol. 9, No. 1, 1982, pp. 6-7.
Joseph,
Stephen and Trussell, Jenny. Report on
Advisory Visit to
the VITA Wood Stove Project in Upper
Volta. Intermediate
Technology Consultants Ltd. report to
VITA, 1981, 52 pp.
Illus.
Singer,
H. "Improvement of Fuelwood
Cooking Stoves and Economy in
Fuelwood Consumption."
Report to the Government of Indonesia
No. 1315.
Rome, Italy: Food and
Agriculture Organization
of the United Nations, 1961, 58 pp.
Tata Energy
Research Institute. Solid Fuel Cooking
Stoves. Bombay,
India, 1980. 118 pp. Illus.
Volunteers in
Technical Assistance (VITA). Testing
the Efficiency
of Wood-Burning Cookstoves:
Provisional International
Standards.
Arlington, Virginia:
Volunteers in Technical
Assistance (VITA), 1982, 76 pp. Illus.
Yameogo,
Georges; Bussman, Paul; Simonis, Philippe; and Baldwin,
Sam.
Comparison of Improved Stoves:
Lab, Controlled Cooking,
and Family Compound Tests.
I.V.E/T.H.E. Eindhoven/GTZ/
CILSS/VITA, 1983, 67 pp. Illus.
========================================
========================================